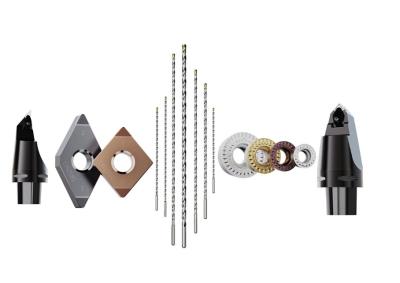
To overcome various machining challenges and boost productivity, Seco has introduced new toolholders, PCBN inserts, round carbide inserts and extra-long solid carbide drills with enhanced versatility and tool life. These innovative products are aimed at applications ranging from general ISO turning to high-volume hard turning and deep hole drilling.
Cost-saving X-tra Long Solid Carbide Drills - 40xD-60xD
Manufacturers that drill holes at depths from 40xD to 60xD want to lengthen tool life and reduce tooling costs. New Seco X-tra Long Solid Carbide Drills provide more than 15% greater tool life than other extra-long solid carbide drills.
Seco X-tra Long Solid Carbide Drills achieve fast, reliable performance in steel, stainless steel and cast iron, as well as good performance in Inconel®, titanium and hardened steel, all on standard machining centers.
Unique tool geometry and coating eliminate chipping and sudden breakage while they minimize flank and center wear. A ground edge prep produces smoother cutting edges, greater evenness and closer tolerances than brushing. Seco X-tra Long Solid Carbide Drills maintain specified drilling depth after up to three reconditioning cycles.
CH1050 and CH2581 PCBN inserts for process stability
Two new Seco grades of PCBN inserts offer ideal performance in high-volume production of automotive and other industry components. The CH1050 grade is designed for finishing and the CH2581 for semi-interrupted cuts.
With a substrate grade and unique Seco nanolaminate PVD coating designed to achieve high surface quality requirements, CH1050 also offers high-accuracy edge prep through a new grinding process. Designed for extended tool life and lower cost per part, CH1050 promotes high output and reduced scrap or rework.
CH2581 achieves greater process stability and reduced tool breakage with a versatile, forgiving grade specifically designed for semi-interrupted cuts. Its high-accuracy edge prep and next-generation Seco PVD coating enable faster speeds and higher throughput for reduced part costs.
MF2 chipbreaker on RCMT/RCGT round, positive-style ISO-turning carbide inserts with chip control
Many round turning inserts suffer from poor chip control, but Seco MF2 chipbreaker on RCGT/RCMT inserts maintains favorable chip control at higher speeds and feeds, especially with dynamic turning. One series of stable, durable carbide round insert grades handles a wide range of turning operations from roughing to finish turning.
Seco´s unique chipbreaker geometry and strong insert shape provide versatile, reliable performance in tough operations, including heavy intermittence and rough skin. In a general engineering environment with materials ranging from smeary low-carbon steels to stainless steels, titanium and heat-resistant super alloys (HRSA), these versatile inserts outperform pointed tools.
On parts with wide, deep grooves, pockets or cavities - even in difficult-to-cut materials - MF2 chipbreaker on RCMT/RCGT inserts tackles complex parts with fast production.
Better surface finishes with Seco-Capto MTM JETI Toolholders for general ISO turning
Seco have utilized their unique 3D-printed coolant clamp to deliver Jetstream Tooling® high-pressure cutting fluid directly to the cutting edge. With a range of single-screw coolant clamp options for specific applications and depths of cut, these toolholders provide fast setup and indexing, making chip control less of a challenge on 45° B-axis multi-tasking machines.
Seco-Capto MTM JETI Toolholders allow for the use of shorter tooling with greater reach, less overhang and reduced collision risk. The decrease in vibration and chatter improve machining results, even with materials that require high-pressure cutting fluid. The toolholder design also enables shops to optimize production and use the same machining tools on more than one spindle.
Seco innovation for production efficiency
The recently launched tools, toolholders and chipbreakers move manufacturers toward better results easier, more quickly and with cost savings. "We're focused on developing new ways for our customers to solve age old problems while taking full advantage of their machine tools," said Mia Bökmark, Vice President Product Offer & Innovation at Seco. "We draw on more than 80 years of toolmaking experience to offer solutions for the real challenges in every shop."
Contact Details
Related Glossary Terms
- alloys
alloys
Substances having metallic properties and being composed of two or more chemical elements of which at least one is a metal.
- brushing
brushing
Generic term for a curve whose shape is controlled by a combination of its control points and knots (parameter values). The placement of the control points is controlled by an application-specific combination of order, tangency constraints and curvature requirements. See NURBS, nonuniform rational B-splines.
