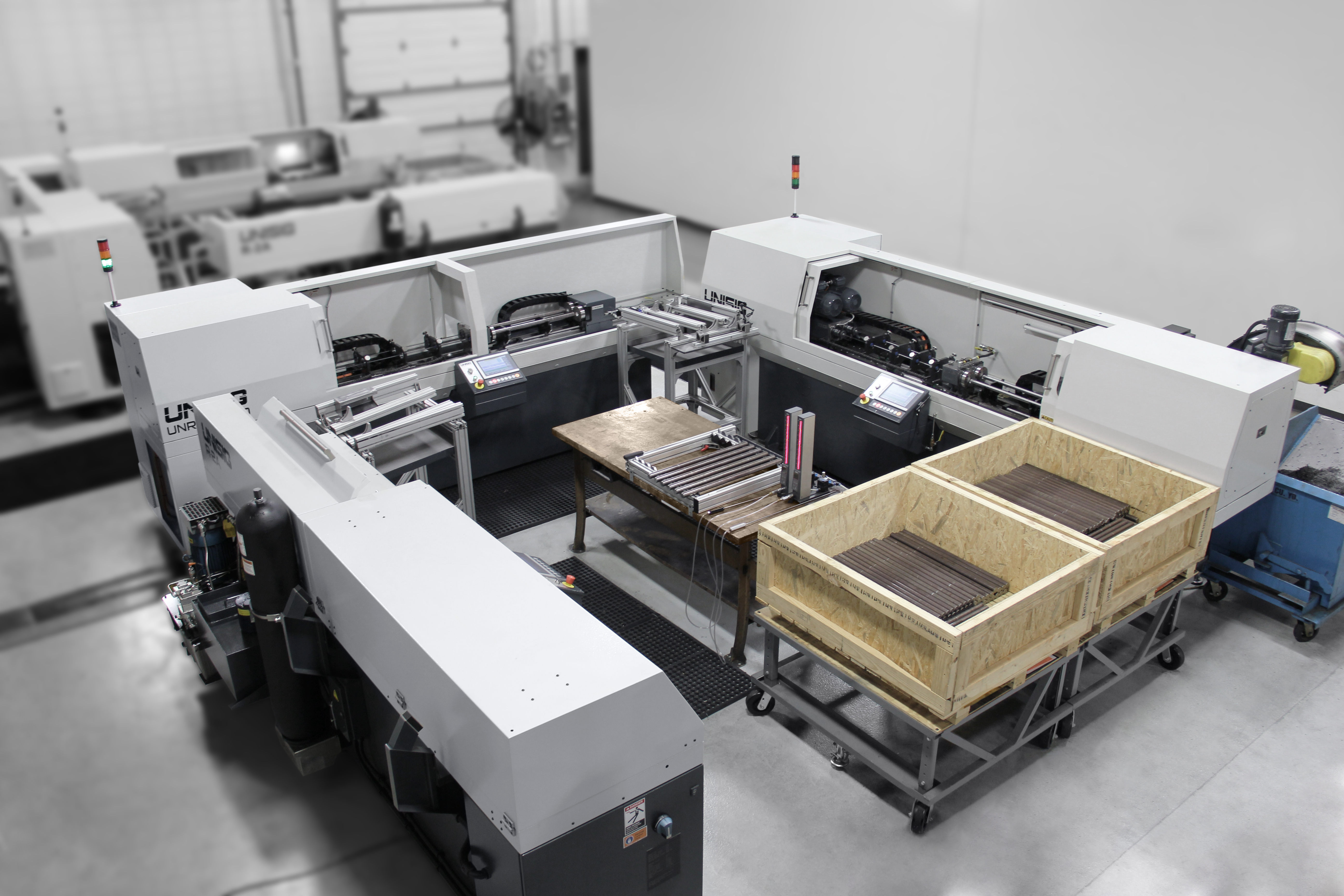
MENOMONEE FALLS, Wis., January 2, 2019 – Entrust Manufacturing Technologies, Inc. has announced the launch of Vortakt, a new component manufacturing division specializing in OEM partnerships for gundrilling applications. Vortakt leverages the deep-hole drilling expertise and equipment produced by the UNISIG division of Entrust to provide world-class solutions for high-volume production.
With an initial focus in the firearm industry, Vortakt offers its services to barrel manufacturers that need a partner to help elevate the quality of their products and provide reliable service using state of the art technology. Vortakt handles mass production runs that other services find difficult to manage. Vortakt’s calculated approach to production gundrilling uses a tried-and-true set of processes – as well as industry-leading manufacturing technology from UNISIG – to offer exceptionally precise gundrilling and the additional steps necessary to produce rifle barrels.
Chad Weister leads the new division, with an emphasis on growing its presence in the industry through continued investment by Entrust. An engineer with nearly 15 years of experience in the deep hole drilling industry, Weister oversees a team of expert technicians running multiple production cells. “We’re machinists and engineers, not gunsmiths,” said Weister. “Our precise processes and extensive data, as well as decades of collective gundrilling, reaming, rifling and manufacturing experience, means that we don’t just make great barrels – we do so consistently.”
In addition to providing contract production to its firearm customers, Vortakt also assists OEMs in all industries with application assistance and design expertise. Although Vortakt frequently produce components from customer-supplied dimensions or to internationally recognized standards, Vortakt also works directly with customers to help them develop ideal solutions to manufacturing needs.
Related Glossary Terms
- gundrilling
gundrilling
Drilling process using a self-guiding tool to produce deep, precise holes. High-pressure coolant is fed to the cutting area, usually through the gundrill’s shank.