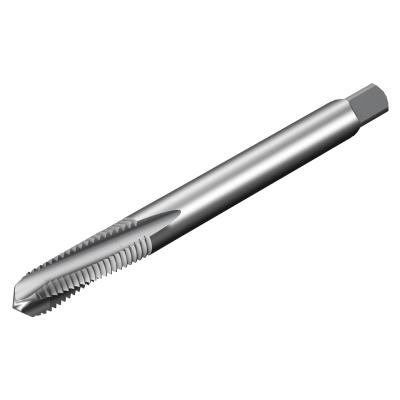
In response to strong demand for reliable machining solutions in the aerospace industry, Sandvik Coromant has launched new tapping and thread milling tools for ISO S materials (titanium and nickel-based alloys). The products have been specifically designed to enhance process security on high-value components, such as engine casings, thus providing reductions in scrap rates and machine downtime.
Developed to offer consistent and repeatable results, optimized geometry on the new taps for titanium includes a small positive rake angle for challenging materials and an innovative, wear resistant ACN (aluminium chromium nitride) coating that helps prevent weld formations. To avoid chip jamming in challenging material, the taps also have a high flank clearance for reduced friction. For truly stable tapping, the tools for nickel-based alloys feature a reduced helix of 10°.
The thread mills are produced with MJ thread forms with a 27° helix, the optimum angle for threading exotic materials. MJ thread forms are prevalent in the aerospace industry as they help reduce stress in the thread root of components.
“When tapping nickel alloys, the most important factor is creating the correct hole size for thread size required,” explains Steve Shotbolt, global product manager, threading at Sandvik Coromant. “Decreasing thread engagement reduces the torque necessary to drive the tap and helps eliminate any potential for tap breakage. Conventional thread engagement values of 75% have been found to be unnecessary with high-strength materials; usually engagements of 50-60% are sufficient for most requirements.”
The tapping of titanium alloys such as Ti6Al4V is more challenging than most alloyed materials. For example, titanium is not a good conductor of heat, which means temperatures tend to elevate on the faces and edges of cutting tools instead of dissipating through the part and machine structure. This retained heat can result in chipped edges and reduced tap life. In addition, titanium’s fairly low modulus of elasticity and high tensile strength gives it "springiness," producing the effect of "closing in" on the tap, a factor that can cause thread galling and tearing. It also increases torque on the tap and shortens its life.
The new taps from Sandvik Coromant are designed to counter these issues, helping to boost the manufacture of many aerospace engine components, including casings, shafts and discs, in fact any engine part made from ISO S materials that features bosses and/or flanges. The tools will also prove ideal for other sectors where titanium and nickel-based alloys are commonplace, such the oil and gas, pump and valve, and medical industries.
Introduced is the CoroTap 200 SM for tapping through holes in titanium, as well as the CoroTap 300 SM (blind holes, titanium) and CoroTap 300 SD (blind holes, nickel-based alloys). For thread milling, Sandvik Coromant is releasing the R217 for MJ thread forms.
In a customer performance test, the CoroTap 300 SM was able to more than double the number of tapped holes produced on an Inconel 718 workpiece, from eight holes (using a competitor tap) to 17 holes. Using a DMG DMU 60 CNC machining center with eight percent external coolant, the cutting data was identical for both tools: 251 rpm spindle speed; 6 m/min (19.685 ft/min) cutting speed; and 0.907 mm/min (28 TPI) feed rate.
Contact Details
Related Glossary Terms
- alloys
alloys
Substances having metallic properties and being composed of two or more chemical elements of which at least one is a metal.
- clearance
clearance
Space provided behind a tool’s land or relief to prevent rubbing and subsequent premature deterioration of the tool. See land; relief.
- computer numerical control ( CNC)
computer numerical control ( CNC)
Microprocessor-based controller dedicated to a machine tool that permits the creation or modification of parts. Programmed numerical control activates the machine’s servos and spindle drives and controls the various machining operations. See DNC, direct numerical control; NC, numerical control.
- coolant
coolant
Fluid that reduces temperature buildup at the tool/workpiece interface during machining. Normally takes the form of a liquid such as soluble or chemical mixtures (semisynthetic, synthetic) but can be pressurized air or other gas. Because of water’s ability to absorb great quantities of heat, it is widely used as a coolant and vehicle for various cutting compounds, with the water-to-compound ratio varying with the machining task. See cutting fluid; semisynthetic cutting fluid; soluble-oil cutting fluid; synthetic cutting fluid.
- feed
feed
Rate of change of position of the tool as a whole, relative to the workpiece while cutting.
- galling
galling
Condition whereby excessive friction between high spots results in localized welding with subsequent spalling and further roughening of the rubbing surface(s) of one or both of two mating parts.
- gang cutting ( milling)
gang cutting ( milling)
Machining with several cutters mounted on a single arbor, generally for simultaneous cutting.
- machining center
machining center
CNC machine tool capable of drilling, reaming, tapping, milling and boring. Normally comes with an automatic toolchanger. See automatic toolchanger.
- milling
milling
Machining operation in which metal or other material is removed by applying power to a rotating cutter. In vertical milling, the cutting tool is mounted vertically on the spindle. In horizontal milling, the cutting tool is mounted horizontally, either directly on the spindle or on an arbor. Horizontal milling is further broken down into conventional milling, where the cutter rotates opposite the direction of feed, or “up” into the workpiece; and climb milling, where the cutter rotates in the direction of feed, or “down” into the workpiece. Milling operations include plane or surface milling, endmilling, facemilling, angle milling, form milling and profiling.
- modulus of elasticity
modulus of elasticity
Measure of rigidity or stiffness of a metal, defined as a ratio of stress, below the proportional limit, to the corresponding strain. Also known as Young’s modulus.
- rake
rake
Angle of inclination between the face of the cutting tool and the workpiece. If the face of the tool lies in a plane through the axis of the workpiece, the tool is said to have a neutral, or zero, rake. If the inclination of the tool face makes the cutting edge more acute than when the rake angle is zero, the rake is positive. If the inclination of the tool face makes the cutting edge less acute or more blunt than when the rake angle is zero, the rake is negative.
- tap
tap
Cylindrical tool that cuts internal threads and has flutes to remove chips and carry tapping fluid to the point of cut. Normally used on a drill press or tapping machine but also may be operated manually. See tapping.
- tapping
tapping
Machining operation in which a tap, with teeth on its periphery, cuts internal threads in a predrilled hole having a smaller diameter than the tap diameter. Threads are formed by a combined rotary and axial-relative motion between tap and workpiece. See tap.
- tensile strength
tensile strength
In tensile testing, the ratio of maximum load to original cross-sectional area. Also called ultimate strength. Compare with yield strength.
- threading
threading
Process of both external (e.g., thread milling) and internal (e.g., tapping, thread milling) cutting, turning and rolling of threads into particular material. Standardized specifications are available to determine the desired results of the threading process. Numerous thread-series designations are written for specific applications. Threading often is performed on a lathe. Specifications such as thread height are critical in determining the strength of the threads. The material used is taken into consideration in determining the expected results of any particular application for that threaded piece. In external threading, a calculated depth is required as well as a particular angle to the cut. To perform internal threading, the exact diameter to bore the hole is critical before threading. The threads are distinguished from one another by the amount of tolerance and/or allowance that is specified. See turning.