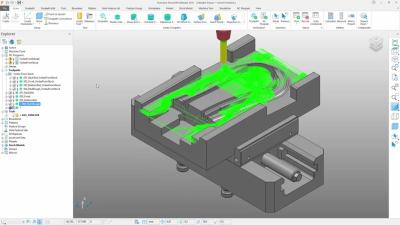
PowerMill is Autodesk’s CAM software for high-speed and 5-axis machining. It offers a comprehensive range of strategies and powerful editing tools to ensure efficient, safe and accurate machining, especially for companies that are using sophisticated CNC machine tools to produce complex shapes in challenging materials. PowerMill is used in a range of industries but is particularly successful in mold, tool and die, complex aerospace and automotive applications.
The release of PowerMill 2019 focuses on three key areas of development:
- Enhancing existing functionality for high-efficiency machining;
- Adding technology from the wider family of Autodesk software that can benefit PowerMill users;
- Developing completely new technology to allow PowerMill to support new processes.
To meet the growing trend for CNC machine tools that offer both additive and subtractive capabilities, PowerMill 2019 provides a dedicated suite of additive strategies and simulation tools. These are specifically designed to solve the unique challenges of programming these hybrid machines. PowerMill can generate safe and efficient toolpaths to drive directed energy deposition (DED) processes that utilize wire-fed or powder-blown hardware.
These are not simply subtractive toolpaths in reverse, instead PowerMill offers highly specialized 3- and 5-axis programs that can be used to reliably build entire components from scratch. Alternatively, localized features or surface coatings can be applied to existing parts, allowing components to be enhanced or repaired. Of course, being PowerMill, manufacturers have instant access to a vast library of subtractive manufacturing strategies meaning critical features can be CNC machined where needed.
For five-axis programming, PowerMill’s collision avoidance tools have been further improved. A new “automatic tool-axis tilting” method for collision avoidance simplifies hugely the programming of 5-axis machines. The new option provides a single solution that helps generate smooth and safe five-axis motion for all model shapes and toolpath types, making it as easy to create five-axis programs as it is 3-axis code.
PowerMill’s high-efficiency roughing strategy – or Vortex – was one of the first high efficiency roughing algorithms to hit the world of CNC machining. The 2019 release sees the inclusion of a new “From Stock” option that is based on the “Adaptive Clearing” technology provided in other Autodesk CAM software products.
This new option creates toolpaths with offsets that are based on both the shape of the part being produced and the stock being milled. The result is toolpaths that are considerably more efficient, with shorter machining cycle times and fewer tool retractions. In recent tests, carried out in Autodesk’s Advanced Manufacturing Facility (AMF) in Birmingham, UK, a test mold was machined in P20 tool steel. The previous “From Model” option took 48 minutes 28 seconds to complete. The “From Stock” option used the same tooling, feeds and speeds and yet produced this same part in 32 minutes 33 seconds, a saving of 33 percent.
For 2D machining, PowerMill provides an improved workflow for the definition of open-sided pockets and bosses. These new, open, features are recognized by PowerMill’s existing 2D toolpaths meaning tool entry and exit points are automatically positioned in sensible locations to avoid overloading cutting tools. In addition, PowerMill 2019 allows 2D features to be created based on a selection of surfaces – reducing the time and effort needed to generate NC code.
PowerMill’s stock simulation tool – ViewMill – has been enhanced to include a new “Remaining Material” shading mode. This helps CAM programmers to identify areas of un-machined stock quickly, to ensure parts are fully machined before being removed from the machine. The shading mode automatically identifies the maximum amount of stock left on a simulated part and provides dynamic slider bars to allow programmers to visualize the distribution of stock. This improvement aims to give manufacturers increased confidence that the parts are cut correctly and fully prior to being removed from the CNC machine table
PowerMill 2019 includes a new entity called “Setups,” which allows programmers to better manage the synchronization between toolpaths and NC Programs. This first version of setups also provides tools to help manufacture parts that use multiple fixture offsets.
To improve collaboration between the programming office and the shop floor, PowerMill 2019 includes a direct interface to Autodesk Fusion Production, a cloud-based collaboration tool specializing in scheduling and tracking production, and monitoring CNC machine utilisation. PowerMill data, including NC code, setup sheets and work instructions, can be shared with key project stakeholders using internet-enabled devices such as mobile phones and tablets. Fusion Production helps manufacturers to get an instant overview of the performance of their facility, allowing them to identify problems and avoid bottlenecks sooner.
Like many Autodesk products, PowerMill now benefits from access to Autodesk Drive, a personal cloud storage site. Subscribers to PowerMill can save project data to a secure cloud and invite project members to collaborate and review the contents of their projects using any cloud-connected device. PowerMill models, tools, toolpaths and NC programs can be interrogated without the need for a PowerMill license.
Contact Details
Related Glossary Terms
- computer numerical control ( CNC)
computer numerical control ( CNC)
Microprocessor-based controller dedicated to a machine tool that permits the creation or modification of parts. Programmed numerical control activates the machine’s servos and spindle drives and controls the various machining operations. See DNC, direct numerical control; NC, numerical control.
- computer-aided manufacturing ( CAM)
computer-aided manufacturing ( CAM)
Use of computers to control machining and manufacturing processes.
- fixture
fixture
Device, often made in-house, that holds a specific workpiece. See jig; modular fixturing.
- numerical control ( NC)
numerical control ( NC)
Any controlled equipment that allows an operator to program its movement by entering a series of coded numbers and symbols. See CNC, computer numerical control; DNC, direct numerical control.
- toolpath( cutter path)
toolpath( cutter path)
2-D or 3-D path generated by program code or a CAM system and followed by tool when machining a part.