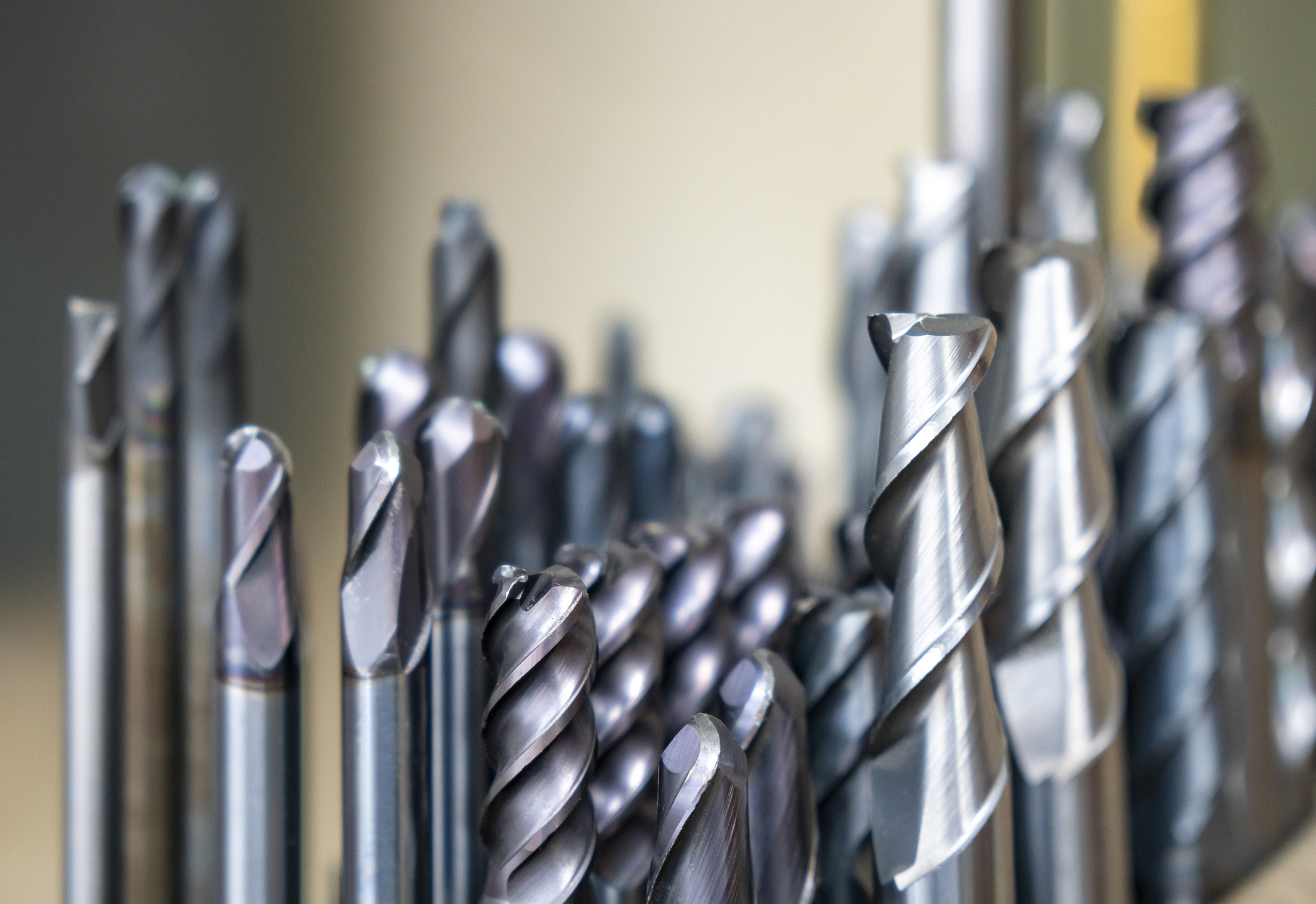
Thomson Mathew, ANCA’s software product manager and the architect of many of ANCA’s software products, has written a technical guide on creating the perfect endmill.
In part 1 of a five-part instructional series, Matthew looks at the factors that impact the overall performance of an endmill and the “weird” endmills that have higher geometrical levels of complexity.
Part one: Geometry design and parameter verification
Every endmill begins with design and a well-designed geometry can make a high-performance endmill.
There are many factors that will impact the overall performance of an endmill. Four major ones that get cited are the grade or quality of carbide material, the cutting tool geometry design, the precision manufacturing process or quality control and the type of coating.
The hardness of an endmill’s material, usually carbide, will depend on the grade of carbide in the matrix. Smaller grains mean more substance versus binder, and therefore a harder tool. Exotic coatings will improve lifespan and cutting performance. Quality control means a workshop can get a consistent result.
But geometry has an outsized role, one that highlights the blend of art and engineering – and for a long time, trial and error – involved in creating the ideal endmill. This begins with design. Some of the important factors in endmill design include the combination of both variable helix and index flute geometry design, core geometry design, the OD clearance angles eccentric versus facet reliefs design, endface design with wiper flats and pad grinding or end dubbing etc. each time from a set of endmills.
