I once accepted an order for F-16 engine lugs from our best aerospace customer—thin, triangular parts machined from 4 "-dia. (101.6mm) A-286 iron-base superalloy. I’d never cut the stuff before, but knew it was tough, and there was little chance of sawing the blanks on our hardware-store-grade bandsaw. I called Jerry, the owner of the sawing house that cut all our difficult jobs.
A few days later, he stepped through the loading door carrying a small cardboard box with a handful of ugly blanks inside. “Where did you find this stuff?” Jerry exclaimed, pointing at the box. “I went through three blades just getting you those.”
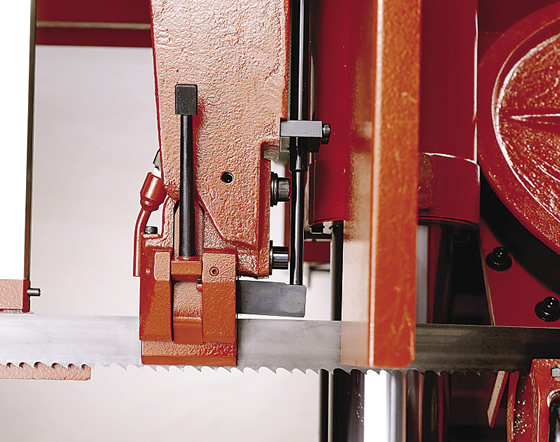
A close-up of the pulse mechanism on an Amada PCSAW330 13 " pulse-cutting bandsaw. Image courtesy Amada Machine Tools America.
We eventually found someone to saw the blanks and finished the job, but not without first losing our shirt. The lesson: Never take sawing for granted. Yet this is something far too many shops are guilty of. Inadequate equipment maintenance, poorly trained operators, improper cutting parameters and poor blade selection—these are just some of the common mistakes that lead to crooked or inconsistent blanks, wasted material, broken blades and lost production time.
Finger on the Pulse
That job was 20 years ago. If Jerry had modern equipment at his disposal, he would have made short work of that A-286. Bandsaw machine and blade manufacturers are making their wares smarter and more capable every day. An example of this is a bandsaw machine that senses cutting forces and automatically adjusts cutting parameters. Sandy Young, regional manager for Amada Machine Tools America Inc., Schaumburg, Ill., said technology such as this not only makes life much simpler for operators, but also provides straighter, faster cuts.
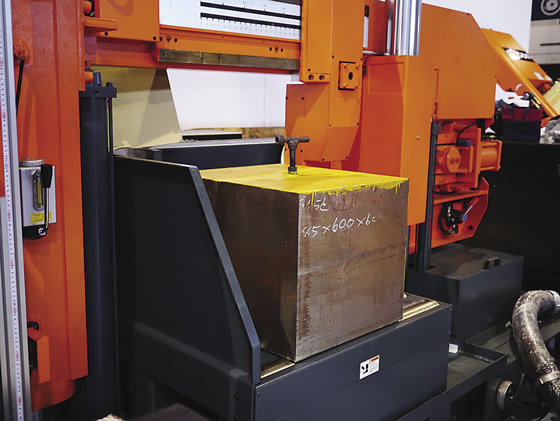
Heavy, wide cuts such as this one can cause chip evacuation problems. Deep blade gullets and flood coolant increase productivity and improve blade life. Image courtesy Cosen Saws USA.
“I call it smart cutting,” Young said. “It removes much of the thought process in sawing, automatically setting the feed, speed and cutting pressure based on preloaded control parameters. If the head senses resistance in the cut, the controller will pick up on that and signal the hydraulic system to provide more fluid to the down-feed side of the cylinder, maintaining a consistent, straight level of cutting. Also, the computer will monitor the blade speed and automatically adjust to whatever feed rate is being used at that time. The operator doesn’t have to worry about any of those things.”
