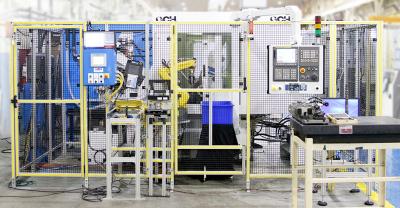
GCH Machinery says it has both the machine tool remanufacturing experience and know-how to take your older machine and restore it to the original OEM specifications (and beyond) using the most modern mechanical and electronic technology available. The result is a high-precision machine or grinding cell that has been remanufactured to your exact requirements, fully supported by GCH Machinery's technical staff.
Before anyone touches a machine, the company meet with you to go over your requirements in depth. The GCH team will offer suggestions to allow you to get more production out of your grinding machine. If warranted, GCH examines your grinding application to see where processes can be honed and improved. Company employees are known for their ability to come up with creative solutions to your manufacturing challenges.
The remanufacturing services include:
- All ways, slides and moving surfaces are precision hand scraped and flaked.
- All spindles are ceramic coated or chrome plated and ground.
- New precision-scraped Filmatic bearings that are matched to the new spindle surfaces
- All bearings, roller, ball and angular contact are replaced with new matching precision sets
- New hydraulic valves
- New steel pipes, hydraulic hoses and fittings
- New hydraulic pumps, filters and motors.
- New electrical, motor starter and fuse blocks
- New panel disconnects, wiring and transformers
- New NEMA 12 electrical enclosures
- New SLC, PLC and CNC controls
- New control console color CRT and push buttons (option)
- Complete AutoCad schematics (electrical, hydraulic, pneumatic)
- New auto lubrication controls, new lube blocks, steel lines and fitting
- New motion control devices, servos and steppers
- New precision ground ball screws and nuts
- New grinder tooling
- New automation for loaders and unloaders
- New gages for in process and post process
- New auto wheel balancers
- New constant surface footage
- Special load monitoring devices
- Choice of color-customer selection
- Completely re-tooled set-up and SPC and CPK run-off on your part
- Complete turnkey package
- Global warranty standard
Contact Details
Related Glossary Terms
- computer numerical control ( CNC)
computer numerical control ( CNC)
Microprocessor-based controller dedicated to a machine tool that permits the creation or modification of parts. Programmed numerical control activates the machine’s servos and spindle drives and controls the various machining operations. See DNC, direct numerical control; NC, numerical control.
- grinding
grinding
Machining operation in which material is removed from the workpiece by a powered abrasive wheel, stone, belt, paste, sheet, compound, slurry, etc. Takes various forms: surface grinding (creates flat and/or squared surfaces); cylindrical grinding (for external cylindrical and tapered shapes, fillets, undercuts, etc.); centerless grinding; chamfering; thread and form grinding; tool and cutter grinding; offhand grinding; lapping and polishing (grinding with extremely fine grits to create ultrasmooth surfaces); honing; and disc grinding.
- grinding machine
grinding machine
Powers a grinding wheel or other abrasive tool for the purpose of removing metal and finishing workpieces to close tolerances. Provides smooth, square, parallel and accurate workpiece surfaces. When ultrasmooth surfaces and finishes on the order of microns are required, lapping and honing machines (precision grinders that run abrasives with extremely fine, uniform grits) are used. In its “finishing” role, the grinder is perhaps the most widely used machine tool. Various styles are available: bench and pedestal grinders for sharpening lathe bits and drills; surface grinders for producing square, parallel, smooth and accurate parts; cylindrical and centerless grinders; center-hole grinders; form grinders; facemill and endmill grinders; gear-cutting grinders; jig grinders; abrasive belt (backstand, swing-frame, belt-roll) grinders; tool and cutter grinders for sharpening and resharpening cutting tools; carbide grinders; hand-held die grinders; and abrasive cutoff saws.
- statistical process control ( SPC)
statistical process control ( SPC)
Statistical techniques to measure and analyze the extent to which a process deviates from a set standard.