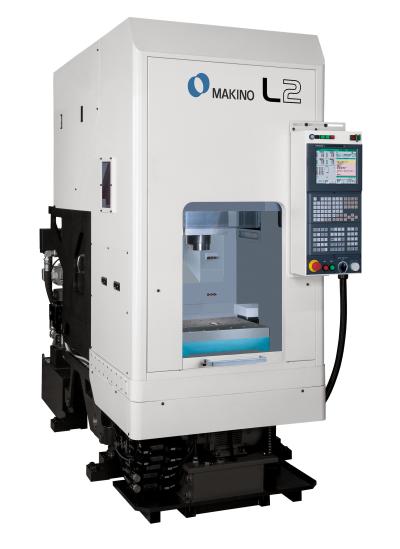
Makino offers the L2 vertical machining center for high-volume, small-part manufacturing. Combining a rigid construction, compact footprint and flexible spindle design, the L2 offers a highly stable and reliable machine platform for fully unattended, around-the-clock part processing, according to the company.
“The minimal floor-space design and wide range of highly productive standard specifications make the L2 an ideal solution for any type of high-volume, small-component processing,” said William Howard, vertical product line manager at Makino. “Given the small size of the machine, it can be effectively employed in virtually any type of workpiece flow arrangement, ranging from manual part transfers to automated part movement facilitated by robotic systems. The L2 can be deployed to meet the specific needs of any manufacturing environment.”
The L2 vertical machining center features a compact footprint of 850mm wide by 2,130mm long (33.46 inches by 83.86 inches), including cooling tank. The X-, Y- and Z-axis travels on the machine are 400mm by 300mm by 300mm (15.74 inches by 11.81 inches by 11.81 inches). A standard, integrated A-axis rotary table and automatic pallet-change system can accommodate workpiece sizes up to 413mm by 267mm by 215mm (16.26 inches by 10.51 inches by 8.46 inches). The A-axis provides six integral ports for hydraulics and pneumatics to support fully automated fixtures. An optional fixed-table configuration without pallet-change system is also available, and can accommodate a maximum workpiece size of 413mm by 267mm by 215mm (16.26 inches by 10.51 inches by 8.46 inches).
Noncut times, including positioning and chip-to-chip times, are dramatically reduced with rapid traverse rates of 48,000mm/minute (1,890 inches/minute) and acceleration rates of 2.0G, 1.5G and 1.7G in the X-, Y- and Z-axes respectively. The standard A-axis rotary table and automatic pallet changer further enhance productive capabilities, providing 3-second pallet changeovers to maximize spindle utilization and machine productivity. Configured with 0.05-micron scale feedback and the highly rigid machine design, the L2 machine is both quick and highly accurate.
Standardly equipped with a 16,000-rpm, HSK-A50 spindle, the L2 accommodates a range of applications. Through-spindle, nozzle, overhead shower and even fixture wash coolant systems provide quick and efficient evacuation of chips from the machine work area. Completing the process, a strategically placed, center trough chip conveyor rapidly removes the chip from the machine. Additionally, the L2 features a 30-tool-capacity automatic toolchanger that can accommodate tooling up to 80mm (3.14 inches) in diameter, 250mm (9.84 inches) in length and 5 kg (11 lbs.) in weight. An optional 8,000-rpm spindle configuration is also available.
The A-axis rotary table facilitates access to multiple sides of the workpiece in a single setup, and the automatic pallet changer delivers a fast 3-second pallet change. Outfitted with wide, front-access, automatic doors, the L2 is quick and convenient for manual loading applications, and ready for integration into a wide variety of automated load and unload arrangements.
The L2 is designed for simple and easy integration within a variety of automated transfer and loading configurations, including exterior loading arms, gantry loaders, and fixed or movable robot loaders. These automated configurations help maximize the capabilities and value of the L2, resulting in higher production rates, shorter lead-times, reduced labor costs and saving significant floor space.
Contact Details
Related Glossary Terms
- automatic toolchanger
automatic toolchanger
Mechanism typically included in a machining center that, on the appropriate command, removes one cutting tool from the spindle nose and replaces it with another. The changer restores the used tool to the magazine and selects and withdraws the next desired tool from the storage magazine. The changer is controlled by a set of prerecorded/predetermined instructions associated with the part(s) to be produced.
- coolant
coolant
Fluid that reduces temperature buildup at the tool/workpiece interface during machining. Normally takes the form of a liquid such as soluble or chemical mixtures (semisynthetic, synthetic) but can be pressurized air or other gas. Because of water’s ability to absorb great quantities of heat, it is widely used as a coolant and vehicle for various cutting compounds, with the water-to-compound ratio varying with the machining task. See cutting fluid; semisynthetic cutting fluid; soluble-oil cutting fluid; synthetic cutting fluid.
- fixture
fixture
Device, often made in-house, that holds a specific workpiece. See jig; modular fixturing.
- machining center
machining center
CNC machine tool capable of drilling, reaming, tapping, milling and boring. Normally comes with an automatic toolchanger. See automatic toolchanger.
- rapid traverse
rapid traverse
Movement on a CNC mill or lathe that is from point to point at full speed but, usually, without linear interpolation.
- toolchanger
toolchanger
Carriage or drum attached to a machining center that holds tools until needed; when a tool is needed, the toolchanger inserts the tool into the machine spindle. See automatic toolchanger.