In addition to 5-axis machine tools, manufacturers of aerospace parts must have the appropriate cutting tools for an application to remain competitive. Rather than choosing a standard tool grade for the spectrum of materials being machined and sacrificing productivity, these manufacturers are benefiting from the increasing amount of material-specific grades toolmakers are developing.
Sandvik Coromant Co. is one of the toolmakers that “completely optimized tools” for specific workpiece materials and machining techniques, according to William Durow, global engineering project office manager for the Mebane, North Carolina, company. For example, the toolmaker engineers solid-carbide endmill grades with geometries designed for cutting titanium while following a trochoidal toolpath.
In addition, machining heat-resistant superalloys (HRSA) is common in aerospace applications but challenging, nonetheless. To assist when finishing nickel-base superalloys, Durow said Sandvik Coromant developed the S205 turning grade for indexable inserts. The inserts have a second-generation Inveio coating for high wear resistance and long tool life, and are enhanced with a post-treatment technology that alters mechanical properties, the company reports. The Inveio layer features tightly packed, unidirectional crystals, which create a strong protective barrier around the insert to maximize thermal protection, improve crater wear and better resist flank wear.
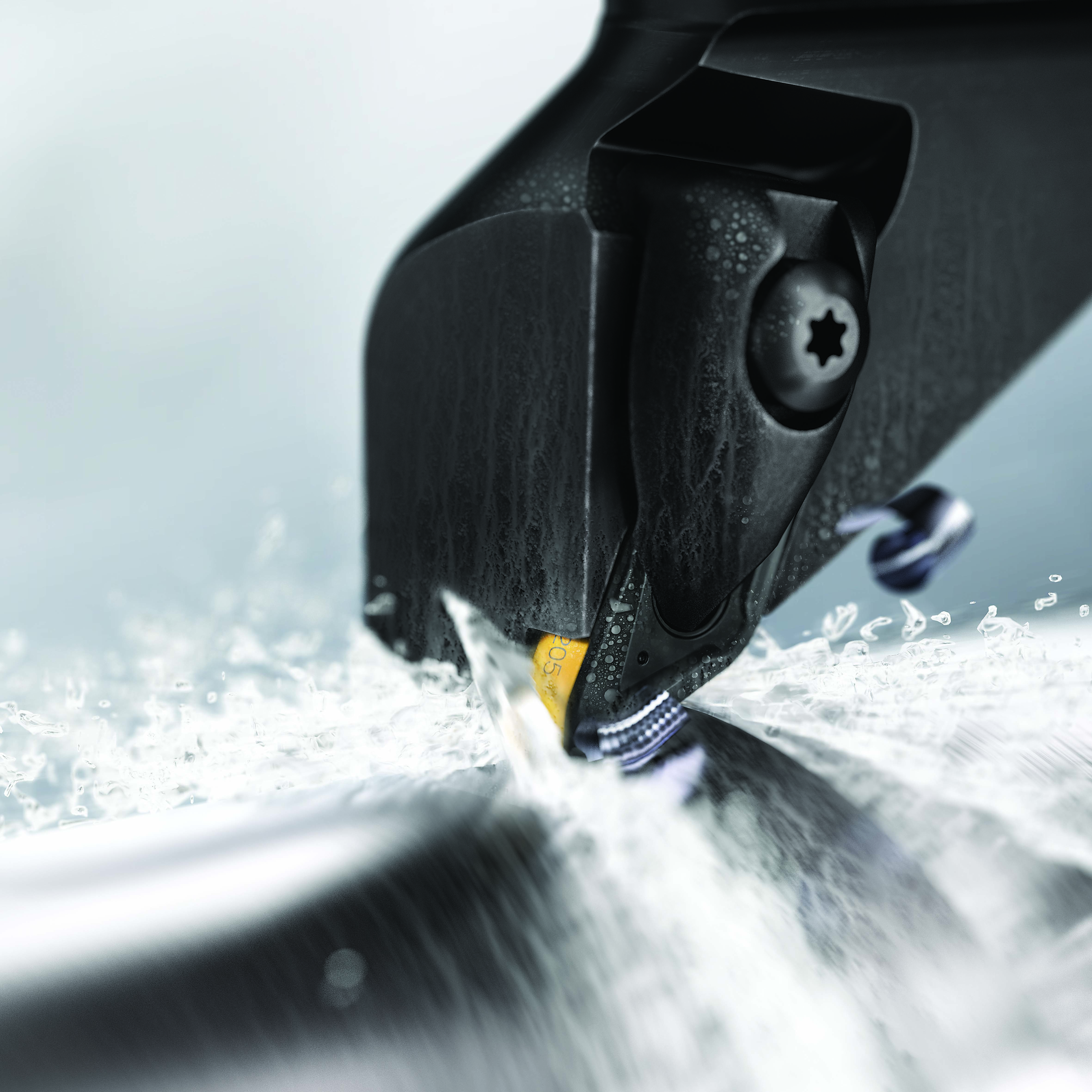
Because cutting a HRSA sends heat back into the tool rather than being primarily carried away with the chips, HRSA-specific grades are harder than other grades, Durow added. With light DOCs typically employed, the grades also have sharper geometries to shear rather than rub the material, creating less heat at the tool/workpiece interface.
