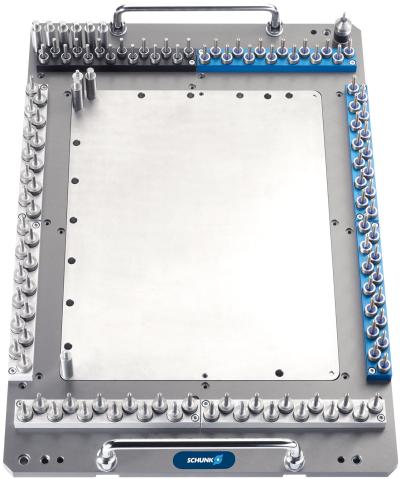
SCHUNK Electronic Solutions has developed Magnoplate – a universal workpiece holder for depaneling machines that places magnetic carrier pins with a milling head on a support plate. This results in lightning fast brackets for new assembly groups.
The advantage for users: You start new jobs faster without having to wait for the time-consuming production of suitable workpiece carriers. Electronic Manufacturing Services (EMS) service providers with a great product variance especially benefit from this automation. They are confronted with the challenge of processing thousands of assembly groups (panels) for the manufacturers of mobile phones, printers, and computers every month.
"The trend in the era of individualized products is towards ever smaller batch sizes. This increases the pressure on companies," explains Jochen Ehmer, managing director of SCHUNK Electronic Solutions. "With Magnoplate, even the smallest series can be machined quickly and economically."
Zollner Elektronik AG from Zandt in Bavaria, which has established itself as a mechatronics service provider among the top 15 EMS service providers worldwide, is one of the users of the system, which is unique on the market to date.
Magnoplate consists of a support plate, magnetic carrier pins and CAD software. When a new order is placed, an employee loads the CAD data of the assembly into the software of the depaneling machine, and then virtually determines the position of the carrier pins. Now the milling head comes into play, in which a setting sleeve is clamped, not a milling cutter. With this setting sleeve, the milling head grips the magnetic pins, which are stored in magazines along the edge of the carrier plate and positions them on the base plate. In this way, the suitable workpiece holder is created step by step within two minutes and the depaneling can begin.
"The production of a classic tool carrier, on the other hand, often takes several weeks and reduces the company's ability to react," Ehmer said. With Magnoplate, however, users are not just more responsive. "You also save the purchasing, storage, and maintenance costs for classic workpiece holders. The investment pays for itself accordingly." The system is compatible with all depaneling machines from SCHUNK Electronic Solutions. Customized pin geometries are also available.
A further component of Magnoplate is a patented fixing plate with holes, which is placed on top of the carrier pins - it can be produced using the CAD software and the milling head of the depaneling machine. The fixing plate ensures that the carrier pins do not move during depaneling. This ensures that small sensitive assembly groups are not damaged during the milling process. The fixing plate also ensure a faster workflow. The corresponding CNC program can be automatically loaded via a printed QR code that the machine reads. Given its thickness of just 1.5 mm, the fixing plate can be stored in drawers to save space.
Contact Details
Related Glossary Terms
- computer numerical control ( CNC)
computer numerical control ( CNC)
Microprocessor-based controller dedicated to a machine tool that permits the creation or modification of parts. Programmed numerical control activates the machine’s servos and spindle drives and controls the various machining operations. See DNC, direct numerical control; NC, numerical control.
- computer-aided design ( CAD)
computer-aided design ( CAD)
Product-design functions performed with the help of computers and special software.
- gang cutting ( milling)
gang cutting ( milling)
Machining with several cutters mounted on a single arbor, generally for simultaneous cutting.
- milling
milling
Machining operation in which metal or other material is removed by applying power to a rotating cutter. In vertical milling, the cutting tool is mounted vertically on the spindle. In horizontal milling, the cutting tool is mounted horizontally, either directly on the spindle or on an arbor. Horizontal milling is further broken down into conventional milling, where the cutter rotates opposite the direction of feed, or “up” into the workpiece; and climb milling, where the cutter rotates in the direction of feed, or “down” into the workpiece. Milling operations include plane or surface milling, endmilling, facemilling, angle milling, form milling and profiling.
- milling cutter
milling cutter
Loosely, any milling tool. Horizontal cutters take the form of plain milling cutters, plain spiral-tooth cutters, helical cutters, side-milling cutters, staggered-tooth side-milling cutters, facemilling cutters, angular cutters, double-angle cutters, convex and concave form-milling cutters, straddle-sprocket cutters, spur-gear cutters, corner-rounding cutters and slitting saws. Vertical cutters use shank-mounted cutting tools, including endmills, T-slot cutters, Woodruff keyseat cutters and dovetail cutters; these may also be used on horizontal mills. See milling.