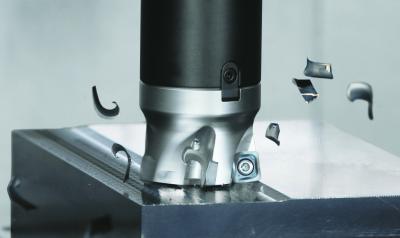
Kyocera introduces the PR18 Series, an innovative lineup of indexable milling inserts meticulously crafted to elevate the user’s machining experience across Kyocera’s most popular milling lines.
At the core of this series lies Kyocera’s all new, next-generation PVD coating technology. Designed to propel production runs forward, this groundbreaking coating takes milling performance to new heights. With PR18 Series inserts, machinists can eliminate frequent tool replacements and costly downtime, as Kyocera’s cutting-edge coating brings an unmatched level of longevity to milling operations in a large variety of workpiece materials.
The PR18 Series incorporates proprietary MEGACOAT NANO EX coating technology, setting a new standard for wear resistance and durability. By using a unique double lamination technique with special nano multi- layers for abrasion, wear, and heat resistance, this coating surpasses conventional grades, delivering superior performance and extending the lifespan of the tools.
The key to the PR18 Series' success lies in its ability to protect against wear and abrasion like no other. With excellent oxidation resistance and a higher coating toughness, PR18 suppresses crack growth and remains tougher longer. This results in prolonged tool life, reducing the need for frequent tool changes in the middle of your production runs. With enhanced wear resistance and durability, milling operations can be extended longer while maintaining precision and surface finish, ultimately improving productivity and efficiency.
Benefits:
-
Kyocera's nano layer coating technology provides increased tool life
-
Superior abrasion, fracture, heat, and oxidation resistance
-
Extended milling operations eliminating frequent insert
changes/indexing
-
Excellent durability
Features:
-
Proprietary MEGACOAT NANO EX multi-layer structure with two unique nano layers
-
AlCr-based coating layer with excellent abrasion resistance
-
AlTi-based coating layer with excellent heat resistance
-
PR18 grades available across more than 16 popular milling series cutter lines
-
Multiple cutting edges per insert
Applications:
-
PR1825 – Recommended for Steel (wear resistance oriented)
-
PR1835 – Recommended for Stainless Steel and steel (stability oriented)
-
PR1810 – Recommended for Cast Iron
-
Compatible cutter series include various milling operations (facing, slotting, ramping, helical milling,
shouldering, etc.)
Contact Details
Related Glossary Terms
- gang cutting ( milling)
gang cutting ( milling)
Machining with several cutters mounted on a single arbor, generally for simultaneous cutting.
- milling
milling
Machining operation in which metal or other material is removed by applying power to a rotating cutter. In vertical milling, the cutting tool is mounted vertically on the spindle. In horizontal milling, the cutting tool is mounted horizontally, either directly on the spindle or on an arbor. Horizontal milling is further broken down into conventional milling, where the cutter rotates opposite the direction of feed, or “up” into the workpiece; and climb milling, where the cutter rotates in the direction of feed, or “down” into the workpiece. Milling operations include plane or surface milling, endmilling, facemilling, angle milling, form milling and profiling.
- physical vapor deposition ( PVD)
physical vapor deposition ( PVD)
Tool-coating process performed at low temperature (500° C), compared to chemical vapor deposition (1,000° C). Employs electric field to generate necessary heat for depositing coating on a tool’s surface. See CVD, chemical vapor deposition.
- slotting
slotting
Machining, normally milling, that creates slots, grooves and similar recesses in workpieces, including T-slots and dovetails.
- wear resistance
wear resistance
Ability of the tool to withstand stresses that cause it to wear during cutting; an attribute linked to alloy composition, base material, thermal conditions, type of tooling and operation and other variables.