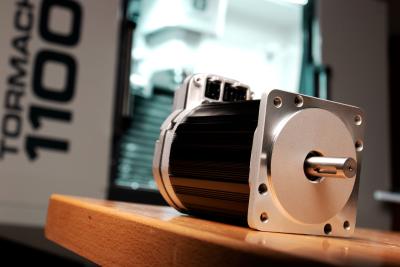
Tormach Inc. has announced it is now offering servomotors for its line of 1100M and 770M CNC milling machines. Servo upgrade kits are now available for current users of these machines, which allows them to transform their current ‘M’ series machines to ‘M+’.
Users who upgrade to servo motors will enjoy numerous benefits, including:
-Faster speeds – more than double feed rates
-Higher acceleration – allows machine to get up to speed much quicker
-Reduced noise
-Closing of the feedback loop into the control system
-Time and money savings on every part made
“For the vast majority of machinists using our 1100M and 770M mills, upgrading to the servo motors is an easy decision,” said Lori Morrison Bufalo, marketing director at Tormach. “We’ve made it easy and affordable for users to perform this upgrade and start getting even better performance out of their Tormach mills.”
The cost to upgrade to the servomotor package is $1,995.00. Additional recommended items including an automatic oiler kit are available for an additional fee.
Later this year Tormach plans to offer a BT30 spindle upgrade package to users as well. This upgrade will allow users to take their ‘M+’ mills to the ‘MX’ level, meaning they will have the servomotors along with BT30 spindles, encoders and power drawbars.
Contact Details
Related Glossary Terms
- computer numerical control ( CNC)
computer numerical control ( CNC)
Microprocessor-based controller dedicated to a machine tool that permits the creation or modification of parts. Programmed numerical control activates the machine’s servos and spindle drives and controls the various machining operations. See DNC, direct numerical control; NC, numerical control.
- feed
feed
Rate of change of position of the tool as a whole, relative to the workpiece while cutting.
- gang cutting ( milling)
gang cutting ( milling)
Machining with several cutters mounted on a single arbor, generally for simultaneous cutting.
- milling
milling
Machining operation in which metal or other material is removed by applying power to a rotating cutter. In vertical milling, the cutting tool is mounted vertically on the spindle. In horizontal milling, the cutting tool is mounted horizontally, either directly on the spindle or on an arbor. Horizontal milling is further broken down into conventional milling, where the cutter rotates opposite the direction of feed, or “up” into the workpiece; and climb milling, where the cutter rotates in the direction of feed, or “down” into the workpiece. Milling operations include plane or surface milling, endmilling, facemilling, angle milling, form milling and profiling.