Young noted that machine shop customers are demanding faster lead times and lower priced parts. One often overlooked part of this equation is the first step in machining: sawing blanks. “The biggest failure is not treating a saw as a CNC machine tool,” he said. “In today’s price-conscious world, you have to consider every detail. Unfortunately, as shop owners modernize their equipment, the last thing they consider is the saw.”
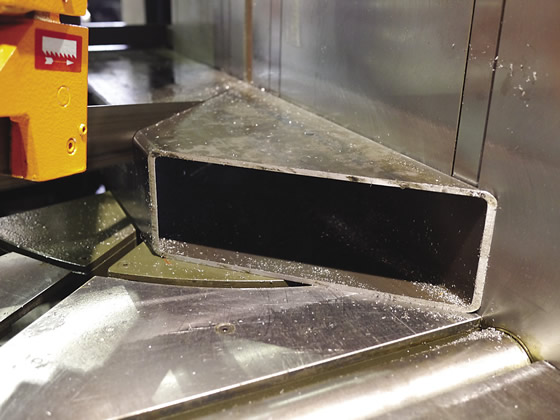
Mitering is a common bandsawing operation, but one that’s prone to deflection as the blade enters the angled cut. Controls that automatically adjust the down-feed pressure and blade speed improve blade life and part quality. Image courtesy Cosen Saws USA.
A big part of the modernization Young promotes is improved blade control. Aside from automatically speeding up or slowing down as the need arises, Amada bandsaws offer pulse cutting technology, which uses a guide arm-mounted servomotor to apply alternating pulses of pressure to the saw guides approximately 10 times each second (see photo on page 90). According to Young, this forces the blade to penetrate materials faster and more aggressively than conventional bandsaws, increasing material removal in titanium and nickel-based alloys from 3 to 4 sq. in./min. (76.2 to 101.6 sq. mm/min.) to 25 sq. in./min. (635 sq. mm/min.) or more when using Amada’s Axcela G carbide blade.
Good Vibrations
Michael Finklea, director of North American sales and marketing for Cosen Saws USA, Charlotte, N.C., said one of the problems with sawing difficult-to-cut materials is the vibration caused when the blade teeth enter and exit the cut. Controlling this vibration is the job of Cosen’s V_Drive system, which, as Finklea explained, uses a combination of hardware and software to manipulate the drive motor frequency, thus canceling the vibration and harmonics.
“It’s basically noise cancellation, similar to what happens in a pair of high-quality headphones,” Finklea said. “We suppress vibration by applying a frequency opposite that produced during cutting, reducing harmonics at the blade by approximately 38 percent. We’ve had some real success stories, but as a rule, we tell customers to expect cutting rates to improve by one and a half to two times faster than what they’re used to. Sometimes far faster.”
For example, a Cosen customer was sawing a 48 "-dia. (1,219mm) × 11 "-thick (279.4mm) wall in a proprietary brand of centripetal cast tubing, a hard and abrasive material. Where previous methods yielded a cycle time of 16 hours per cut and consumed one carbide-tipped blade per cut, V_Drive reduced the time per cut to 6½ hours, with each blade completing three cuts before giving up the ghost. Bimetal blades offered similar results when cutting 17-4 PH stainless steel. Finklea said V_Drive increases blade speed from 85 to 135 sfm (25.9 to 41.1 m/min.) or more.
Iron Town
The key to vibration reduction is cast iron construction, according to Joe Suydam, inside sales and marketing specialist for Behringer Saws Inc., Morgantown, Pa. “As with any machine tool, a rigid frame is critical to tool life and part accuracy.” Behringer uses cast iron for the bow frame and other major components, “which we feel is far better at damping vibration than steel weldments,” he said.
