Having the right cutting tool for a job does not help get the job done if a manufacturer does not know that it has the tool. That sometimes occurred at the Athens, Alabama, production facility of Intech, a manufacturer of medical devices and equipment, said Joseph Forsyth, director of advanced manufacturing at Intech.
“If you don’t know what tools you have for sure,” he said, “then you’re not really going to have a clear understanding of what you can do.”
Having managed the shop floor, Forsyth said he was familiar with almost all the machining tasks performed at the plant.
“I understand every struggle right down to the very floor level,” he said.
After trying numerous solutions to fix even some of the simplest problems, Forsyth said the shop achieved small successes “but nothing that ever really came all together.”
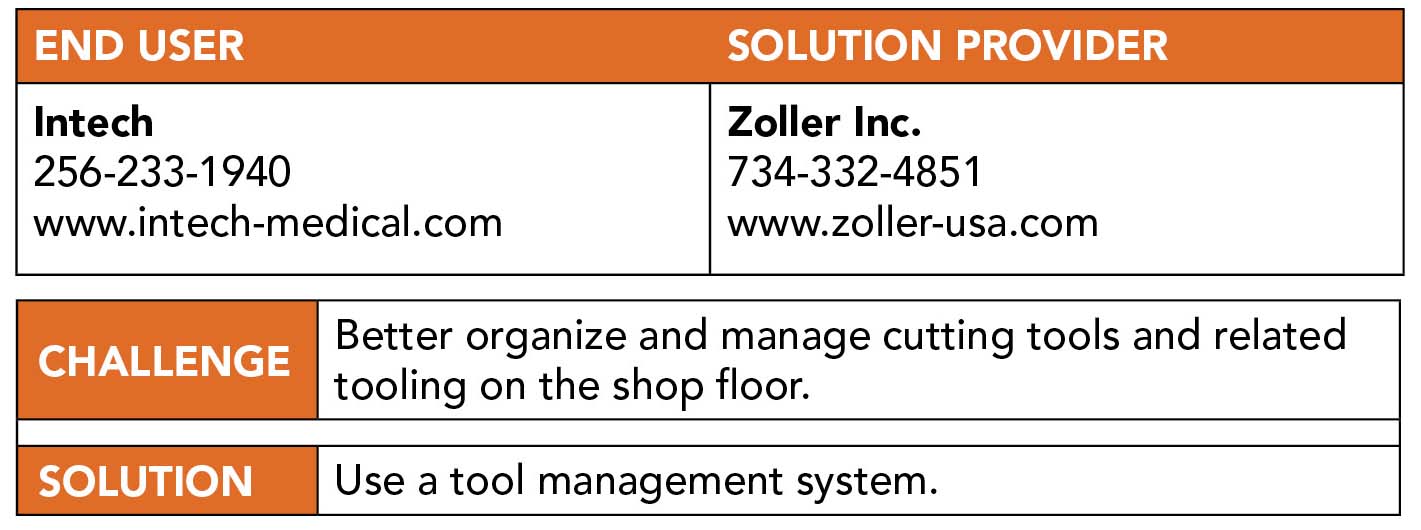
A number of years ago, Intech bought a tool presetter from Zoller Inc. in Ann Arbor, Michigan, after he visited the French parent company following its purchase of Turner Medical Inc., the business he was working for.
“When I was introduced to the Zoller system and the software, I didn’t really understand it at the time,” Forsyth said. “But I just knew that the older gentlemen I met in France knew their stuff, and if they’re on to something, then you might want to pay attention. We bought a presetter first, thinking that was all we really needed.”
Realizing that Intech was getting only a small sample of what was possible with the presetter, he started researching tool management systems to compare them with the Zoller TMS but found they all were based on software.
“Anything that competes with Zoller TMS doesn’t have any well-integrated hardware solutions to go along with it,” Forsyth said.
Intech purchased the Zoller TMS with the Gold software package to have the necessary capabilities. With the system in place, he said the medical manufacturer needed to decide how to begin the system integration process.
