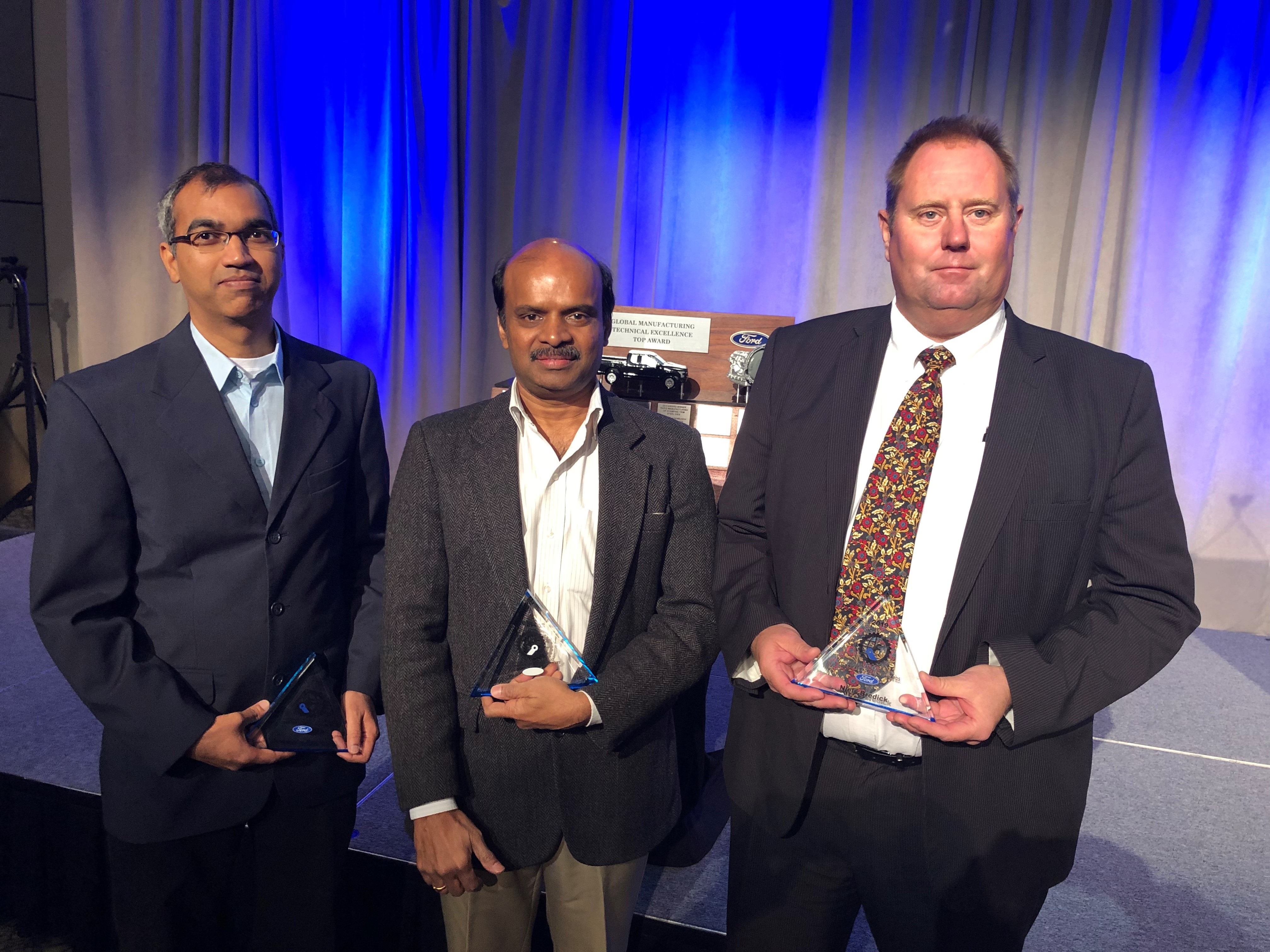
Sandvik Coromant wins the Technical Excellence Award from Ford Motor Co. for tool and process monitoring application of a gear grinding operation. The award was presented at a ceremony in Michigan on Nov. 7, 2019.
Accepting the award for Sandvik Coromant, Niels Bredick, senior solutions specialist, played an integral role in the success of the tool and process monitoring application. Using CoroPlus Tool Guard and Collision Detector, a Ford Motor plant was able to successfully monitor a gear grinding process in real time using a force sensor integrated between the spindle and the interface of the revolver.
The process monitoring application uses vibration to detect a tool force overload. If the signal being sent from a sensor on the machine spindle exceeds the predetermined monitoring overload limit, the machining force strikes out and alerts the operator and shuts down the machine, saving valuable parts from being scrapped. Both solutions are installed inside a machine tool and are connected to a programmable logic controller so that with any detection of a collision or degeneration, the machine reacts within five milliseconds.
Bredick said, “It is very satisfying to know that we implemented the correct technology for this process and provided a reliable solution to successfully monitor this critical operation. This process monitoring software can be applied to any operation with moving parts to avoid unwanted deviances from expected results.”
Jeff Rizzie, vice president of digital machining at Sandvik Coromant, concurred, “Without a process monitoring solution, like CoroPlus Tool Guard and CoroPlus Collision Detector, reaction time and expensive parts may be compromised if something goes wrong. Supporting sustainability and lean initiatives, this in-cut process monitoring technology provides stability and security enabling customers to be more productive and efficient.”
Contact Details
Related Glossary Terms
- grinding
grinding
Machining operation in which material is removed from the workpiece by a powered abrasive wheel, stone, belt, paste, sheet, compound, slurry, etc. Takes various forms: surface grinding (creates flat and/or squared surfaces); cylindrical grinding (for external cylindrical and tapered shapes, fillets, undercuts, etc.); centerless grinding; chamfering; thread and form grinding; tool and cutter grinding; offhand grinding; lapping and polishing (grinding with extremely fine grits to create ultrasmooth surfaces); honing; and disc grinding.