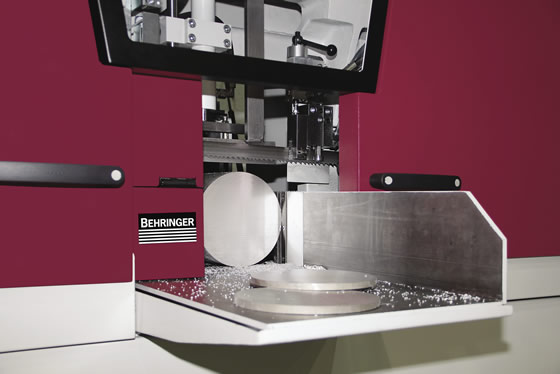
A cast iron frame and hydraulic blade tensioning eliminate much of the vibration in bandsawing operations. Image courtesy Behringer Saws.
That’s not to say there are no electronics involved. As Suydam explained, Behringer saws are equipped with a servo ballscrew system and pressure sensors to monitor the cutting force and make adjustments to optimize the process. Hydraulic blade tensioning further reduces any residual vibration not absorbed by the saw’s iron frame, and the control will sense blade deflection during the cut, operating within user-defined parameters to adjust feed rate or even shut down the operation if needed.
Ease of use is another feature saw builders strive for. Auto feed control is one example. “We have a data-base of specific materials within the control,” Suydam said. “This gives the operator good feeds and speeds as a starting point, rather than relying on the sound of the cut or color of the chips to determine sawing parameters. There are also built-in functions to accelerate or decelerate based on where you’re at in the bar or channel. This helps avoid problems with gouging at the start of the cut, for example, where only a few teeth are engaged, reducing tooth breakage and premature blade wear.”
Double Down
Gary Toddish agreed that solid machine construction is paramount to sawing success, but added that the choice of saw is equally important. A district sales manager for saw builder Marvel Manufacturing Co. Inc., Oshkosh, Wis., Toddish said there are two basic types of horizontal saws: scissor saws, as their name implies, use a pivoting design similar to a set of household shears, while double-column saws act like a guillotine. Of the two, the double-column design is more suitable for difficult materials and high production rates.
“Double columns work best where higher feed forces are necessary,” Toddish said. “Since the blade support is better, they tend to give quieter, smoother cuts than the more common scissors-style saw, which translates to less vibration and good blade life. I have customers that own both, and they say the double-column design cuts 20 percent faster overall.”
Operator training is also critical. While programming the CNC on a modern sawing machine requires little more than inputting material type and diameter, that doesn’t guarantee good results. “Cutting performance relies on more than the right feeds and speeds,” Toddish pointed out. “You can cut an aluminum beer can using the coarsest blade available, provided the machine is controllable enough. That doesn’t mean it’s efficient. It’s the operator’s job to always use the correct blade for any given material and make sure the cutting fluid is at the recommended concentration for sawing. Also, the guides and tensioners have to be maintained, the saw kept clean—there are all sorts of considerations.”
Breaking In
Matt Lacroix, director of brand marketing at Lenox Tools, a saw blade manufacturer based in East Longmeadow, Mass., agreed that preventive maintenance is an often-overlooked component of saw operation. “You want to make sure there’s a preventive maintenance schedule in place. Whether that’s monthly, quarterly or every 6 months, it’s still important to have it; otherwise, at some point you’ll find yourself with a broken saw and no way to cut parts,” he said.
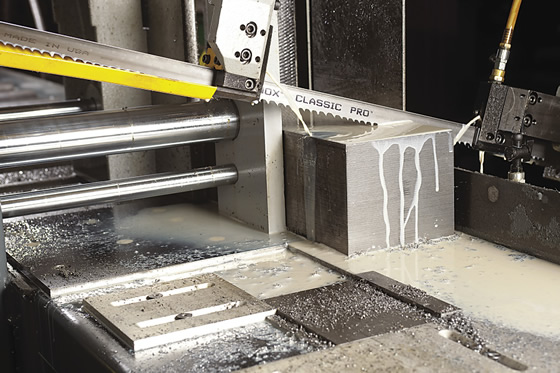
Because of their toughness and relative low cost, bimetal bandsaw blades are widely applied. Image courtesy Lenox Tools.
