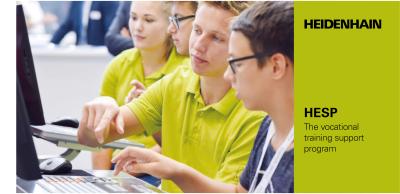
To assist in training the next generation of manufacturing professionals, HEIDENHAIN is offering a collection of educational services and products to meet the demands for today’s digitization of data in NC metalworking. This worldwide initiative called the HEIDENHAIN Education Support Program (HESP) promises to bring the latest advancements on the shop floor to current classrooms of vocational training centers, universities, and corporate trainee programs.
Digital services and their remarkable speed are now commonplace and only growing. With HESP, HEIDENHAIN is making its own important contribution to training the next generation of metalworkers by providing highly cost-effective, state-of-the-art resources to educators that can include computer programming stations, software and learning materials for fast and highly accurate milling and turning needs. HESP also includes offers to train the trainers at significantly reduced prices.
HEIDENHAIN’s programming stations are based on the same software foundation as its CNC controls, thus making them ideal vocational training tools to give students the confidence they need to program in the manufacturing world. HESP’s learning materials include practical course supplies for explaining complex topics, as well support posters for the classroom.
Those that are familiar with HEIDENHAIN will especially appreciate the special opportunity for educators to obtain HEIDENHAIN’s Connecting Machining package of functions and its StateMonitor MDA software, as well as the option of its online HIT (HEIDENHAIN Interactive Training) program.
Contact Details
Related Glossary Terms
- centers
centers
Cone-shaped pins that support a workpiece by one or two ends during machining. The centers fit into holes drilled in the workpiece ends. Centers that turn with the workpiece are called “live” centers; those that do not are called “dead” centers.
- computer numerical control ( CNC)
computer numerical control ( CNC)
Microprocessor-based controller dedicated to a machine tool that permits the creation or modification of parts. Programmed numerical control activates the machine’s servos and spindle drives and controls the various machining operations. See DNC, direct numerical control; NC, numerical control.
- gang cutting ( milling)
gang cutting ( milling)
Machining with several cutters mounted on a single arbor, generally for simultaneous cutting.
- metalworking
metalworking
Any manufacturing process in which metal is processed or machined such that the workpiece is given a new shape. Broadly defined, the term includes processes such as design and layout, heat-treating, material handling and inspection.
- milling
milling
Machining operation in which metal or other material is removed by applying power to a rotating cutter. In vertical milling, the cutting tool is mounted vertically on the spindle. In horizontal milling, the cutting tool is mounted horizontally, either directly on the spindle or on an arbor. Horizontal milling is further broken down into conventional milling, where the cutter rotates opposite the direction of feed, or “up” into the workpiece; and climb milling, where the cutter rotates in the direction of feed, or “down” into the workpiece. Milling operations include plane or surface milling, endmilling, facemilling, angle milling, form milling and profiling.
- numerical control ( NC)
numerical control ( NC)
Any controlled equipment that allows an operator to program its movement by entering a series of coded numbers and symbols. See CNC, computer numerical control; DNC, direct numerical control.
- turning
turning
Workpiece is held in a chuck, mounted on a face plate or secured between centers and rotated while a cutting tool, normally a single-point tool, is fed into it along its periphery or across its end or face. Takes the form of straight turning (cutting along the periphery of the workpiece); taper turning (creating a taper); step turning (turning different-size diameters on the same work); chamfering (beveling an edge or shoulder); facing (cutting on an end); turning threads (usually external but can be internal); roughing (high-volume metal removal); and finishing (final light cuts). Performed on lathes, turning centers, chucking machines, automatic screw machines and similar machines.