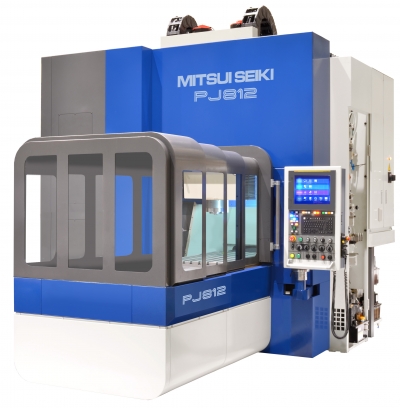
Mitsui Seiki has been instrumental in the advancement of critical parts manufacturing capability in North America for over 55 years. Today our product lines represent the finest in accuracy, contouring precision, and long-term reliability. To that end, the company has launched a new series of CNC vertical machining centers called the “J” series for “Jig”, which are ideal to machine medical, optical, mold & die, and aerospace parts.
The line provides positioning accuracy and repeatability of +/- 1µm. A thermal compensation system employs sensors on the machine faceplate and inside the spindle to minimize the effects of temperature changes on part accuracy and cut temperature-generated displacement by 60 percent. This system also reduces Z-axis thermal growth and deflection by 30 percent. Cooling systems for slide way lubrication and ball screw cores stabilize axis feed precision.
Mechanical design features that maximize machine rigidity and accuracy include hardened and ground tool steel box slideways as well as contact elements that enhance acceleration, reduce stick-slip, and allow for feed accuracy of 0.1 µm. Another proprietary engineering detail drastically improves the static rigidity of the Z-axis to more than six times that of conventional Z-axis arrangements.
These heavy duty, ultra precision machines allow for more complete machining of precision components including precision boring, milling, drilling and tapping. Machining center technology and jig borer precision in one machine.
The line incudes 4 basic machines to satisfy a broad range of workpieces:
PJ812 (PJ for “Profile Jig”) with travels X-1200mm, Y-800mm, Z-500mm. Max work size 1200mm x 800mm. Table load 1500kg. Spindles are offered from 10000RPM to 30000RPM. ATC 60, 90, 120 tools.
J1220 with travels X-2000mm, Y-1250mm, Z-500mm. Max work size 2200mm x 1500mm Table load 3000 (4000 opt)kg. Spindles are offered from 10000RPM to 15000RPM. ATC 60, 90, 120 tools.
J1230 with travels X-3000mm, Y-1250mm, Z-500mm. Max work size 3000mm x 1500mm Table load 3000 (4000 opt)kg. Spindles are offered from 10000RPM to 15000RPM. ATC 60, 90, 120 tools.
J1625 with travels X-2500mm, Y-1600mm, Z-500mm. Max work size 2700mm x 1700mm Table load 6500 kg. Spindles are offered from 10000RPM to 15000RPM. ATC 20, 60, 90, 120 tools.
All of the machines feature a full enclosure and various coolant system options.
Contact Details
Related Glossary Terms
- boring
boring
Enlarging a hole that already has been drilled or cored. Generally, it is an operation of truing the previously drilled hole with a single-point, lathe-type tool. Boring is essentially internal turning, in that usually a single-point cutting tool forms the internal shape. Some tools are available with two cutting edges to balance cutting forces.
- centers
centers
Cone-shaped pins that support a workpiece by one or two ends during machining. The centers fit into holes drilled in the workpiece ends. Centers that turn with the workpiece are called “live” centers; those that do not are called “dead” centers.
- computer numerical control ( CNC)
computer numerical control ( CNC)
Microprocessor-based controller dedicated to a machine tool that permits the creation or modification of parts. Programmed numerical control activates the machine’s servos and spindle drives and controls the various machining operations. See DNC, direct numerical control; NC, numerical control.
- coolant
coolant
Fluid that reduces temperature buildup at the tool/workpiece interface during machining. Normally takes the form of a liquid such as soluble or chemical mixtures (semisynthetic, synthetic) but can be pressurized air or other gas. Because of water’s ability to absorb great quantities of heat, it is widely used as a coolant and vehicle for various cutting compounds, with the water-to-compound ratio varying with the machining task. See cutting fluid; semisynthetic cutting fluid; soluble-oil cutting fluid; synthetic cutting fluid.
- feed
feed
Rate of change of position of the tool as a whole, relative to the workpiece while cutting.
- gang cutting ( milling)
gang cutting ( milling)
Machining with several cutters mounted on a single arbor, generally for simultaneous cutting.
- jig
jig
Tooling usually considered to be a stationary apparatus. A jig assists in the assembly or manufacture of a part or device. It holds the workpiece while guiding the cutting tool with a bushing. A jig used in subassembly or final assembly might provide assembly aids such as alignments and adjustments. See fixture.
- machining center
machining center
CNC machine tool capable of drilling, reaming, tapping, milling and boring. Normally comes with an automatic toolchanger. See automatic toolchanger.
- milling
milling
Machining operation in which metal or other material is removed by applying power to a rotating cutter. In vertical milling, the cutting tool is mounted vertically on the spindle. In horizontal milling, the cutting tool is mounted horizontally, either directly on the spindle or on an arbor. Horizontal milling is further broken down into conventional milling, where the cutter rotates opposite the direction of feed, or “up” into the workpiece; and climb milling, where the cutter rotates in the direction of feed, or “down” into the workpiece. Milling operations include plane or surface milling, endmilling, facemilling, angle milling, form milling and profiling.
- tapping
tapping
Machining operation in which a tap, with teeth on its periphery, cuts internal threads in a predrilled hole having a smaller diameter than the tap diameter. Threads are formed by a combined rotary and axial-relative motion between tap and workpiece. See tap.