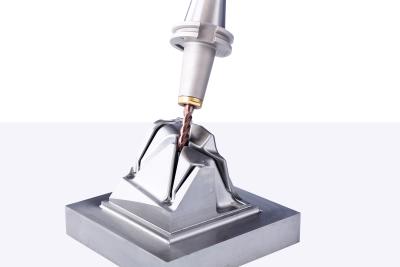
Accutek Inc. now offers new end mill and shrink fit holder coolant technology. Since a high percentage of CNC machine tools are now being purchased with coolant through the spindle options, it is important to make sure you coolant gets to the the cutting edges of your cutting tools. Coolant is not only a cooling agent, it is also a cutting edge lubricant so make sure your cutting edges get maximum efficiency from your cutting fluids during the machining processes.
Accutek now offers two different types of AccuKool Coolant ports with our End Mill holders and our AccuGrip Shrink fit holders.
End Mill holders are now available with two coolant ports 180° apart and angled at the cutting tool to properly place the coolant into the “vortex” of the spinning cutting tool for maximum cooling and lubrication benefits.
AccuGripTM Shrink fit holders will have three coolant ports 120° apart and angled at the cutting edges of the cutting tool for maximum cooling and lubrucation benefits.
Diebold JetSleeve 2.0 technology offers a unique coolant supply system that is unmatched by any other tool holder product. The JetSleeve 2.0 patented design not only delivers coolant to the cutting edges of your cutting tools, but it also it accelerates the coolant multiple times over the “normal” machine coolant pressure to blast the chips/swarf away for the machined surfaces to eliminate recutting of chips that leads to shorter tool life and prevents smooth machined surfaces.
The Jet Sleeve 2.0 technology offers a “Gold Ring” Nozzle at the end of the Diebold shrink fit holders. This nozzle has tiny holes and varying angles that not only “twist” the coolant as it enters the “vortex” but these holes cause the coolant pressure to increase and create a strong coolant flow that blasts all chip away from the cutting tool path and cavity if you are machining down into a part. This is a great application for high production setups for machining high-nickel material, die mold materials, medical parts, and aerospace parts.
This same Jet Sleeve technology is also available with the Diebold UltraJet Power Chucks.
Contact Details
Related Glossary Terms
- computer numerical control ( CNC)
computer numerical control ( CNC)
Microprocessor-based controller dedicated to a machine tool that permits the creation or modification of parts. Programmed numerical control activates the machine’s servos and spindle drives and controls the various machining operations. See DNC, direct numerical control; NC, numerical control.
- coolant
coolant
Fluid that reduces temperature buildup at the tool/workpiece interface during machining. Normally takes the form of a liquid such as soluble or chemical mixtures (semisynthetic, synthetic) but can be pressurized air or other gas. Because of water’s ability to absorb great quantities of heat, it is widely used as a coolant and vehicle for various cutting compounds, with the water-to-compound ratio varying with the machining task. See cutting fluid; semisynthetic cutting fluid; soluble-oil cutting fluid; synthetic cutting fluid.
- milling machine ( mill)
milling machine ( mill)
Runs endmills and arbor-mounted milling cutters. Features include a head with a spindle that drives the cutters; a column, knee and table that provide motion in the three Cartesian axes; and a base that supports the components and houses the cutting-fluid pump and reservoir. The work is mounted on the table and fed into the rotating cutter or endmill to accomplish the milling steps; vertical milling machines also feed endmills into the work by means of a spindle-mounted quill. Models range from small manual machines to big bed-type and duplex mills. All take one of three basic forms: vertical, horizontal or convertible horizontal/vertical. Vertical machines may be knee-type (the table is mounted on a knee that can be elevated) or bed-type (the table is securely supported and only moves horizontally). In general, horizontal machines are bigger and more powerful, while vertical machines are lighter but more versatile and easier to set up and operate.