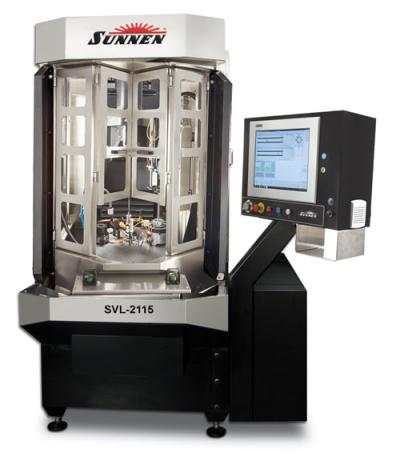
Sunnen's SVL-2115 automated lapping machine brings increased productivity and part consistency to what is traditionally a manual process. Based on the same proven SV-2115 honing system, the SVL-2115 provides single setup processing of hydraulic valves, sleeves, fuel system components and other parts that are prone to distortion when honed. The patented system control is designed for unattended operation and automatically laps and air gage bores throughout the cycle. Gage readings are fed back to the control and the cycle is repeated until the parts are within specifications.
“Automated lapping is more consistent than manual and there are fewer workers today with the skills necessary for precision manual lapping,” said Phil Hanna, Sunnen product manager. “For very expensive parts an automatic lapping process reduces the possibility of ruined parts due to human error. Since lapping is usually the last process during the machining of a workpiece, if the lapping is not correct all the work to get the part produced up to that point is wasted.”
The patented Sunnen lapping tools are available for workpiece diameters from 6.3 to 45 mm (0.25 to 1.77 in) and lengths up to 12 times the bore diameter, not to exceed 200 mm (7.87 in). Additional diameter ranges are in development. Spindle speed range is 100 to 2,000 rpm during lapping, but it is capable of slow speeds for non-powered steps, such as lapping paste application or slow-rotation bore entry. Stroking speed is 0 to 350 spm, with stroke length optimized to achieve a high degree of cylindricity.
“This system is a time-saver and it frees operators to run another machine, or handle other job floor duties,” added Hanna. “Operators load the workpiece into the fixture and start the lapping cycle, the cycle ends when the part is in tolerance. With automated lapping, less-skilled operators can achieve consistent, close-tolerance results. The precision control valve market is growing, not only in aerospace, but other industries as well. We have numerous SVL-2115 machines now in operation around the US, proving the need for automated lapping.”
Due to the outstanding ergonomics of the machine, repetitive motion injuries often encountered with manual lapping have been virtually eliminated. There is no need to touch a moving part during the lapping process, and a light curtain is standard, so safety is greatly improved.
Easy tooling and probe changeovers accommodate multiple different parts runs during the course of a shift. A stack light allows operators to monitor cycle completions or faults from a distance.
Contact Details
Related Glossary Terms
- fixture
fixture
Device, often made in-house, that holds a specific workpiece. See jig; modular fixturing.
- lapping
lapping
Finishing operation in which a loose, fine-grain abrasive in a liquid medium abrades material. Extremely accurate process that corrects minor shape imperfections, refines surface finishes and produces a close fit between mating surfaces.
- tolerance
tolerance
Minimum and maximum amount a workpiece dimension is allowed to vary from a set standard and still be acceptable.