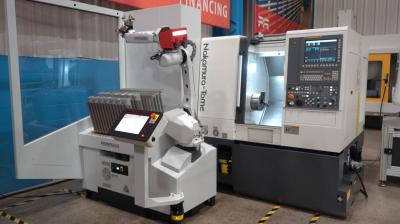
Methods Machine Tools, the foremost supplier of high-quality, high-precision CNC machine tools and automation in North America, has released the Turn-Assist 200i and 270i from RoboJob as its first, end-to-end standard automation system for Nakamura-Tome turning centers.
A semi-collaborative system engineered for lathe automation, Turn-Assist is designed to be implemented and run by operators of any skill level. With a simple tablet-style HMI and standard Ethernet IP interface, shops can successfully change over from one part to another within minutes.
“By pairing the Turn-Assist from RoboJob with Nakamura-Tome, we have created a unique automation solution for high-mix/low-volume and/or mid-volume with frequent changeovers on round workpieces often associated with Nakamura lathes,” said Zach Spencer, Methods’ Automation Manager.
“As Methods provides the machine, the options, the automation system, and the interface, along with the installation, training and support, customers have the advantage of working with one supplier for the entire technology and experience stack.”
Turn-Assist features an open-floor setup and area sensors to maximize operator safety and accessibility, while a pre-programmable FANUC robot loads blanks and unloads finished parts from the stocking table. Options are available that allows the robot to process shafts, rotate parts, and interface with a bar-feeder.
Additionally, the integrated, automatic air blow nozzle on the dual, three-jaw gripper enables the robot to discard chips and coolant away from the workholding further streamlining operations without any manual intervention.
“Methods and Nakamura-Tome together have served customers for decades with industry-best solutions. In introducing Turn-Assist for Nakamura-Tome, machine owners gain a user-friendly, reliable automation system that will increase efficiency and output on Day 1 without any operator upskilling requirements,” added Sergio Tondato, Methods’ Nakamura-Tome product manager.
Contact Details
Related Glossary Terms
- centers
centers
Cone-shaped pins that support a workpiece by one or two ends during machining. The centers fit into holes drilled in the workpiece ends. Centers that turn with the workpiece are called “live” centers; those that do not are called “dead” centers.
- computer numerical control ( CNC)
computer numerical control ( CNC)
Microprocessor-based controller dedicated to a machine tool that permits the creation or modification of parts. Programmed numerical control activates the machine’s servos and spindle drives and controls the various machining operations. See DNC, direct numerical control; NC, numerical control.
- coolant
coolant
Fluid that reduces temperature buildup at the tool/workpiece interface during machining. Normally takes the form of a liquid such as soluble or chemical mixtures (semisynthetic, synthetic) but can be pressurized air or other gas. Because of water’s ability to absorb great quantities of heat, it is widely used as a coolant and vehicle for various cutting compounds, with the water-to-compound ratio varying with the machining task. See cutting fluid; semisynthetic cutting fluid; soluble-oil cutting fluid; synthetic cutting fluid.
- lathe
lathe
Turning machine capable of sawing, milling, grinding, gear-cutting, drilling, reaming, boring, threading, facing, chamfering, grooving, knurling, spinning, parting, necking, taper-cutting, and cam- and eccentric-cutting, as well as step- and straight-turning. Comes in a variety of forms, ranging from manual to semiautomatic to fully automatic, with major types being engine lathes, turning and contouring lathes, turret lathes and numerical-control lathes. The engine lathe consists of a headstock and spindle, tailstock, bed, carriage (complete with apron) and cross slides. Features include gear- (speed) and feed-selector levers, toolpost, compound rest, lead screw and reversing lead screw, threading dial and rapid-traverse lever. Special lathe types include through-the-spindle, camshaft and crankshaft, brake drum and rotor, spinning and gun-barrel machines. Toolroom and bench lathes are used for precision work; the former for tool-and-die work and similar tasks, the latter for small workpieces (instruments, watches), normally without a power feed. Models are typically designated according to their “swing,” or the largest-diameter workpiece that can be rotated; bed length, or the distance between centers; and horsepower generated. See turning machine.
- turning
turning
Workpiece is held in a chuck, mounted on a face plate or secured between centers and rotated while a cutting tool, normally a single-point tool, is fed into it along its periphery or across its end or face. Takes the form of straight turning (cutting along the periphery of the workpiece); taper turning (creating a taper); step turning (turning different-size diameters on the same work); chamfering (beveling an edge or shoulder); facing (cutting on an end); turning threads (usually external but can be internal); roughing (high-volume metal removal); and finishing (final light cuts). Performed on lathes, turning centers, chucking machines, automatic screw machines and similar machines.