“All of it was there,” Forsyth said, “but you can’t use it all at once. It’s just too expansive.”
He said basic development began in the first quarter of 2022, with training key users, developing nomenclature and establishing group structures for all the modules. The TMS timeline for the second quarter primarily covered cataloging single components, or tools, as well as some accessories and fixtures.
Forsyth explained that Intech did a complete build of a small sample project to confirm the logic that the shop was using. With the logic established, the company started building all its single components over a four- or five-month period.
“Two guys just sitting there creating tool by tool,” he said.

Intech’s timeline for implementing TMS is based on quarters, but Forsyth said some of the broad milestones that he wanted to achieve have been accomplished sooner than expected while others have not.
“Those changed pretty significantly as we moved through the months due to unforeseen changes in the shop or work changes or new things we learned,” he said. “You pick a path, and sometimes you have to bob and weave to find your way.”
In addition, during the second quarter the company received two Kardex Remstar Shuttle XP 500 vertical lift modules to organize the shop floor by enabling high-density storage of supplies in a minimal footprint and prioritizing items that consume the most space.
“It was just getting out of control,” Forsyth said. “Our shop had gotten worse than we realized.”
During the third quarter, Intech started moving inventory into the Kardex modules and assigning locations in tandem with ongoing data creation. In the fourth quarter, the company set up the ordering functions of TMS and the reporting module.
The major milestone that Intech accomplished after the first year, Forsyth said, was to make the old hardware and software system at the shop obsolete.
“I wanted it out,” he said, “and I wanted to be in TMS fully by the end of the first year.”
Forsyth said at the conclusion of year one Intech had received a return on investment from the Zoller TMS Gold package and hardware.
“Our sales went up,” he said, “but our tooling consumption went down almost an equivalent number to what the investment was with Zoller TMS.”
Also, Forsyth said the remaining quantity of tools, which still was large, was not stored in a central toolroom, but in satellite stations such as Zoller Smart Cabinets near the people who used the tools.
“You can spread out everything and get the same level of control from a toolroom,” he said.
The first quarter of 2023 saw a shop wide rollout of tool vending at Intech, Forsyth said, as the company began issuing and ordering tools strictly through TMS.
At the time that this article was written, Intech was targeting programmer training for the second quarter of 2023, which involved intersection coding, G code program storage and capturing standards in the tool module. Parts management, with setup sheet development and conversion, was scheduled for the third quarter, and job management to redefine pre-stage workflow was scheduled for the fourth. CAM system selection and interface were set for the first quarter of 2024.
When implementing the Zoller TMS, Forsyth emphasized that it is important to take time to do things right.
“Don’t overthink it,” he said. “Don’t shortcut it. Don’t force it.”
Forsyth also noted the need for all TMS users to buy into the system, even if it involves overcoming resistance to new software technology.
“This system directly helped each and every one of my team members significantly,” he said, “so it was very easy for buying into it because they all saw how this can really help them do their jobs.”
That’s certainly the case when shop workers have access to the cutting tools they need.
“As we built out this system,” Forsyth said, “we were finding tooling we didn’t know we even had. We were making our tooling visible to us.”
Contact Details
Related Glossary Terms
- arbor
arbor
Shaft used for rotary support in machining applications. In grinding, the spindle for mounting the wheel; in milling and other cutting operations, the shaft for mounting the cutter.
- computer-aided manufacturing ( CAM)
computer-aided manufacturing ( CAM)
Use of computers to control machining and manufacturing processes.
- sawing machine ( saw)
sawing machine ( saw)
Machine designed to use a serrated-tooth blade to cut metal or other material. Comes in a wide variety of styles but takes one of four basic forms: hacksaw (a simple, rugged machine that uses a reciprocating motion to part metal or other material); cold or circular saw (powers a circular blade that cuts structural materials); bandsaw (runs an endless band; the two basic types are cutoff and contour band machines, which cut intricate contours and shapes); and abrasive cutoff saw (similar in appearance to the cold saw, but uses an abrasive disc that rotates at high speeds rather than a blade with serrated teeth).