As I have written elsewhere, the progress of the industry has seen endmills grow increasingly “weird” as toolmakers have sought high material removal rates while avoiding “chatter”.
Regenerative chatter happens when the harmonics between a tool and workpiece are at different frequencies. The two self-excited objects will hit against each other, which is a negative for surface finish and dimensional accuracy, as well as the lifespan of the tool and machinery. It is a drain on productivity and profits.
High helix tools (over 35 degrees) have long been popular for their strength and fast feed and swarf removal rates. While they have these advantages over low helix endmills for hard materials, they are also the more prone of the two to chatter. Some of the trial and error to combat this has been around variable helixes and pitches and trying to better balance tools. This has led to “weird” endmills, with higher geometrical levels of complexity.
In high helix tools the cutting forces are directed more vertically and less horizontally, which reduces tool deflection and results in quick and efficient chip evacuation.
More positive axial rake lowers cutting forces which helps to increase feedrates. The core of the tool is thicker due to the shape of the helix and the tool is stronger. High helix endmills are typically used in tougher harder materials because they wear better, although they can also be used in softer materials like aluminium. One disadvantage of high helix endmills is the tendency to chatter more, and they really bite into the material.
On the contrary, low helix tools are less likely to chatter and typically perform better in soft materials. Their disadvantage is the lower feedrates and hence lower material removal rates. Our understanding of how to mitigate chatter has come a long way and involves no guesswork nowadays. The geometry and design are purely based on material to be cut whether it is soft or hard.
Variable helix end mills with variable index are considered state of the art these days. The idea is to vary the helix along the flute length or from flute-to-flute. The aim of the variable helix is to fight chatter. Since chatter is a resonance effect, anything we can do to break up the resonance of the flutes beating against the workpiece will reduce chatter. The tool balancing capabilities in the RN34 release of ANCA’s ToolRoom software is the perfect solution to combat chatter.
Contact Details
Related Glossary Terms
- axial rake
axial rake
On angular tool flutes, the angle between the tooth face and the axial plane through the tool point.
- chatter
chatter
Condition of vibration involving the machine, workpiece and cutting tool. Once this condition arises, it is often self-sustaining until the problem is corrected. Chatter can be identified when lines or grooves appear at regular intervals in the workpiece. These lines or grooves are caused by the teeth of the cutter as they vibrate in and out of the workpiece and their spacing depends on the frequency of vibration.
- clearance
clearance
Space provided behind a tool’s land or relief to prevent rubbing and subsequent premature deterioration of the tool. See land; relief.
- endmill
endmill
Milling cutter held by its shank that cuts on its periphery and, if so configured, on its free end. Takes a variety of shapes (single- and double-end, roughing, ballnose and cup-end) and sizes (stub, medium, long and extra-long). Also comes with differing numbers of flutes.
- feed
feed
Rate of change of position of the tool as a whole, relative to the workpiece while cutting.
- flutes
flutes
Grooves and spaces in the body of a tool that permit chip removal from, and cutting-fluid application to, the point of cut.
- grinding
grinding
Machining operation in which material is removed from the workpiece by a powered abrasive wheel, stone, belt, paste, sheet, compound, slurry, etc. Takes various forms: surface grinding (creates flat and/or squared surfaces); cylindrical grinding (for external cylindrical and tapered shapes, fillets, undercuts, etc.); centerless grinding; chamfering; thread and form grinding; tool and cutter grinding; offhand grinding; lapping and polishing (grinding with extremely fine grits to create ultrasmooth surfaces); honing; and disc grinding.
- hardness
hardness
Hardness is a measure of the resistance of a material to surface indentation or abrasion. There is no absolute scale for hardness. In order to express hardness quantitatively, each type of test has its own scale, which defines hardness. Indentation hardness obtained through static methods is measured by Brinell, Rockwell, Vickers and Knoop tests. Hardness without indentation is measured by a dynamic method, known as the Scleroscope test.
- outer diameter ( OD)
outer diameter ( OD)
Dimension that defines the exterior diameter of a cylindrical or round part. See ID, inner diameter.
- quality assurance ( quality control)
quality assurance ( quality control)
Terms denoting a formal program for monitoring product quality. The denotations are the same, but QC typically connotes a more traditional postmachining inspection system, while QA implies a more comprehensive approach, with emphasis on “total quality,” broad quality principles, statistical process control and other statistical methods.
- rake
rake
Angle of inclination between the face of the cutting tool and the workpiece. If the face of the tool lies in a plane through the axis of the workpiece, the tool is said to have a neutral, or zero, rake. If the inclination of the tool face makes the cutting edge more acute than when the rake angle is zero, the rake is positive. If the inclination of the tool face makes the cutting edge less acute or more blunt than when the rake angle is zero, the rake is negative.
- swarf
swarf
Metal fines and grinding wheel particles generated during grinding.
- wiper
wiper
Metal-removing edge on the face of a cutter that travels in a plane perpendicular to the axis. It is the edge that sweeps the machined surface. The flat should be as wide as the feed per revolution of the cutter. This allows any given insert to wipe the entire workpiece surface and impart a fine surface finish at a high feed rate.