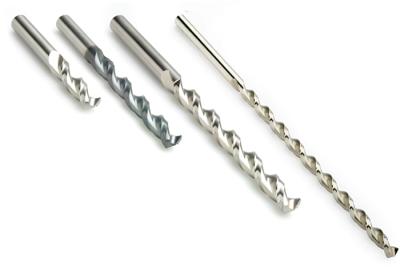
Dormer PFX premium cobalt HSS drills are available in screw machine, jobber, taper and extra-length designs. Providing options for drilling applications, the PFX is ideal for most engineering materials drilling 3 diameters deep (A920, A921), 6 diameters deep (A900, A901), 10 diameters deep (A940, A941) and 15 diameters deep (A976, A977, A978).
All drills feature a parabolic flute design for increased chip space and improved chip evacuation capabilities. This design allows greater hole depths to be achieved, in some cases without the need for pecking. A thick web increases the structural strength of the drill for enhanced rigidity and minimizes the risk of drill breakage. In addition, the special point geometry promotes excellent centering, eliminating the requirement for a pilot hole, and reduces thrust force and power requirements.
Available in bright finish across the full range, a Smooth-Flow coating option is available on screw machine, jobber and taper lengths. This AlCrN top coating reduces the coefficient of friction, increases wear resistance and, in combination with the parabolic flute, eliminates chip packing at greater depths.
Contact Details
Related Glossary Terms
- centering
centering
1. Process of locating the center of a workpiece to be mounted on centers. 2. Process of mounting the workpiece concentric to the machine spindle. See centers.
- high-speed steels ( HSS)
high-speed steels ( HSS)
Available in two major types: tungsten high-speed steels (designated by letter T having tungsten as the principal alloying element) and molybdenum high-speed steels (designated by letter M having molybdenum as the principal alloying element). The type T high-speed steels containing cobalt have higher wear resistance and greater red (hot) hardness, withstanding cutting temperature up to 1,100º F (590º C). The type T steels are used to fabricate metalcutting tools (milling cutters, drills, reamers and taps), woodworking tools, various types of punches and dies, ball and roller bearings. The type M steels are used for cutting tools and various types of dies.
- wear resistance
wear resistance
Ability of the tool to withstand stresses that cause it to wear during cutting; an attribute linked to alloy composition, base material, thermal conditions, type of tooling and operation and other variables.
- web
web
On a rotating tool, the portion of the tool body that joins the lands. Web is thicker at the shank end, relative to the point end, providing maximum torsional strength.