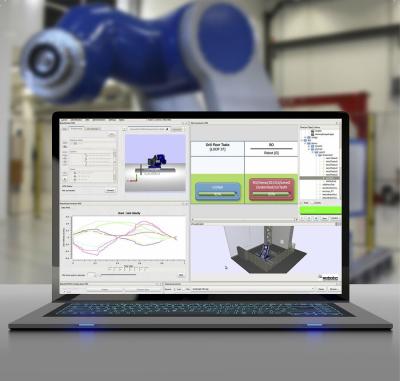
Energid released Version 5.5 of the Actin software development kit (SDK), an even more powerful and easier-to-use version of the industry’s only real-time adaptive robotic motion control and path planning toolkit. Actin Version 5.5 adds Actin Viewer enhancements, Motion Script updates and G-code support, making it even easier for robotic systems developers to focus on the robot’s tasks rather than joint movement and paths. These features help further decrease the developer’s time to proof-of-concept (POC) and time to market, while also remaining a less expensive and time-tested option to in-house development and open source solutions.
“Actin can save months or years of development time and money over in-house programming and open source tools, and now we’ve added new features that make Actin even easier to use,” said Doug Barker, Energid's COO. “Actin 5.5 expands the SDK's core motion control and path planning libraries and adds efficiency improvements to core motion planning algorithms. This release will make it possible for customers to more easily address robotics process applications like dispensing and deburring using toolpaths generated from G-code. We've also made it easier for developers to create robot tasks through our Motion Script interface.”
Traditionally, developers of robotic systems would have to program many intermediate waypoints to avoid collisions with the environment and would have to hand tune paths to avoid collisions, singularities and joint limits for process-related tasks. Actin automatically finds optimal paths in real time, responding to sensory input and then directing robots on the most efficient path while avoiding collisions. The robot motion is updated dynamically without requiring reprogramming, even in dynamic, mission-critical environments.
Actin 5.5 adds to the software’s powerful capabilities with:
- Edit Motion Scripts in Actin Viewer: Actin 5.5 provides a simple IDE to create Motion Scripts. Developers can also use the motion script GUI plugin to more easily create motion scripts to task an Actin model. The interface now has file save, save as, and open options, as well as syntax highlighting, improved icons and layout, a toolbar quick-access button, as well as context menu options to insert motion scripts from the current state of the model.
- Updates to Motion Script: Developers can now write custom functions in Motion Script, with a list of Motion Script variables able to be passed to the function by value or reference. This brought about a new capability: developers can now create a Motion Script composed of multiple files. build more modular programs to create a Motion Script composed of multiple files. This lets developers compose more complex scripts, reuse scripts in more advanced applications, and quickly iterate when setting up new applications with Actin.
- G-code support: Actin 5.5 supports toolpaths defined in G-code, an industry standard widely adopted by manufacturers that are familiar with CNC machining. A toolpath defines the tool orientation, trajectory, speed (or feed rate) and travel direction. The toolpath files can be generated in third-party CAD/CAM software packages based on part models. Actin will convert imported toolpath files into robot motion automatically.
Contact Details
Related Glossary Terms
- computer numerical control ( CNC)
computer numerical control ( CNC)
Microprocessor-based controller dedicated to a machine tool that permits the creation or modification of parts. Programmed numerical control activates the machine’s servos and spindle drives and controls the various machining operations. See DNC, direct numerical control; NC, numerical control.
- feed
feed
Rate of change of position of the tool as a whole, relative to the workpiece while cutting.
- robotics
robotics
Discipline involving self-actuating and self-operating devices. Robots frequently imitate human capabilities, including the ability to manipulate physical objects while evaluating and reacting appropriately to various stimuli. See industrial robot; robot.
- toolpath( cutter path)
toolpath( cutter path)
2-D or 3-D path generated by program code or a CAM system and followed by tool when machining a part.