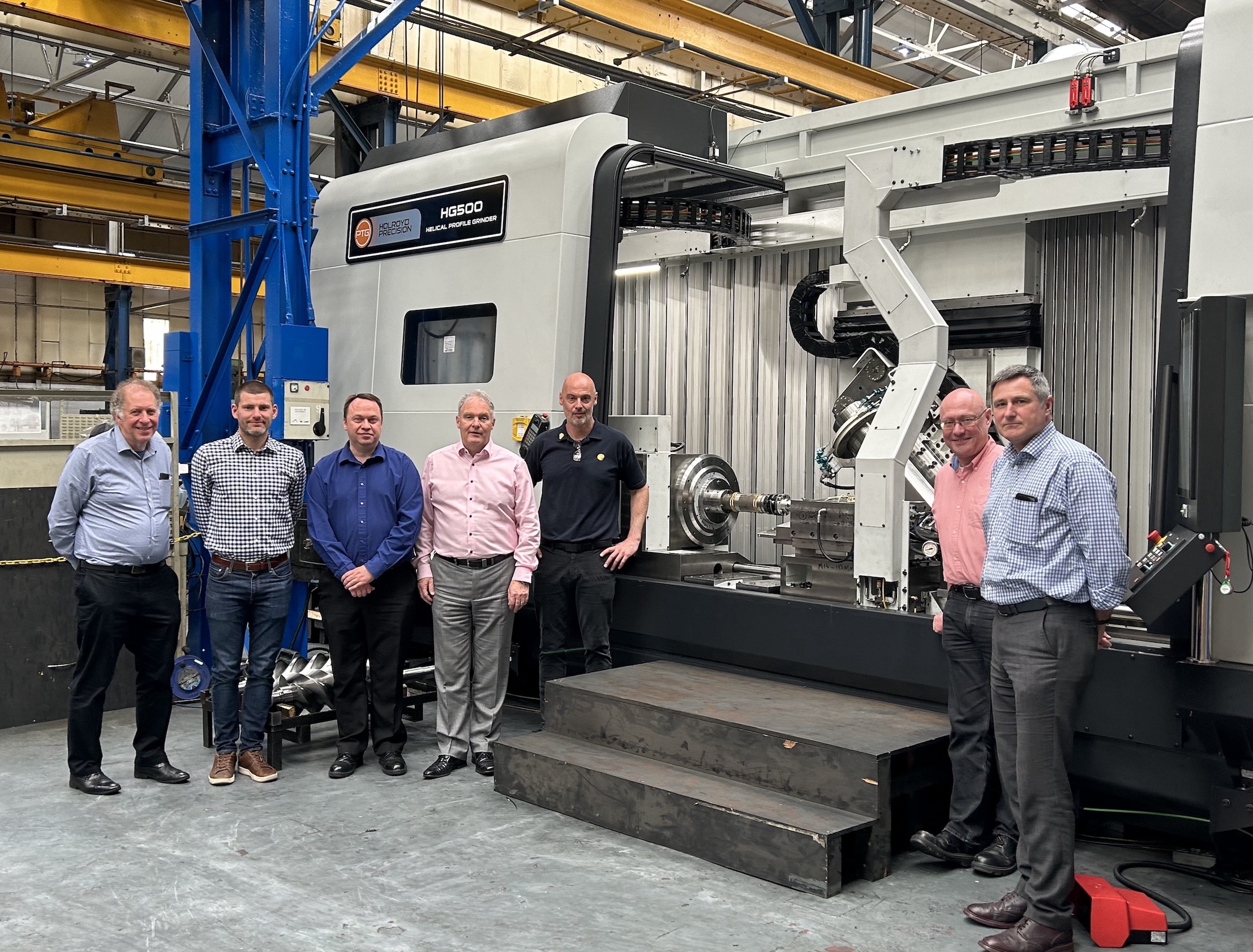
PTG Holroyd hosted an event at its Rochdale, United Kingdom, facility during which it gavew a sneak preview of its soon-to-be-launched, large-capacity HG500 ultra-high-performance helical profile grinding machine,
Held at PTG Holroyd’s Rochdale-based machine tool technology center on May 22, the company hosted the quarterly regional meeting of The Advanced Machinery & Productivity Institute (AMPI)
The event included networking opportunities and an update on the institute’s flagship industry and academic-led projects that support manufacturers in the development of world-class machine tool technologies.
