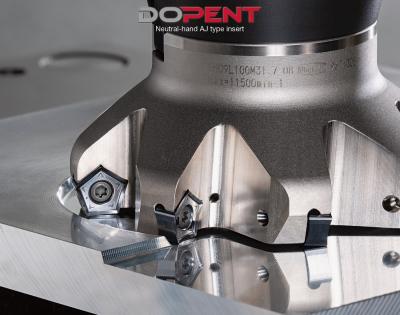
Tungaloy Corporation (President: Satoshi Kinoshita, Headquarters: Iwaki, Fukushima) announces the expansion of its "DoPent" face milling cutter series with the addition of Neutral "AJ Type" inserts for non-ferrous metal machining.
Overview
The "DoPent" series features economical double-sided pentagonal inserts with 10 cutting edges, designed for face milling operations. "DoPent" offers significant reductions in cutting force (by 30%) and radial forces (by 50%) compared to competitors, thanks to its large rake angle and optimal insert positioning. This makes it especially suitable for machining thin and low-rigidity workpieces. The series also includes the "SS-FiT" mechanism, which increases rigidity and allows for more number of insert on the cutter body without compromising body rigidity, enabling high-efficiency machining.
Cutter bodies are available in both bore and shank types, with tool diameters ranging from φ32 to φ315 mm (from φ1.260” to φ12.40”), including left-hand body options for use in double-headed milling machines. The insert lineup includes six types: the general-purpose "MJ Type", low cutting force "ML Type", and wiper inserts. Neutral inserts are also available for use with left-hand cutter bodies.
The new Neutral "AJ Type" inserts for non-ferrous metals join this lineup. Like their right-hand counterparts, these new inserts feature ground peripheral surface and polished rake face with a mirror-like finish for sharp cutting edges. This prevents the built-up edges to the cutting edge during machining, and achieving a high-quality, glossy finish. The large rake angle and deep inclination ensure excellent chip control with both right-hand and left-hand cutter bodies. The insert grade is "KS05F", a micro-grain cemented carbide that balances wear resistance and toughness, providing exceptional reliability and long tool life for machining aluminum, copper alloys, and other non-ferrous metals.
With the addition of the new "AJ Type" inserts, the "DoPent" series will significantly reduce machining costs and improve productivity for customers across various industries, handling a wide range of materials from steel and cast iron to non-ferrous metals.
Contact Details
Related Glossary Terms
- alloys
alloys
Substances having metallic properties and being composed of two or more chemical elements of which at least one is a metal.
- copper alloys
copper alloys
Copper containing specified quantities of alloying elements added to obtain the necessary mechanical and physical properties. The most common copper alloys are divided into six groups, and each group contains one of the following major alloying elements: brasses—major alloying element is zinc; phosphor bronzes—major alloying element is tin; aluminum bronzes—major alloying element is aluminum; silicon bronzes—major alloying element is silicon; copper-nickels and nickel-silvers—major alloying element is nickel; and dilute-copper or high-copper alloys, which contain small amounts of various elements such as beryllium, cadmium, chromium or iron.
- cutting force
cutting force
Engagement of a tool’s cutting edge with a workpiece generates a cutting force. Such a cutting force combines tangential, feed and radial forces, which can be measured by a dynamometer. Of the three cutting force components, tangential force is the greatest. Tangential force generates torque and accounts for more than 95 percent of the machining power. See dynamometer.
- gang cutting ( milling)
gang cutting ( milling)
Machining with several cutters mounted on a single arbor, generally for simultaneous cutting.
- milling
milling
Machining operation in which metal or other material is removed by applying power to a rotating cutter. In vertical milling, the cutting tool is mounted vertically on the spindle. In horizontal milling, the cutting tool is mounted horizontally, either directly on the spindle or on an arbor. Horizontal milling is further broken down into conventional milling, where the cutter rotates opposite the direction of feed, or “up” into the workpiece; and climb milling, where the cutter rotates in the direction of feed, or “down” into the workpiece. Milling operations include plane or surface milling, endmilling, facemilling, angle milling, form milling and profiling.
- milling cutter
milling cutter
Loosely, any milling tool. Horizontal cutters take the form of plain milling cutters, plain spiral-tooth cutters, helical cutters, side-milling cutters, staggered-tooth side-milling cutters, facemilling cutters, angular cutters, double-angle cutters, convex and concave form-milling cutters, straddle-sprocket cutters, spur-gear cutters, corner-rounding cutters and slitting saws. Vertical cutters use shank-mounted cutting tools, including endmills, T-slot cutters, Woodruff keyseat cutters and dovetail cutters; these may also be used on horizontal mills. See milling.
- rake
rake
Angle of inclination between the face of the cutting tool and the workpiece. If the face of the tool lies in a plane through the axis of the workpiece, the tool is said to have a neutral, or zero, rake. If the inclination of the tool face makes the cutting edge more acute than when the rake angle is zero, the rake is positive. If the inclination of the tool face makes the cutting edge less acute or more blunt than when the rake angle is zero, the rake is negative.
- shank
shank
Main body of a tool; the portion of a drill or similar end-held tool that fits into a collet, chuck or similar mounting device.
- wear resistance
wear resistance
Ability of the tool to withstand stresses that cause it to wear during cutting; an attribute linked to alloy composition, base material, thermal conditions, type of tooling and operation and other variables.
- wiper
wiper
Metal-removing edge on the face of a cutter that travels in a plane perpendicular to the axis. It is the edge that sweeps the machined surface. The flat should be as wide as the feed per revolution of the cutter. This allows any given insert to wipe the entire workpiece surface and impart a fine surface finish at a high feed rate.