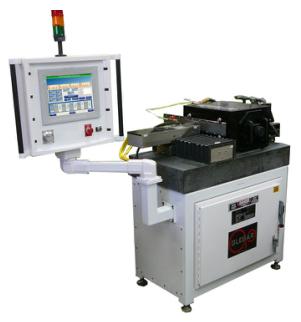
Dressing grinding wheels offline allows manufacturers to use their grinding equipment for production, reduces set up time, improves quality, and ultimately increases throughput. Manual contour dressers are operator-dependent and inconsistent, affecting the quality of the grind and increasing scrap rates. Utilization of a contour dresser generally requires more frequent dressing, reducing the lifespan of the wheel and increasing consumable costs.
Glebar’s DM-9CNC Wheel Dressing Machine is a stand-alone machine that provides operators with the ability to dress grinding wheels while the grinder is in production. Available for 9” and 10” diameter wheels, the machine CNC dresses precision contours in vitrified grinding wheels. The shape can be transferred from a CAD drawing into G-code which the DM-9CNC can read to form the wheel. Alternatively, for simpler geometry, the operator can enter the dress profile in a tabulated form on the 15” touch screen HMI. A diamond plated dress roller is powered by a high-speed brushless servo motor offering high torque and closed-loop velocity control up to 10,000 RPM. Additionally, two axis servo-driven slides use a 0.1 micron glass scale to precisely position the dress roller.
“Dressing wheels off of the grinding machine itself has typically been a manual operation requiring a highly skilled technician, often resulting in rework and increased set up time. Once the DM-9CNC is set up, it can run unmanned, shaping a grinding wheel for your specific application,” explained John Bannayan, CTO at Glebar Company. “This allows the manufacturer to run their grinding machine process while simultaneously truing a wheel for the next job, reducing set up time and increasing overall output.”
When purchasing a machine isn’t practical, Glebar offers its customers wheel dressing as a service using the DM-9CNC Wheel Dressing Machine.
Contact Details
Related Glossary Terms
- computer numerical control ( CNC)
computer numerical control ( CNC)
Microprocessor-based controller dedicated to a machine tool that permits the creation or modification of parts. Programmed numerical control activates the machine’s servos and spindle drives and controls the various machining operations. See DNC, direct numerical control; NC, numerical control.
- computer-aided design ( CAD)
computer-aided design ( CAD)
Product-design functions performed with the help of computers and special software.
- dressing
dressing
Removal of undesirable materials from “loaded” grinding wheels using a single- or multi-point diamond or other tool. The process also exposes unused, sharp abrasive points. See loading; truing.
- grinding
grinding
Machining operation in which material is removed from the workpiece by a powered abrasive wheel, stone, belt, paste, sheet, compound, slurry, etc. Takes various forms: surface grinding (creates flat and/or squared surfaces); cylindrical grinding (for external cylindrical and tapered shapes, fillets, undercuts, etc.); centerless grinding; chamfering; thread and form grinding; tool and cutter grinding; offhand grinding; lapping and polishing (grinding with extremely fine grits to create ultrasmooth surfaces); honing; and disc grinding.
- grinding machine
grinding machine
Powers a grinding wheel or other abrasive tool for the purpose of removing metal and finishing workpieces to close tolerances. Provides smooth, square, parallel and accurate workpiece surfaces. When ultrasmooth surfaces and finishes on the order of microns are required, lapping and honing machines (precision grinders that run abrasives with extremely fine, uniform grits) are used. In its “finishing” role, the grinder is perhaps the most widely used machine tool. Various styles are available: bench and pedestal grinders for sharpening lathe bits and drills; surface grinders for producing square, parallel, smooth and accurate parts; cylindrical and centerless grinders; center-hole grinders; form grinders; facemill and endmill grinders; gear-cutting grinders; jig grinders; abrasive belt (backstand, swing-frame, belt-roll) grinders; tool and cutter grinders for sharpening and resharpening cutting tools; carbide grinders; hand-held die grinders; and abrasive cutoff saws.
- grinding wheel
grinding wheel
Wheel formed from abrasive material mixed in a suitable matrix. Takes a variety of shapes but falls into two basic categories: one that cuts on its periphery, as in reciprocating grinding, and one that cuts on its side or face, as in tool and cutter grinding.
- micron
micron
Measure of length that is equal to one-millionth of a meter.
- shaping
shaping
Using a shaper primarily to produce flat surfaces in horizontal, vertical or angular planes. It can also include the machining of curved surfaces, helixes, serrations and special work involving odd and irregular shapes. Often used for prototype or short-run manufacturing to eliminate the need for expensive special tooling or processes.
- truing
truing
Using a diamond or other dressing tool to ensure that a grinding wheel is round and concentric and will not vibrate at required speeds. Weights also are used to balance the wheel. Also performed to impart a contour to the wheel’s face. See dressing.