Lacroix is also a proponent of proper blade break-in, a process whereby the blade is run at 20 to 50 percent of the normal feed rate for the first few cuts. This removes microburrs left from the blade manufacturing process and avoids the chips and fractures that will form with aggressive initial handling. On older machines, this was left to the operator, but some of today’s saw controls have preprogrammed cycles that ease saw blades into a long and useful life.
He also recommends carbide-tipped blades instead of bimetal ones when cutting difficult materials used in aerospace, power generation and medical parts. “Much of the technology used in saws lends itself well to carbide. This includes vibration damping and automatic feed adjustments, as well as beefier machine construction, allowing for the higher cutting speeds.”
Lacroix admitted the price tag for carbide-tipped blades may be three times that of bimetal blades, but said the blade life and increased productivity easily justifies the additional expense—even for the high-mix, low-volume applications seen in many job shops.
If your shop is one of those that mistreats its bandsaw, it might be time to remedy the situation. Bandsaws are the first machining step with many parts—crooked slugs, inconsistent lengths and nasty burrs can drag down production for downstream operations. And because there’s often a single bandsaw serving multiple machines, the stakes can be quite high if the saw takes an unplanned vacation due to poor maintenance. So keep it clean, apply the right saw blade and cutting parameters and keep an eye on blade life. CTE
About the Author: Kip Hanson is contributing editor for CTE. Contact him at (520) 548-7328 or [email protected].
Predicting failure, preventing damage
Having a bandsaw blade break halfway through an expensive workpiece is enough to ruin anyone’s day. Sawing machine builders offer tools to manage blade life, but so many variables exist in the sawing process that some level of unpredictability remains. An imperfectly maintained machine, inconsistent material, operator error—any of these can throw the best saw blade life calculations out the window, leading to downtime and a potentially dangerous situation if the blade runs amok.
All that may be about to change. Cosen Saws USA, in collaboration with the Taiwan government and the Center for Intelligent Maintenance Systems at the University of Cincinnati, is working on a predictive analysis system that monitors sawing conditions and sends an alert when blade life reaches a preset percentage. “It’s based on a series of sensors mounted on various parts of the machine, collecting such information as temperature, motor speed and hydraulic pressure,” said Michael Finklea at Cosen. “In some cases, there may be 10,000 data points per second coming back to a data acquisition unit, which then relays the information to a cloud-based server.” Finklea expects the first commercial versions to be available this month.
It’s a little like weather forecasting, he explained, in that a series of events occurs, producing data that can be used to make predictions. In this case, blade failure can be anticipated well in advance. Further, it’s possible to deploy these data-collection systems to other types of equipment, such as lathes and mills. And because the data and associated software resides in the cloud, it’s a simple matter to share information across multiple machines and locations, allowing technicians and plant managers to make proactive decisions before disaster strikes.
The company is even working on a smartphone app, making it convenient for those same people to perform remote monitoring and predictive analysis of whatever machine tools they are responsible for. “Prior to this, knowing if you should start cutting with a used blade has always been a guess,” Finklea said. “Now you can maximize tool usage, while also assuring that you’ll get a good part.”
—K. Hanson
Contributors
Amada Machine Tools America Inc.
(800) 877-4729
www.amadamachinetools.com
Behringer Saws Inc.
(610) 286-9777
www.behringersaws.com
Cosen Saws USA
(877) SAWING1
www.cosen.com
Lenox Tools
(800) 628-8810
www.lenoxtools.com
Marvel Manufacturing Co. Inc.
(800) 472-9464
www.marvelsaws.com
Related Glossary Terms
- abrasive
abrasive
Substance used for grinding, honing, lapping, superfinishing and polishing. Examples include garnet, emery, corundum, silicon carbide, cubic boron nitride and diamond in various grit sizes.
- alloys
alloys
Substances having metallic properties and being composed of two or more chemical elements of which at least one is a metal.
