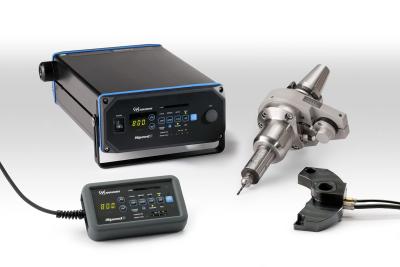
NSK America Corporation has introduced its new iSpeed5 System. The iSpeed5, a Fully Tool Changeable, Electric, High-Speed Motor/Spindle is an innovated tool that the manufacturing industry has been requesting for many years.
The iSpeed5 is a 60,000 or 80,000 RPM, 350 Watt, Brushless DC Electric System that eliminates the need for any operator intervention by using a special designed connection under that machine spindle that can prevent coolant, chips, dust and other machining debris from contaminating the stop block. No longer is there a need for operator intervention to connect or disconnect the High-Speed Motor/Spindle. With the iSpeed5, the availability for High-Speed and Micro Machining for both short or long periods of operation, as well as lights out manufacturing, are possible.
The iSpeed5 features ultra-precision ceramic bearings for high-speed performance, and spindle accuracy of less than 1 micron (.00004) T.I.R. for all micro milling, drilling and grinding applications. The dry air purge system proves ideal for graphite machining as well as surfacing for mold finishing. A wide variety of tapers are available.
The iSpeed5 control unit features a motor protection system as well as an input/output interface to communicate with the CNC controller. The Handy Controller allows hand-held operation of the system from a distance. This device features all of the same buttons and functions as the main controller, including speed adjustment, reverse and reset should the controller be mounted remotely. The iSpeed5 Stop Block integrates with the iSpeed5 controller in order to make automatic tool change possible. A variety of generic and custom stop blocks are available for all machine models.
Contact Details
Related Glossary Terms
- computer numerical control ( CNC)
computer numerical control ( CNC)
Microprocessor-based controller dedicated to a machine tool that permits the creation or modification of parts. Programmed numerical control activates the machine’s servos and spindle drives and controls the various machining operations. See DNC, direct numerical control; NC, numerical control.
- coolant
coolant
Fluid that reduces temperature buildup at the tool/workpiece interface during machining. Normally takes the form of a liquid such as soluble or chemical mixtures (semisynthetic, synthetic) but can be pressurized air or other gas. Because of water’s ability to absorb great quantities of heat, it is widely used as a coolant and vehicle for various cutting compounds, with the water-to-compound ratio varying with the machining task. See cutting fluid; semisynthetic cutting fluid; soluble-oil cutting fluid; synthetic cutting fluid.
- gang cutting ( milling)
gang cutting ( milling)
Machining with several cutters mounted on a single arbor, generally for simultaneous cutting.
- grinding
grinding
Machining operation in which material is removed from the workpiece by a powered abrasive wheel, stone, belt, paste, sheet, compound, slurry, etc. Takes various forms: surface grinding (creates flat and/or squared surfaces); cylindrical grinding (for external cylindrical and tapered shapes, fillets, undercuts, etc.); centerless grinding; chamfering; thread and form grinding; tool and cutter grinding; offhand grinding; lapping and polishing (grinding with extremely fine grits to create ultrasmooth surfaces); honing; and disc grinding.
- micron
micron
Measure of length that is equal to one-millionth of a meter.
- milling
milling
Machining operation in which metal or other material is removed by applying power to a rotating cutter. In vertical milling, the cutting tool is mounted vertically on the spindle. In horizontal milling, the cutting tool is mounted horizontally, either directly on the spindle or on an arbor. Horizontal milling is further broken down into conventional milling, where the cutter rotates opposite the direction of feed, or “up” into the workpiece; and climb milling, where the cutter rotates in the direction of feed, or “down” into the workpiece. Milling operations include plane or surface milling, endmilling, facemilling, angle milling, form milling and profiling.