Much like professional hockey with its power, speed, and grace, so too were some of technologies, techniques, and even milled items showcased at the OPEN MIND Technologies booth at IMTS 2024.
Among the draws of this busy booth was a hockey theme that showed how its hyperMILL software technology can help manufacturers produce perfect finishes such as a brilliantly finished ice skate on display. The theme continued with a hockey stick and goalie mask. The difference, of course, was that these hockey tools were made of metals.
"[The] skate is completed, finished and machined," said Alan Levine, managing director at OPEN MIND Technologies, "with perfect surfaces and blends using hyperMILL's smooth overlap, and point-spacing techniques, it is just a beautiful object."
OPEN MIND Technologies is one of the world’s leading developers of
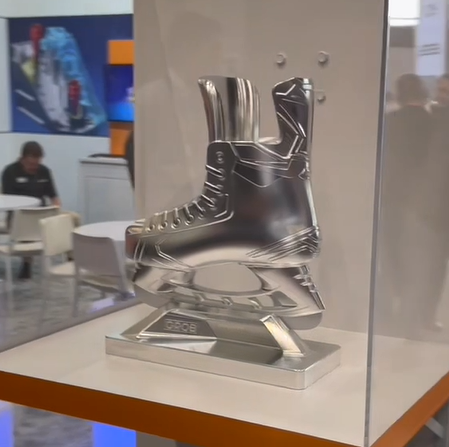
CAD/CAM solutions for machine and controller-independent programming. The Germany-based company with U.S. headquarter near Boston, develops optimized CAD/CAM solutions that Levine said can deliver significantly higher performance.
At the show, Levine said that the company was showcasing its latest iteration, the hyperMill 2024 CAD/CAM software suite version that features range of enhancements to its core toolpath capabilities, as well as custom functionality for increased NC programming efficiency in applications ranging from 2.5D machining to five-axis milling.
