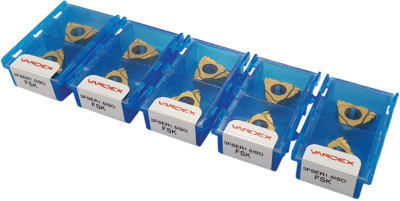
Vargus, a global leader in threading, grooving, and deburring solutions, proudly introduces the FS Line—an economical range of fully sintered inserts designed to meet the needs of diverse industries. This new line includes 62 of the most popular profiles for both external and internal threading, available in various sizes and threading standards, including ISO Metric, American UN, Whitworth, NPT, BSPT, and API Round.
Key Features and Benefits:
- Versatility: The FS Line caters to a wide range of threading standards, making it a versatile solution for multiple applications.
- Economical: Designed to be a cost-effective choice without compromising on performance, suitable for general use across different sectors.
- Durability: Available in two grades—FSK (TiN coated) for steel and general use, and FST (TiAlN coated) for stainless steel and general use, ensuring long-lasting performance.
- Compatibility: These inserts are compatible with all standard thread turning holders, enhancing their utility in various machining environments.
- Innovative Packaging: The FS Line features new 10-piece snap-off packaging for added convenience, allowing for easy handling and storage.
Advanced Tool Selection: The FS Line is now integrated into the VARGUS GENius™, the industry’s most advanced tool selector and CNC program generator, streamlining the tool selection process and optimizing CNC programming efficiency.
Contact Details
Related Glossary Terms
- computer numerical control ( CNC)
computer numerical control ( CNC)
Microprocessor-based controller dedicated to a machine tool that permits the creation or modification of parts. Programmed numerical control activates the machine’s servos and spindle drives and controls the various machining operations. See DNC, direct numerical control; NC, numerical control.
- grooving
grooving
Machining grooves and shallow channels. Example: grooving ball-bearing raceways. Typically performed by tools that are capable of light cuts at high feed rates. Imparts high-quality finish.
- threading
threading
Process of both external (e.g., thread milling) and internal (e.g., tapping, thread milling) cutting, turning and rolling of threads into particular material. Standardized specifications are available to determine the desired results of the threading process. Numerous thread-series designations are written for specific applications. Threading often is performed on a lathe. Specifications such as thread height are critical in determining the strength of the threads. The material used is taken into consideration in determining the expected results of any particular application for that threaded piece. In external threading, a calculated depth is required as well as a particular angle to the cut. To perform internal threading, the exact diameter to bore the hole is critical before threading. The threads are distinguished from one another by the amount of tolerance and/or allowance that is specified. See turning.
- turning
turning
Workpiece is held in a chuck, mounted on a face plate or secured between centers and rotated while a cutting tool, normally a single-point tool, is fed into it along its periphery or across its end or face. Takes the form of straight turning (cutting along the periphery of the workpiece); taper turning (creating a taper); step turning (turning different-size diameters on the same work); chamfering (beveling an edge or shoulder); facing (cutting on an end); turning threads (usually external but can be internal); roughing (high-volume metal removal); and finishing (final light cuts). Performed on lathes, turning centers, chucking machines, automatic screw machines and similar machines.