Also helping to dissipate heat is high-pressure coolant streamed through channels that are targeted directly where it’s needed, he notes. “If you have flood coolant, usually what happens is there’s so much heat generated in the cut, you’re just vaporizing coolant in the cutting zone. Also in some applications, it helps move the chip off the top of the insert, so you’ll avoid crater wear on the top of the insert.”
Not only can the workpiece material be difficult-to-machine, but features found in many aerospace components present challenges, Durow said. These include disks, blisks and IBRs. “If you think about the ton of machining that goes into those, any little issue is going to create a very expensive scrap part.”
Regarding the former, the fir tree slots on disks were typically broached on large, expensive machines with pricey tools, according to Durow. Based on demand, Sandvik Coromant developed tools for achieving the same results on conventional machines.
While specials have their place, such as reaching deep into a bore and up into a groove to remove a friction weld, for example, Sandvik Coromant offers modular tool systems to minimize the needs for specials, Durow said. The SL70 modular blade system with the serration lock coupling is one. Using a 5-axis machine, the part can be tilted and moved to enable a modular tool to reach a feature that required a special previously.
CAM software developments in combination with 5-axis capability are enabling additional approaches. Durow explained how that combination can enable a continuous B-axis movement so a tool can sweep an entire feature and eliminate blend points that might cause an engine failure. These enhanced machining capabilities can even assist in engine design.
Introducing a new tool or technique for an already established process to produce a critical component, such as one in an engine or landing gear, however, “is a big ordeal” that can involve a lot of paperwork and part cut-ups to verify structural and surface integrity, Durow said. “You really need to make sure the performance you’re going to have exceeds what they’re looking for to justify all of that extra work they have to do on the back end to get the approval.”
The aerospace market has its ups and downs and not all manufacturers rise or fall with the tide, but “the whole aerospace market is booming,” Durow said. The situation is causing the supply chain to struggle to produce enough parts to satisfy the production requirements of OEMs. “There’s a huge demand right now in the cutting tool industry for producing aerospace parts, not only frame stuff but also engines.”
For more information about Sandvik Coromant Co., visit www.sandvik.coromant.com/us or call 800-SANDVIK.
Contact Details
Related Glossary Terms
- computer-aided manufacturing ( CAM)
computer-aided manufacturing ( CAM)
Use of computers to control machining and manufacturing processes.
- coolant
coolant
Fluid that reduces temperature buildup at the tool/workpiece interface during machining. Normally takes the form of a liquid such as soluble or chemical mixtures (semisynthetic, synthetic) but can be pressurized air or other gas. Because of water’s ability to absorb great quantities of heat, it is widely used as a coolant and vehicle for various cutting compounds, with the water-to-compound ratio varying with the machining task. See cutting fluid; semisynthetic cutting fluid; soluble-oil cutting fluid; synthetic cutting fluid.
- endmill
endmill
Milling cutter held by its shank that cuts on its periphery and, if so configured, on its free end. Takes a variety of shapes (single- and double-end, roughing, ballnose and cup-end) and sizes (stub, medium, long and extra-long). Also comes with differing numbers of flutes.
- flank wear
flank wear
Reduction in clearance on the tool’s flank caused by contact with the workpiece. Ultimately causes tool failure.
- mechanical properties
mechanical properties
Properties of a material that reveal its elastic and inelastic behavior when force is applied, thereby indicating its suitability for mechanical applications; for example, modulus of elasticity, tensile strength, elongation, hardness and fatigue limit.
- superalloys
superalloys
Tough, difficult-to-machine alloys; includes Hastelloy, Inconel and Monel. Many are nickel-base metals.
- toolpath( cutter path)
toolpath( cutter path)
2-D or 3-D path generated by program code or a CAM system and followed by tool when machining a part.
- turning
turning
Workpiece is held in a chuck, mounted on a face plate or secured between centers and rotated while a cutting tool, normally a single-point tool, is fed into it along its periphery or across its end or face. Takes the form of straight turning (cutting along the periphery of the workpiece); taper turning (creating a taper); step turning (turning different-size diameters on the same work); chamfering (beveling an edge or shoulder); facing (cutting on an end); turning threads (usually external but can be internal); roughing (high-volume metal removal); and finishing (final light cuts). Performed on lathes, turning centers, chucking machines, automatic screw machines and similar machines.
- wear resistance
wear resistance
Ability of the tool to withstand stresses that cause it to wear during cutting; an attribute linked to alloy composition, base material, thermal conditions, type of tooling and operation and other variables.