- bandsaw
bandsaw
Machine that utilizes an endless band, normally with serrated teeth, for cutoff or contour sawing. See saw, sawing machine.
- bandsaw blade ( band)
bandsaw blade ( band)
Endless band, normally with serrated teeth, that serves as the cutting tool for cutoff or contour band machines.
- bandsawing
bandsawing
Long, endless band with many small teeth traveling over two or more wheels (one is a driven wheel, and the others are idlers) in one direction. The band, with only a portion exposed, produces a continuous and uniform cutting action with evenly distributed low, individual tooth loads. Often called band machining.
- computer numerical control ( CNC)
computer numerical control ( CNC)
Microprocessor-based controller dedicated to a machine tool that permits the creation or modification of parts. Programmed numerical control activates the machine’s servos and spindle drives and controls the various machining operations. See DNC, direct numerical control; NC, numerical control.
- coolant
coolant
Fluid that reduces temperature buildup at the tool/workpiece interface during machining. Normally takes the form of a liquid such as soluble or chemical mixtures (semisynthetic, synthetic) but can be pressurized air or other gas. Because of water’s ability to absorb great quantities of heat, it is widely used as a coolant and vehicle for various cutting compounds, with the water-to-compound ratio varying with the machining task. See cutting fluid; semisynthetic cutting fluid; soluble-oil cutting fluid; synthetic cutting fluid.
- cutting fluid
cutting fluid
Liquid used to improve workpiece machinability, enhance tool life, flush out chips and machining debris, and cool the workpiece and tool. Three basic types are: straight oils; soluble oils, which emulsify in water; and synthetic fluids, which are water-based chemical solutions having no oil. See coolant; semisynthetic cutting fluid; soluble-oil cutting fluid; synthetic cutting fluid.
- cutting force
cutting force
Engagement of a tool’s cutting edge with a workpiece generates a cutting force. Such a cutting force combines tangential, feed and radial forces, which can be measured by a dynamometer. Of the three cutting force components, tangential force is the greatest. Tangential force generates torque and accounts for more than 95 percent of the machining power. See dynamometer.
- feed
feed
Rate of change of position of the tool as a whole, relative to the workpiece while cutting.
- sawing
sawing
Machining operation in which a powered machine, usually equipped with a blade having milled or ground teeth, is used to part material (cutoff) or give it a new shape (contour bandsawing, band machining). Four basic types of sawing operations are: hacksawing (power or manual operation in which the blade moves back and forth through the work, cutting on one of the strokes); cold or circular sawing (a rotating, circular, toothed blade parts the material much as a workshop table saw or radial-arm saw cuts wood); bandsawing (a flexible, toothed blade rides on wheels under tension and is guided through the work); and abrasive sawing (abrasive points attached to a fiber or metal backing part stock, could be considered a grinding operation).
- sawing machine ( saw)
sawing machine ( saw)
Machine designed to use a serrated-tooth blade to cut metal or other material. Comes in a wide variety of styles but takes one of four basic forms: hacksaw (a simple, rugged machine that uses a reciprocating motion to part metal or other material); cold or circular saw (powers a circular blade that cuts structural materials); bandsaw (runs an endless band; the two basic types are cutoff and contour band machines, which cut intricate contours and shapes); and abrasive cutoff saw (similar in appearance to the cold saw, but uses an abrasive disc that rotates at high speeds rather than a blade with serrated teeth).
- sawing machine ( saw)2
sawing machine ( saw)
Machine designed to use a serrated-tooth blade to cut metal or other material. Comes in a wide variety of styles but takes one of four basic forms: hacksaw (a simple, rugged machine that uses a reciprocating motion to part metal or other material); cold or circular saw (powers a circular blade that cuts structural materials); bandsaw (runs an endless band; the two basic types are cutoff and contour band machines, which cut intricate contours and shapes); and abrasive cutoff saw (similar in appearance to the cold saw, but uses an abrasive disc that rotates at high speeds rather than a blade with serrated teeth).