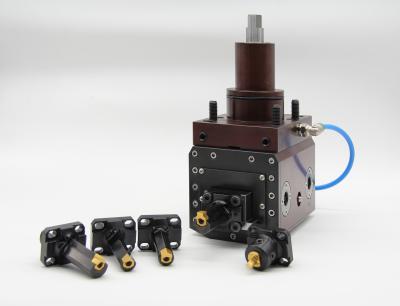
Platinum Tooling, the importer and master distributor of live tools, angle heads, speed increasers, Swiss machine products, knurling and marking tools and shrink fit tool holders manufactured by various international suppliers, will now carry REV broaching tools in North America. This announcement was made by Platinum Tooling president, Preben Hansen, at their headquarters in Prospect Heights, Illinois, near Chicago.
REV S.R.L., located in Northern Italy, is the manufacturer of innovative broaching solutions for CNC lathes and machining centers. The tools are ideal for machining simple keyways or internal and external profiles, both teeth and splines. Common profiles including square and hexagon are easily achieved and custom profiles are available. REV Broaching Tools offer excellent performance with long insert life and high surface quality.
The REV motorized broaching tool is designed for use on live tool lathes. Single machine set-up eliminates the need for secondary operation or outsourcing. REV tools are ideal for high production runs, offer easy installation and fast processing time. These tools are designed for maximum rigidity, offer long tool life and an excellent finish.
REV static broaching tools are for use on CNC lathes with or without Y-axis. They offer a patented eccentric bushing which eliminates alignment errors for machines without a Y-axis. The tools have a sturdy two-piece construction and are ideal for smaller runs. They are designed for use in boring bar holders on lathes and for use in collet chucks or Weldon holders on machining centers. REV tools allow for a wide variety of standard and custom profiles and sizes.
REV broaching tools are a perfect complement to the Heimatec live tools that are sold by the extensive network of Platinum Tooling manufacturers’ representatives and distributors throughout North America.
Contact Details
Related Glossary Terms
- boring
boring
Enlarging a hole that already has been drilled or cored. Generally, it is an operation of truing the previously drilled hole with a single-point, lathe-type tool. Boring is essentially internal turning, in that usually a single-point cutting tool forms the internal shape. Some tools are available with two cutting edges to balance cutting forces.
- boring bar
boring bar
Essentially a cantilever beam that holds one or more cutting tools in position during a boring operation. Can be held stationary and moved axially while the workpiece revolves around it, or revolved and moved axially while the workpiece is held stationary, or a combination of these actions. Installed on milling, drilling and boring machines, as well as lathes and machining centers.
- broaching
broaching
Operation in which a cutter progressively enlarges a slot or hole or shapes a workpiece exterior. Low teeth start the cut, intermediate teeth remove the majority of the material and high teeth finish the task. Broaching can be a one-step operation, as opposed to milling and slotting, which require repeated passes. Typically, however, broaching also involves multiple passes.
- bushing
bushing
Cylindrical sleeve, typically made from high-grade tool steel, inserted into a jig fixture to guide cutting tools. There are three main types: renewable, used in liners that in turn are installed in the jig; press-fit, installed directly in the jig for short production runs; and liner (or master), installed permanently in a jig to receive renewable bushing.
- centers
centers
Cone-shaped pins that support a workpiece by one or two ends during machining. The centers fit into holes drilled in the workpiece ends. Centers that turn with the workpiece are called “live” centers; those that do not are called “dead” centers.
- collet
collet
Flexible-sided device that secures a tool or workpiece. Similar in function to a chuck, but can accommodate only a narrow size range. Typically provides greater gripping force and precision than a chuck. See chuck.
- computer numerical control ( CNC)
computer numerical control ( CNC)
Microprocessor-based controller dedicated to a machine tool that permits the creation or modification of parts. Programmed numerical control activates the machine’s servos and spindle drives and controls the various machining operations. See DNC, direct numerical control; NC, numerical control.
- knurling
knurling
Chipless material-displacement process that is usually accomplished on a lathe by forcing a knurling die into the surface of a rotating workpiece to create a pattern. Knurling is often performed to create a decorative or gripping surface and repair undersized shafts.