- centers
centers
Cone-shaped pins that support a workpiece by one or two ends during machining. The centers fit into holes drilled in the workpiece ends. Centers that turn with the workpiece are called “live” centers; those that do not are called “dead” centers.
- chatter
chatter
Condition of vibration involving the machine, workpiece and cutting tool. Once this condition arises, it is often self-sustaining until the problem is corrected. Chatter can be identified when lines or grooves appear at regular intervals in the workpiece. These lines or grooves are caused by the teeth of the cutter as they vibrate in and out of the workpiece and their spacing depends on the frequency of vibration.
- chipbreaker
chipbreaker
Groove or other tool geometry that breaks chips into small fragments as they come off the workpiece. Designed to prevent chips from becoming so long that they are difficult to control, catch in turning parts and cause safety problems.
- coolant
coolant
Fluid that reduces temperature buildup at the tool/workpiece interface during machining. Normally takes the form of a liquid such as soluble or chemical mixtures (semisynthetic, synthetic) but can be pressurized air or other gas. Because of water’s ability to absorb great quantities of heat, it is widely used as a coolant and vehicle for various cutting compounds, with the water-to-compound ratio varying with the machining task. See cutting fluid; semisynthetic cutting fluid; soluble-oil cutting fluid; synthetic cutting fluid.
- cutting fluid
cutting fluid
Liquid used to improve workpiece machinability, enhance tool life, flush out chips and machining debris, and cool the workpiece and tool. Three basic types are: straight oils; soluble oils, which emulsify in water; and synthetic fluids, which are water-based chemical solutions having no oil. See coolant; semisynthetic cutting fluid; soluble-oil cutting fluid; synthetic cutting fluid.
- grinding
grinding
Machining operation in which material is removed from the workpiece by a powered abrasive wheel, stone, belt, paste, sheet, compound, slurry, etc. Takes various forms: surface grinding (creates flat and/or squared surfaces); cylindrical grinding (for external cylindrical and tapered shapes, fillets, undercuts, etc.); centerless grinding; chamfering; thread and form grinding; tool and cutter grinding; offhand grinding; lapping and polishing (grinding with extremely fine grits to create ultrasmooth surfaces); honing; and disc grinding.
- hard turning
hard turning
Single-point cutting of a workpiece that has a hardness value higher than 45 HRC.
- low-carbon steels
low-carbon steels
Group of carbon steels designated by American Iron and Steel Institute numerical classification as AISI 1005, 1006, 1008, etc., up to AISI 1026, for a total of 16 grades. They are softer and more ductile than other carbon steels. Composition of low-carbon steels is 0.06 to 0.28 percent carbon, 0.25 to 1.00 percent manganese, 0.040 percent (maximum) phosphorus and 0.050 percent (maximum) sulfur. See high-carbon steels; medium-carbon steels.
- physical vapor deposition ( PVD)
physical vapor deposition ( PVD)
Tool-coating process performed at low temperature (500° C), compared to chemical vapor deposition (1,000° C). Employs electric field to generate necessary heat for depositing coating on a tool’s surface. See CVD, chemical vapor deposition.
- polycrystalline cubic boron nitride ( PCBN)
polycrystalline cubic boron nitride ( PCBN)
Cutting tool material consisting of polycrystalline cubic boron nitride with a metallic or ceramic binder. PCBN is available either as a tip brazed to a carbide insert carrier or as a solid insert. Primarily used for cutting hardened ferrous alloys.
- stainless steels
stainless steels
Stainless steels possess high strength, heat resistance, excellent workability and erosion resistance. Four general classes have been developed to cover a range of mechanical and physical properties for particular applications. The four classes are: the austenitic types of the chromium-nickel-manganese 200 series and the chromium-nickel 300 series; the martensitic types of the chromium, hardenable 400 series; the chromium, nonhardenable 400-series ferritic types; and the precipitation-hardening type of chromium-nickel alloys with additional elements that are hardenable by solution treating and aging.
- toolholder
toolholder
Secures a cutting tool during a machining operation. Basic types include block, cartridge, chuck, collet, fixed, modular, quick-change and rotating.
- turning
turning
Workpiece is held in a chuck, mounted on a face plate or secured between centers and rotated while a cutting tool, normally a single-point tool, is fed into it along its periphery or across its end or face. Takes the form of straight turning (cutting along the periphery of the workpiece); taper turning (creating a taper); step turning (turning different-size diameters on the same work); chamfering (beveling an edge or shoulder); facing (cutting on an end); turning threads (usually external but can be internal); roughing (high-volume metal removal); and finishing (final light cuts). Performed on lathes, turning centers, chucking machines, automatic screw machines and similar machines.