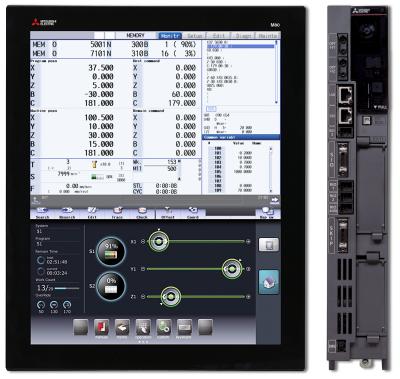
Mitsubishi Electric Automation introduces the M80W computer numerical controller, the latest in its M8 series CNCs. The M80W features a touch screen Windows-based display that is separate from the control unit, providing expandability and flexibility. Incorporating the latest operating system and slim personal computer, the M80W includes two expansion slots for 32GB SD cards, allowing OEMs and end users to add up to 64GB more memory for even greater flexibility.
The new M80W CNC was designed for the automotive and machine tool industries, and is especially useful for applications such as turning centers, machining centers, lathes and mills.
Key benefits of the M80W include:
- CNC-dedicated CPU for improved cycles times, faster program processing and more accurate machining
- Intuitive, touch-screen operation for optimal visibility
- Improved super smooth surface (SSS) control, reducing machine vibration during high-speed cutting
- High-speed, high-accuracy mode comes standard, allowing for complex, highly precise 3-D mold work
- User-level data protection allowing for multiple levels of permissions based on operator’s role
- Field network compatibility with CC-Link, PROFIBUS DP, and Ethernet/IP for easy connectivity to peripheral equipment and devices
The M80W CNC includes a 19" vertical display with a split multiple window that can be customized by arranging a keyboard, operation panel, document viewer or other applications. In addition, real-time servo and spindle tuning helps maintain machine stability by adjusting the control gains automatically.
“We designed the M80W from the ground up, creating a revolutionary leap in CNC performance,” said Scott Strache, product manager at Mitsubishi Electric Automation Inc. “This new standalone CNC is a breakthrough in the control of high-speed, high-precision machining, while offering high productivity and easy operability.”
Contact Details
Related Glossary Terms
- 3-D
3-D
Way of displaying real-world objects in a natural way by showing depth, height and width. This system uses the X, Y and Z axes.
- centers
centers
Cone-shaped pins that support a workpiece by one or two ends during machining. The centers fit into holes drilled in the workpiece ends. Centers that turn with the workpiece are called “live” centers; those that do not are called “dead” centers.
- computer numerical control ( CNC)
computer numerical control ( CNC)
Microprocessor-based controller dedicated to a machine tool that permits the creation or modification of parts. Programmed numerical control activates the machine’s servos and spindle drives and controls the various machining operations. See DNC, direct numerical control; NC, numerical control.
- turning
turning
Workpiece is held in a chuck, mounted on a face plate or secured between centers and rotated while a cutting tool, normally a single-point tool, is fed into it along its periphery or across its end or face. Takes the form of straight turning (cutting along the periphery of the workpiece); taper turning (creating a taper); step turning (turning different-size diameters on the same work); chamfering (beveling an edge or shoulder); facing (cutting on an end); turning threads (usually external but can be internal); roughing (high-volume metal removal); and finishing (final light cuts). Performed on lathes, turning centers, chucking machines, automatic screw machines and similar machines.