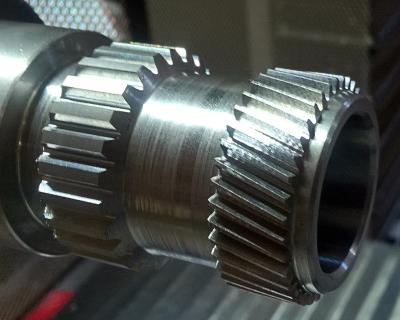
CNC specialist NUM has further extended the functionality of its renowned NUMgear family of gear production technology with the addition of an extremely flexible software option for power skiving.
NUM’s new power skiving option provides the enabling technology for CNC machine tool companies to address a key market opportunity in the nascent compact gearbox manufacturing industry. It is now possible to create an entirely new generation of gear production automation that offers combined hobbing and skiving capabilities on a single machine.
Gear manufacturers currently employ a variety of machining processes, including hobbing, shaping, broaching and grinding. To a large extent, the processes that are used are dictated by the type and size of the gears and splines being produced. Hobbing is ideal for external gears, while shaping and broaching are best suited to the production of internal gears – but the latter is only really practicable with small gears. Power skiving, on the other hand, is potentially a much faster and more efficient way of creating external and internal gears of any size.
However, despite being developed and patented more than 100 years ago, it is only recently, with the advent of multi-axis machine tools capable of precision high-speed synchronization, that the technique of power skiving has become a practicable proposition for industrial-scale use.
Based on NUM’s high performance Flexium+ CNC platform, the new power skiving solution forms the latest addition to the company’s NUMgear suite of gear production software. Originally developed specifically for gear hobbing applications, NUMgear is continually enhanced to meet industrial requirements and nowadays offers solutions for a broad range of gear manufacturing processes; it is used by many leading manufacturers of gear production machines.
The new power skiving software capitalizes on the speed and precision of NUM’s advanced multi-level electronic gearbox (MLEGB). This very high performance unit is capable of unprecedented speed and accuracy – it can handle up to 25,000 rpm on the leading axis, and uses look-ahead algorithms to predict both the speed and the acceleration of axes, in order to minimize synchronization time.
The characteristics of the MLEGB are user-defined in the part program. Any axis can be nominated as leading or following, linear or rotary, and the ratio between the leading and following axes can be controlled by a user-defined fixed parameter or a dynamic machine-cycle variable (curve table). Flexibility is even further enhanced by the fact that multiple MLEGBs can be cascaded, a following axis in a dynamic gearbox can be used as a leading axis in another MLEGB, and either the leading or following axis in an EGB can be real or virtual.
A single multi-role CNC machine tool that offers gear manufacturers the ability to hob large gears and to power skive smaller gears on one shaft, or whenever tool space is constricted – such as in a compact gearbox – would almost certainly enjoy rapid industry take-up. Thanks to NUM, the CNC control technology, together with the necessary precision servomotors and drives, is now a reality.
NUM’s new power skiving software option can be installed and used on any Flexium+ CNC system running Flexium software version 4.1.00.00 or higher.
Contact Details
Related Glossary Terms
- broaching
broaching
Operation in which a cutter progressively enlarges a slot or hole or shapes a workpiece exterior. Low teeth start the cut, intermediate teeth remove the majority of the material and high teeth finish the task. Broaching can be a one-step operation, as opposed to milling and slotting, which require repeated passes. Typically, however, broaching also involves multiple passes.
- computer numerical control ( CNC)
computer numerical control ( CNC)
Microprocessor-based controller dedicated to a machine tool that permits the creation or modification of parts. Programmed numerical control activates the machine’s servos and spindle drives and controls the various machining operations. See DNC, direct numerical control; NC, numerical control.
- grinding
grinding
Machining operation in which material is removed from the workpiece by a powered abrasive wheel, stone, belt, paste, sheet, compound, slurry, etc. Takes various forms: surface grinding (creates flat and/or squared surfaces); cylindrical grinding (for external cylindrical and tapered shapes, fillets, undercuts, etc.); centerless grinding; chamfering; thread and form grinding; tool and cutter grinding; offhand grinding; lapping and polishing (grinding with extremely fine grits to create ultrasmooth surfaces); honing; and disc grinding.
- look-ahead
look-ahead
CNC feature that evaluates many data blocks ahead of the cutting tool’s location to adjust the machining parameters to prevent gouges. This occurs when the feed rate is too high to stop the cutting tool within the required distance, resulting in an overshoot of the tool’s projected path. Ideally, look-ahead should be dynamic, varying the distance and number of program blocks based on the part profile and the desired feed rate.
- shaping
shaping
Using a shaper primarily to produce flat surfaces in horizontal, vertical or angular planes. It can also include the machining of curved surfaces, helixes, serrations and special work involving odd and irregular shapes. Often used for prototype or short-run manufacturing to eliminate the need for expensive special tooling or processes.