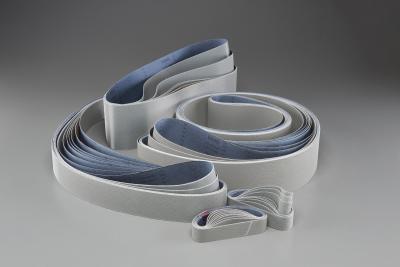
Saint-Gobain Abrasives, one of the world’s largest abrasives manufacturers, announced the introduction of its Next Generation NORaX® N889 Micro-Structured Abrasive Belts, offering a precise, flexible design for producing consistent, fine finishes across a range of industries such as medical, aerospace, automotive, marine, metal fabrication and general metalworking.
The new belts have up to 30% better performance compared with other belts in their class. This is the latest upgrade to Norton’s successful NORaX range of abrasives which also includes ceramic belts, silicon carbide belts for seaming and chamfering glass, and PSA/speed grip discs. New NORaX Belts will be highlighted at the International Manufacturing Technology Show (IMTS) Booth #N-237042 located in the Finishing/ Machining Pavilion, North Hall in McCormick Place, Chicago IL from Sept 9 - 14, 2024.
“Compared to previous generations of the NORaX belts, the new N889 belts have a high, consistent cut rate throughout the life of the abrasive belt,” said Anne Bonner, Sr. Product Manager, Norton | Saint-Gobain Abrasives. “Our new NORaX N889 belt conforms to contoured surfaces, providing a consistent finish, while reducing the number of process steps and overall cost of the finished parts.”
Norton NORaX N889 belts feature an engineered, high-performance micron-grade aluminum oxide grain structured in a fine 3D pyramid pattern which is especially well suited for lower pressure (0-8 PSI) applications where belt flexibility is needed. The engineered abrasive slowly erodes during grinding, exposing new, sharp abrasive grains resulting in 2-5X longer belt life than conventional polishing belts, as well as higher quality finishes, faster cutting rates and an ability to reduce finishing/ polishing steps. Multiple layers of abrasive grain, together with the evenly spaced pyramidal pattern, provide superior, consistent finishes on all types of materials, preventing uncontrolled scratches and producing a more repeatable, uniform finish throughout the entire part run. A flexible J-weight backing easily conforms to complex contours for superior, high-quality finishes.
New NORaX N889 belts are made-to-order in in a wide range of dimensions and are available in a variety of grit sizes including X6, X16, X22, X30, X45, X65, X80 and X100.
Contact Details
Related Glossary Terms
- abrasive
abrasive
Substance used for grinding, honing, lapping, superfinishing and polishing. Examples include garnet, emery, corundum, silicon carbide, cubic boron nitride and diamond in various grit sizes.
- abrasive belt
abrasive belt
Abrasive-coated belt used for production finishing, deburring and similar functions. See coated abrasive.
- aluminum oxide
aluminum oxide
Aluminum oxide, also known as corundum, is used in grinding wheels. The chemical formula is Al2O3. Aluminum oxide is the base for ceramics, which are used in cutting tools for high-speed machining with light chip removal. Aluminum oxide is widely used as coating material applied to carbide substrates by chemical vapor deposition. Coated carbide inserts with Al2O3 layers withstand high cutting speeds, as well as abrasive and crater wear.
- backing
backing
1. Flexible portion of a bandsaw blade. 2. Support material behind the cutting edge of a tool. 3. Base material for coated abrasives.
- chamfering
chamfering
Machining a bevel on a workpiece or tool; improves a tool’s entrance into the cut.
- grinding
grinding
Machining operation in which material is removed from the workpiece by a powered abrasive wheel, stone, belt, paste, sheet, compound, slurry, etc. Takes various forms: surface grinding (creates flat and/or squared surfaces); cylindrical grinding (for external cylindrical and tapered shapes, fillets, undercuts, etc.); centerless grinding; chamfering; thread and form grinding; tool and cutter grinding; offhand grinding; lapping and polishing (grinding with extremely fine grits to create ultrasmooth surfaces); honing; and disc grinding.
- metalworking
metalworking
Any manufacturing process in which metal is processed or machined such that the workpiece is given a new shape. Broadly defined, the term includes processes such as design and layout, heat-treating, material handling and inspection.
- polishing
polishing
Abrasive process that improves surface finish and blends contours. Abrasive particles attached to a flexible backing abrade the workpiece.