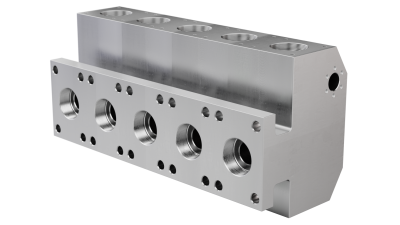
Century Tool and Gage, a Tooling Tech Group company and a precision machining and composites tooling specialist, has announced its ability to provide the machining services required for producing fracking blocks, also known as fluid-end blocks or quints. Fluid ends are large, heavy components made from solid blocks of steel, requiring days of machining time including milling, drilling and threading operations.
“With our experience in machining extremely large compression molds for forming composite components, Century is well-equipped to produce fluid ends for the energy industry,” said John-Paul Mead, general manager. “We have the machine tool resource as well as the staff to effectively produce these heavy-wear parts.”
Century has an 89,900 sq. ft. facility with 40-ton cranes and 15 high performance machine tools for drilling, milling, 3D roughing, semi finishing and finishing of both steel and aluminum, enabling it to achieve complex geometries and exacting tolerances. The company can produce structures in excess of 100,000 lbs. and sizes of up to 343” long by 100” deep by 120” tall.
Contact Details
Related Glossary Terms
- composites
composites
Materials composed of different elements, with one element normally embedded in another, held together by a compatible binder.
- gang cutting ( milling)
gang cutting ( milling)
Machining with several cutters mounted on a single arbor, generally for simultaneous cutting.
- milling
milling
Machining operation in which metal or other material is removed by applying power to a rotating cutter. In vertical milling, the cutting tool is mounted vertically on the spindle. In horizontal milling, the cutting tool is mounted horizontally, either directly on the spindle or on an arbor. Horizontal milling is further broken down into conventional milling, where the cutter rotates opposite the direction of feed, or “up” into the workpiece; and climb milling, where the cutter rotates in the direction of feed, or “down” into the workpiece. Milling operations include plane or surface milling, endmilling, facemilling, angle milling, form milling and profiling.
- precision machining ( precision measurement)
precision machining ( precision measurement)
Machining and measuring to exacting standards. Four basic considerations are: dimensions, or geometrical characteristics such as lengths, angles and diameters of which the sizes are numerically specified; limits, or the maximum and minimum sizes permissible for a specified dimension; tolerances, or the total permissible variations in size; and allowances, or the prescribed differences in dimensions between mating parts.
- threading
threading
Process of both external (e.g., thread milling) and internal (e.g., tapping, thread milling) cutting, turning and rolling of threads into particular material. Standardized specifications are available to determine the desired results of the threading process. Numerous thread-series designations are written for specific applications. Threading often is performed on a lathe. Specifications such as thread height are critical in determining the strength of the threads. The material used is taken into consideration in determining the expected results of any particular application for that threaded piece. In external threading, a calculated depth is required as well as a particular angle to the cut. To perform internal threading, the exact diameter to bore the hole is critical before threading. The threads are distinguished from one another by the amount of tolerance and/or allowance that is specified. See turning.