"Some of our newer techniques," said Levine, in a Cutting Tool Engineering video produced at the booth, "focus on high surface finish. The idea here is that we're recognizing very specific geometry topology from the part, and moving the specific machining points to align with the details in geometry. What comes out of that at the machine control is perfect surface finish and much less work for the machine control."
Enhanced CAM capabilities
Among the new features and strategies of hyperMILL 2024, is an optimized deep hole drilling CAM strategy that offers improved machining reliability by providing a user-friendly interface with process-relevant parameters clearly defined on a new process tab.
According to the company, new capabilities enable coolant and dwell time stages to be identified, and allow a chip break to be integrated into a drilling process. A new single-tip gun drill tool simulation function provides precise collision checking and a detailed visualization of the stock removal.
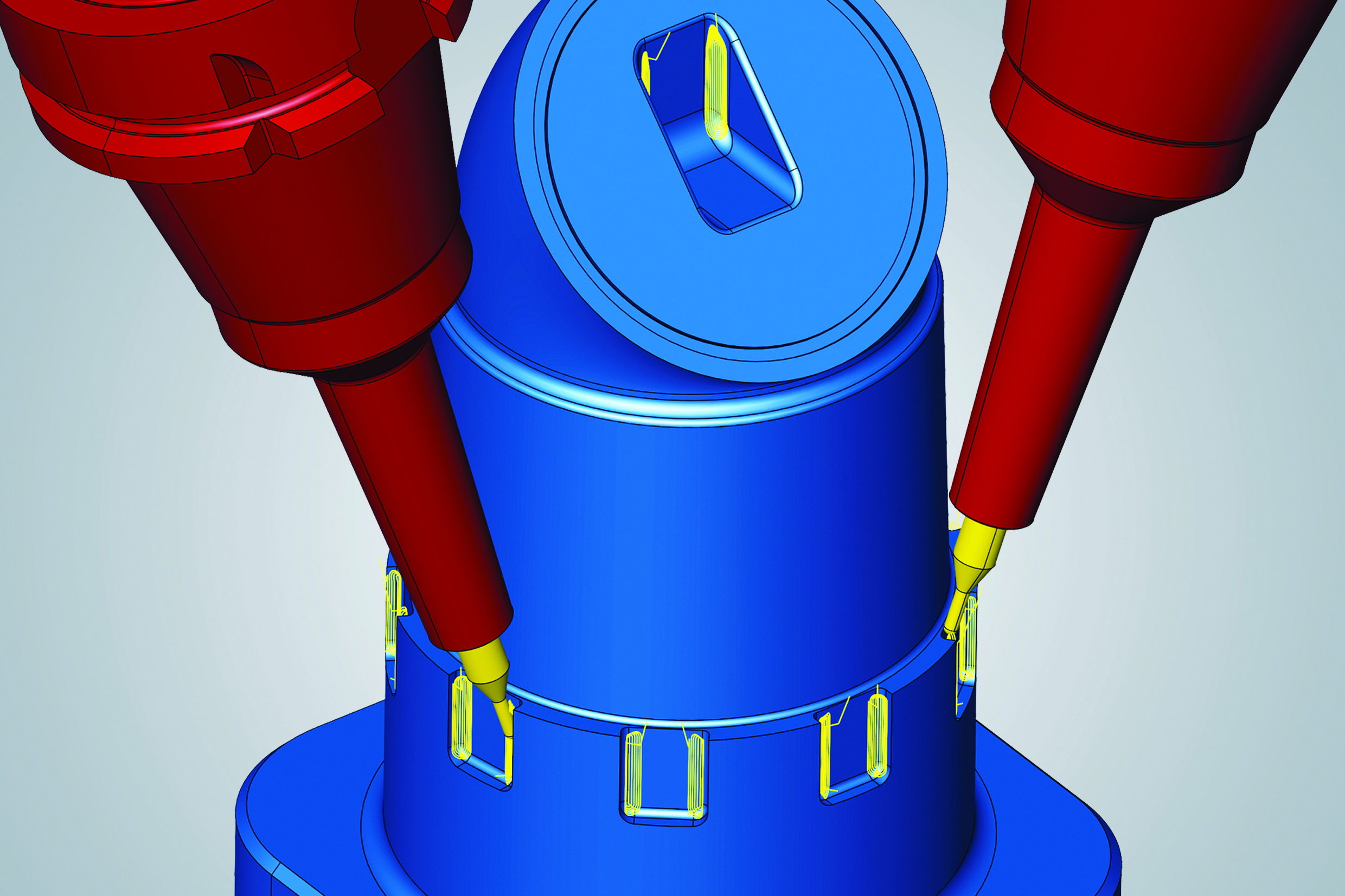
In addition, a new algorithm for 3-axis and 5-axis Rest Machining (see picture above) helps ensure automatic, complete detection of all rest material areas, and optimized toolpath calculations for faster, reliable machining. Toolpaths are now optimally divided to ensure more efficient machining, and the detection of intersection areas where paths meet has been optimized for collision avoidance, the company said.
An additional toolpath improvement is an enhanced path layout for the 3D Plane Machining cycle. The new strategy has a smoother path and fewer pick-ups. While the toolpath length (distance) may be longer in some cases, the machining time, as tested on a variety of NC controllers, has been reduced.