More than 30 delegates commenced a tour of PTG Holroyd’s production facilities – the highlight being a demonstration of the company’s new HG500 helical rotor CNC grinding machine.
“Following the recent, highly successful launch of our smaller HG350 gear grinding center - the first UK machine tool to use Siemens Sinumetrik One future-proof CNC - we realized that a very real need also existed for a new large-capacity helical rotor grinding machine,” said PTG Holroyd’s Engineering Director, Paul Hinchliffe.
“As you can imagine, however, the challenges involved in developing two new machine tools in close succession are considerable, particularly for a UK-based manufacturer operating in the vastly competitive global sector,” he adds. “We were therefore delighted that after reviewing the impressive environmental credentials and performance capabilities of our proposed new HG500 model, AMPI agreed to help support us during the development stages of the machine. As a result, we will be able to launch the HG500 much sooner than would have otherwise been possible."
Full details of PTG Holroyd’s new HG500 ultra-high-performance CNC helical profile grinding machine will be available when the machine is officially launched later this year. Utilizing Siemens CNC system, integrated with the Holroyd Profile Management System (HPMS), the HG500 will accommodate workpieces of up to 500 mm in diameter and up to 1,500 kg in weight. Rapid setup of same component batches will be provided via the machine’s data and program files. Operating with two diamond dressing disks, the CNC-controlled dressing unit will provide automatic wheel profile calculation for each dress cycle along with programmable dressing feed rates for roughing and finishing cycles. While in-cycle profile measurement and correction will be delivered using Renishaw’s high-speed, high-accuracy OMP60 scanning probe with Sprint technology.
Related Glossary Terms
- computer numerical control ( CNC)
computer numerical control ( CNC)
Microprocessor-based controller dedicated to a machine tool that permits the creation or modification of parts. Programmed numerical control activates the machine’s servos and spindle drives and controls the various machining operations. See DNC, direct numerical control; NC, numerical control.
- dressing
dressing
Removal of undesirable materials from “loaded” grinding wheels using a single- or multi-point diamond or other tool. The process also exposes unused, sharp abrasive points. See loading; truing.
- feed
feed
Rate of change of position of the tool as a whole, relative to the workpiece while cutting.
- grinding
grinding
Machining operation in which material is removed from the workpiece by a powered abrasive wheel, stone, belt, paste, sheet, compound, slurry, etc. Takes various forms: surface grinding (creates flat and/or squared surfaces); cylindrical grinding (for external cylindrical and tapered shapes, fillets, undercuts, etc.); centerless grinding; chamfering; thread and form grinding; tool and cutter grinding; offhand grinding; lapping and polishing (grinding with extremely fine grits to create ultrasmooth surfaces); honing; and disc grinding.
- grinding machine
grinding machine
Powers a grinding wheel or other abrasive tool for the purpose of removing metal and finishing workpieces to close tolerances. Provides smooth, square, parallel and accurate workpiece surfaces. When ultrasmooth surfaces and finishes on the order of microns are required, lapping and honing machines (precision grinders that run abrasives with extremely fine, uniform grits) are used. In its “finishing” role, the grinder is perhaps the most widely used machine tool. Various styles are available: bench and pedestal grinders for sharpening lathe bits and drills; surface grinders for producing square, parallel, smooth and accurate parts; cylindrical and centerless grinders; center-hole grinders; form grinders; facemill and endmill grinders; gear-cutting grinders; jig grinders; abrasive belt (backstand, swing-frame, belt-roll) grinders; tool and cutter grinders for sharpening and resharpening cutting tools; carbide grinders; hand-held die grinders; and abrasive cutoff saws.