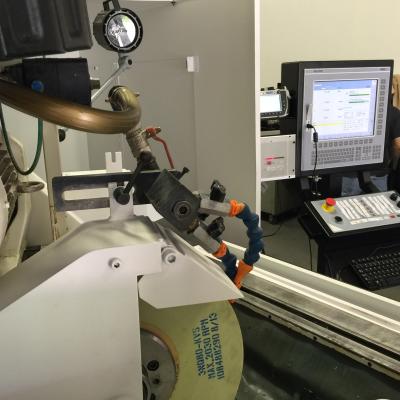
Advanced CNC systems from NUM are helping U.S. machine tool control specialist CNC Onestop Inc. to maintain its competitive market edge through use of ultraprecise positioning techniques. Based in Xenia, Ohio, and also operating in Toronto, Canada, CNC Onestop is a CNC engineering company that specializes in full CNC, motor and drive retrofits for machine tools, as well as machine rebuilds and troubleshooting. Its main area of business is in grinding machines, including OD, ID, nonround and punch grinding, as well as thread grinding, that provide submicron accuracy. The company’s customer base spans a diverse mix of aerospace, medical, marine, defense and high-tech industries.
According to CNC Onestop’s president, Ven Swaminathan, “We aim to develop solutions for machine tool applications that are deemed impossible by competitors. Many of the grinding machines that we retrofit are required to work to sub-micron accuracies. To help achieve this, we need CNC technology with exceptionally precise positioning capabilities. NUM is the leader in this specialized area of CNC and their application support is unparalleled, so we have chosen to standardize on their open architecture hardware and software for all future grinding machine retrofit projects.”
The core of NUM’s cylindrical grinding CNC solutions is a flexible software package known as ProCAM. This features a highly intuitive graphical human-machine interface (HMI), which uses simple conversational style programming. It is used in conjunction with embedded CNC grinding and dressing cycles, with direct hyperlinks to CAD files or other pertinent grinding production data, to facilitate efficient manufacture of a diverse range of workpieces with a variety of wheel forms. ProCAM software is designed primarily to address the requirements of OD, ID or OD/ID with either a horizontal or vertical machine layout.
NUM’s PC-based ProCAM software can be easily and quickly configured for a variety of machine configurations. The basic configuration has the X-axis or radial direction into the part and the Z-axis or axial along the length of the part. The same X/Z axes can be used to drive the dressing operations, or alternatively the software can also set up to manage a rear mounted independent U/W dressing axis set. Embedded grinding cycles include OD/ID plunge/multiplunge, plunge with inclined axes, oscillating plunge/multiplunge, cylinder traverse, complex profile traverse, taper traverse, oscillating shoulder, shoulder traverse and shoulder cylinder blend.
ProCAM also supports a variety of auxiliary grinding functions, including straight and special profile wheels, roller dressing, automatic wheel profiling, in-process dressing and automatic wheel surface speed calculations.
Steven Schilling, general manager of NUM Corp., points out, “Our ProCAM grinding solutions are based on NUM’s latest-generation Flexium+ CNC platform. This provides machine tool retrofitters and manufacturers with a modular and fully scalable CNC system that is very cost-effective across a wide range of applications. We are currently supplying Flexium+ 8 systems to CNC Onestop, which are extremely flexible and powerful configurations. CNC Onestop’s decision to base its future cylindrical grinding developments on NUM’s CNC products is a great accolade and we wish them every success”.
Related Glossary Terms
- computer numerical control ( CNC)
computer numerical control ( CNC)
Microprocessor-based controller dedicated to a machine tool that permits the creation or modification of parts. Programmed numerical control activates the machine’s servos and spindle drives and controls the various machining operations. See DNC, direct numerical control; NC, numerical control.
- computer-aided design ( CAD)
computer-aided design ( CAD)
Product-design functions performed with the help of computers and special software.
- cylindrical grinding
cylindrical grinding
Grinding operation in which the workpiece is rotated around a fixed axis while the grinding wheel is fed into the outside surface in controlled relation to the axis of rotation. The workpiece is usually cylindrical, but it may be tapered or curvilinear in profile. See centerless grinding; grinding.
- dressing
dressing
Removal of undesirable materials from “loaded” grinding wheels using a single- or multi-point diamond or other tool. The process also exposes unused, sharp abrasive points. See loading; truing.
- grinding
grinding
Machining operation in which material is removed from the workpiece by a powered abrasive wheel, stone, belt, paste, sheet, compound, slurry, etc. Takes various forms: surface grinding (creates flat and/or squared surfaces); cylindrical grinding (for external cylindrical and tapered shapes, fillets, undercuts, etc.); centerless grinding; chamfering; thread and form grinding; tool and cutter grinding; offhand grinding; lapping and polishing (grinding with extremely fine grits to create ultrasmooth surfaces); honing; and disc grinding.
- grinding machine
grinding machine
Powers a grinding wheel or other abrasive tool for the purpose of removing metal and finishing workpieces to close tolerances. Provides smooth, square, parallel and accurate workpiece surfaces. When ultrasmooth surfaces and finishes on the order of microns are required, lapping and honing machines (precision grinders that run abrasives with extremely fine, uniform grits) are used. In its “finishing” role, the grinder is perhaps the most widely used machine tool. Various styles are available: bench and pedestal grinders for sharpening lathe bits and drills; surface grinders for producing square, parallel, smooth and accurate parts; cylindrical and centerless grinders; center-hole grinders; form grinders; facemill and endmill grinders; gear-cutting grinders; jig grinders; abrasive belt (backstand, swing-frame, belt-roll) grinders; tool and cutter grinders for sharpening and resharpening cutting tools; carbide grinders; hand-held die grinders; and abrasive cutoff saws.
- inner diameter ( ID)
inner diameter ( ID)
Dimension that defines the inside diameter of a cavity or hole. See OD, outer diameter.
- outer diameter ( OD)
outer diameter ( OD)
Dimension that defines the exterior diameter of a cylindrical or round part. See ID, inner diameter.
- profiling
profiling
Machining vertical edges of workpieces having irregular contours; normally performed with an endmill in a vertical spindle on a milling machine or with a profiler, following a pattern. See mill, milling machine.