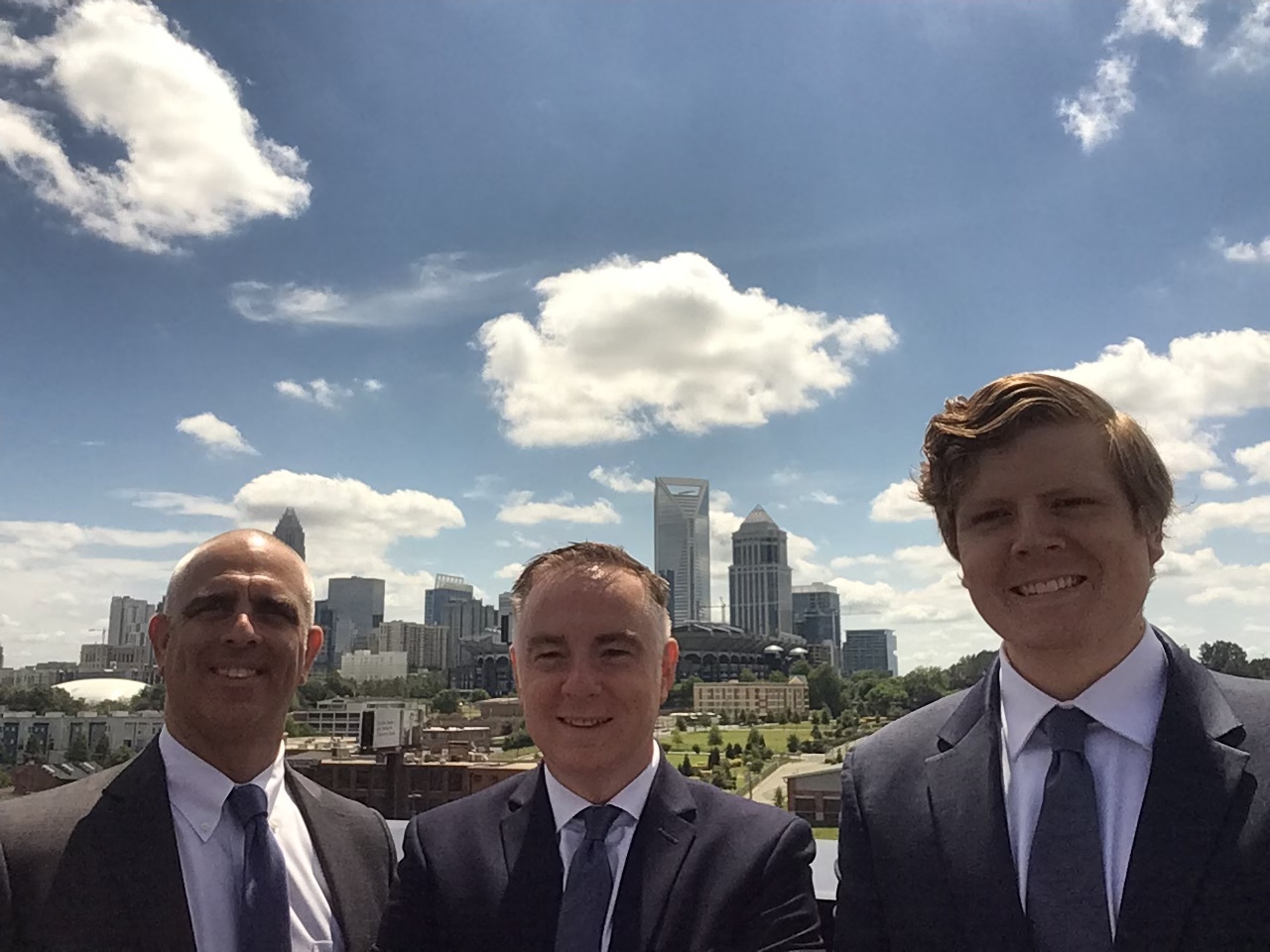
Beginning June 1, 2020, EMAG will be expanding its operation in the United States by opening an additional office, EMAG Charlotte, in Charlotte, NC. With this addition, current and prospective customers located in the southeastern portion of the United States will have the ability to meet face to face with sales, applications and service personnel. By providing local support, EMAG will strive to foster the growth that the industry is experiencing throughout the region. EMAG Charlotte will operate as a branch office of EMAG L.L.C., located in Farmington Hills, Michigan, the North American Headquarters for the EMAG Group.
With the growth of EMAG’s competitive Modular Standard machine portfolio, accessibility to new users has grown substantially; the Southeast is one of the fastest growing manufacturing hubs in the United States, driving EMAG’s strategic decision to open EMAG Charlotte.
The unique configuration of EMAG’s turning machine, allows for the automatic self-loading of workpieces. The inverted, traveling spindle architecture creates an ideal environment for cleanliness, optimum chip flow, and unsurpassed operator access. Coupled with the MINERALIT™ polymer concrete machine base, EMAG offers the best in class solution for tight tolerance production work. According to data from USMTO, EMAG has earned 87% market share for Inverted Vertical Lathes over the past five years in the United States, and the company is hoping that this move will continue to help them expand.
Contact Details
Related Glossary Terms
- numerical control ( NC)
numerical control ( NC)
Any controlled equipment that allows an operator to program its movement by entering a series of coded numbers and symbols. See CNC, computer numerical control; DNC, direct numerical control.
- tolerance
tolerance
Minimum and maximum amount a workpiece dimension is allowed to vary from a set standard and still be acceptable.
- turning
turning
Workpiece is held in a chuck, mounted on a face plate or secured between centers and rotated while a cutting tool, normally a single-point tool, is fed into it along its periphery or across its end or face. Takes the form of straight turning (cutting along the periphery of the workpiece); taper turning (creating a taper); step turning (turning different-size diameters on the same work); chamfering (beveling an edge or shoulder); facing (cutting on an end); turning threads (usually external but can be internal); roughing (high-volume metal removal); and finishing (final light cuts). Performed on lathes, turning centers, chucking machines, automatic screw machines and similar machines.
- turning machine
turning machine
Any machine that rotates a workpiece while feeding a cutting tool into it. See lathe.