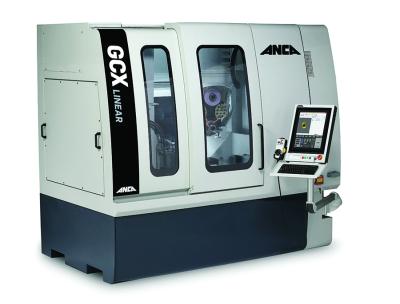
The new GCX Linear builds on the best aspects of ANCAs proven technology to offer a purpose-built solution for manufacturing and sharpening skiving cutters. With a five axis CNC grinder powered by LinX linear motor technology on X, Y and Z axes, the GCX Linear also comes with features specially designed for skiving cutters and shaper cutters.
Xiaoyu Wang, product manager at ANCA said: “ANCA is responding to the increasing popularity of skiving and resulting surge in demand for skiving cutters. We want our customers to have a complete solution for manufacturing and sharpening skiving cutters and the GCX Linear will set the new benchmark for skiving cutter grinding.
“Dressing the complex wheel profile is critical, ANCA developed the latest acoustic emission monitoring system (AEMS). AEMS can be taught to pick up the right sound of perfect dressing even in a noisy production environment. Built upon supervised machine learning algorithm, AEMS ensures the wheel profile is dressed within micron accuracy with the least possible time while minimizing the reduction in size.”
Tailored features of ANCA’s new GCX Linear:
- Motor temperature control (patent pending), minimizes machine warmup time and delivers optimal thermal stability during grinding.
- Full process virtualisation on design station before grinding: design, optimize, 3D simulation, MRR estimation and more.
- In-process dressing with acoustic emission monitoring system and supervised machine learning algorithm.
- Dedicated gear cutting tool software package.
- Five-axis CNC grinder, with LinX linear motor technology on X, Y and Z axes.
- 37kW (49HP) peak power direct drive spindle with BigPlus arbor.
- High-accuracy headstock offers greatly improved index positional accuracy.
Motion Temperature Control (MTC) is a patent pending innovation built into the motor spindle drive firmware. Smart control algorithm actively manages and maintains the temperature of motorised spindles in the GCX Linear. Benefits delivered by this feature include:
- Dramatically reduced machine warmup time, meaning you can start grinding tools sooner, knowing the machine has reached thermal stability. This improves productivity and machine utilization.
- Consistent thermal stability of the spindle over time regardless of changes in spindle load or speed or spindle cooling coolant temperature. This greatly improves dimensional stability of grinding results.
The LinX linear motor technology for axis motion (X, Y and Z axes), in conjunction with linear scales, enhances precision and performance. Specially designed for a lifetime of operation in harsh grinding environments, the LinX motors have a cylindrical magnetic field, which means there is no additional down force on the rails or machine base.
With no temperature variations (meaning no need for a separate chiller unit), and being sealed to IP67, there is minimal wear and tear so that the machine accuracy remains over the lifetime of the machine. The LinX linear motor has a high axis speed and acceleration, leading to reduced cycle times while maintaining a smooth axis motion.
Contact Details
Related Glossary Terms
- arbor
arbor
Shaft used for rotary support in machining applications. In grinding, the spindle for mounting the wheel; in milling and other cutting operations, the shaft for mounting the cutter.
- computer numerical control ( CNC)
computer numerical control ( CNC)
Microprocessor-based controller dedicated to a machine tool that permits the creation or modification of parts. Programmed numerical control activates the machine’s servos and spindle drives and controls the various machining operations. See DNC, direct numerical control; NC, numerical control.
- coolant
coolant
Fluid that reduces temperature buildup at the tool/workpiece interface during machining. Normally takes the form of a liquid such as soluble or chemical mixtures (semisynthetic, synthetic) but can be pressurized air or other gas. Because of water’s ability to absorb great quantities of heat, it is widely used as a coolant and vehicle for various cutting compounds, with the water-to-compound ratio varying with the machining task. See cutting fluid; semisynthetic cutting fluid; soluble-oil cutting fluid; synthetic cutting fluid.
- dressing
dressing
Removal of undesirable materials from “loaded” grinding wheels using a single- or multi-point diamond or other tool. The process also exposes unused, sharp abrasive points. See loading; truing.
- grinding
grinding
Machining operation in which material is removed from the workpiece by a powered abrasive wheel, stone, belt, paste, sheet, compound, slurry, etc. Takes various forms: surface grinding (creates flat and/or squared surfaces); cylindrical grinding (for external cylindrical and tapered shapes, fillets, undercuts, etc.); centerless grinding; chamfering; thread and form grinding; tool and cutter grinding; offhand grinding; lapping and polishing (grinding with extremely fine grits to create ultrasmooth surfaces); honing; and disc grinding.
- linear motor
linear motor
Functionally the same as a rotary motor in a machine tool, a linear motor can be thought of as a standard permanent-magnet, rotary-style motor slit axially to the center and then peeled back and laid flat. The major advantage of using a linear motor to drive the axis motion is that it eliminates the inefficiency and mechanical variance caused by the ballscrew assembly system used in most CNC machines.
- micron
micron
Measure of length that is equal to one-millionth of a meter.
- slotting machine ( shaper)
slotting machine ( shaper)
Vertical or horizontal machine that accommodates single-point, reciprocating cutting tools to shape or slot a workpiece. Normally used for special (unusual/intricate shapes), low-volume runs typically performed by broaching or milling machines. See broaching machine; mill, milling machine.