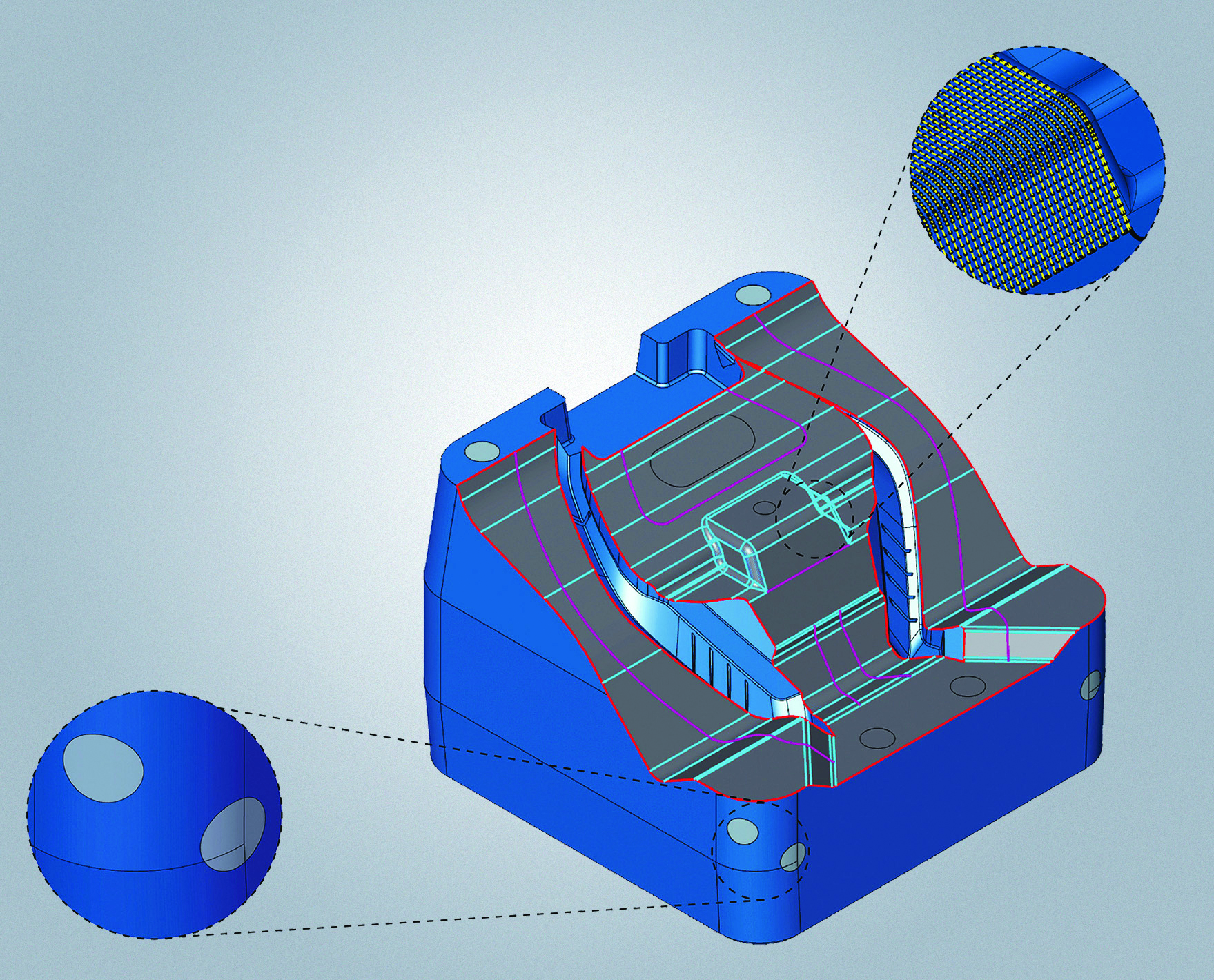
Once the data is organized, the CAM workflow can be processed with more intelligence and higher efficiency. The first benefit from hyperMILL CAM Plan is that component topology is analyzed to produce a precise toolpath that has command locations aligned with key geometric features and with optimized point distribution for milling. The result is improved surface finishes, easier processing by NC controllers, and reduced machining times.
Virtual machining
While CAD/CAM is the company's core product, well known in the five-axis machining world, a highlight of the booth visit with Cutting Tool Engineering editor's is the company's virtual machining technology that Levine said includes a G-code simulator that ensures code is approved before execution and an NC optimizer for efficient post-processing.
According to the company, easy generation of 3-axis and 5-axis NC programs is achievable with axis change and optimized use of the workspace. The NC Optimizer feature in the hyperMILL VIRTUAL Machining strategy offers the option to transform X- and Y-axis movements into a movement that utilizes the rotation axis in the table.
By swapping axes, an XY movement is transformed into a simultaneous CX movement which eliminates rewind movements during machining. This is especially impactful on machines that have a limited linear axis range.
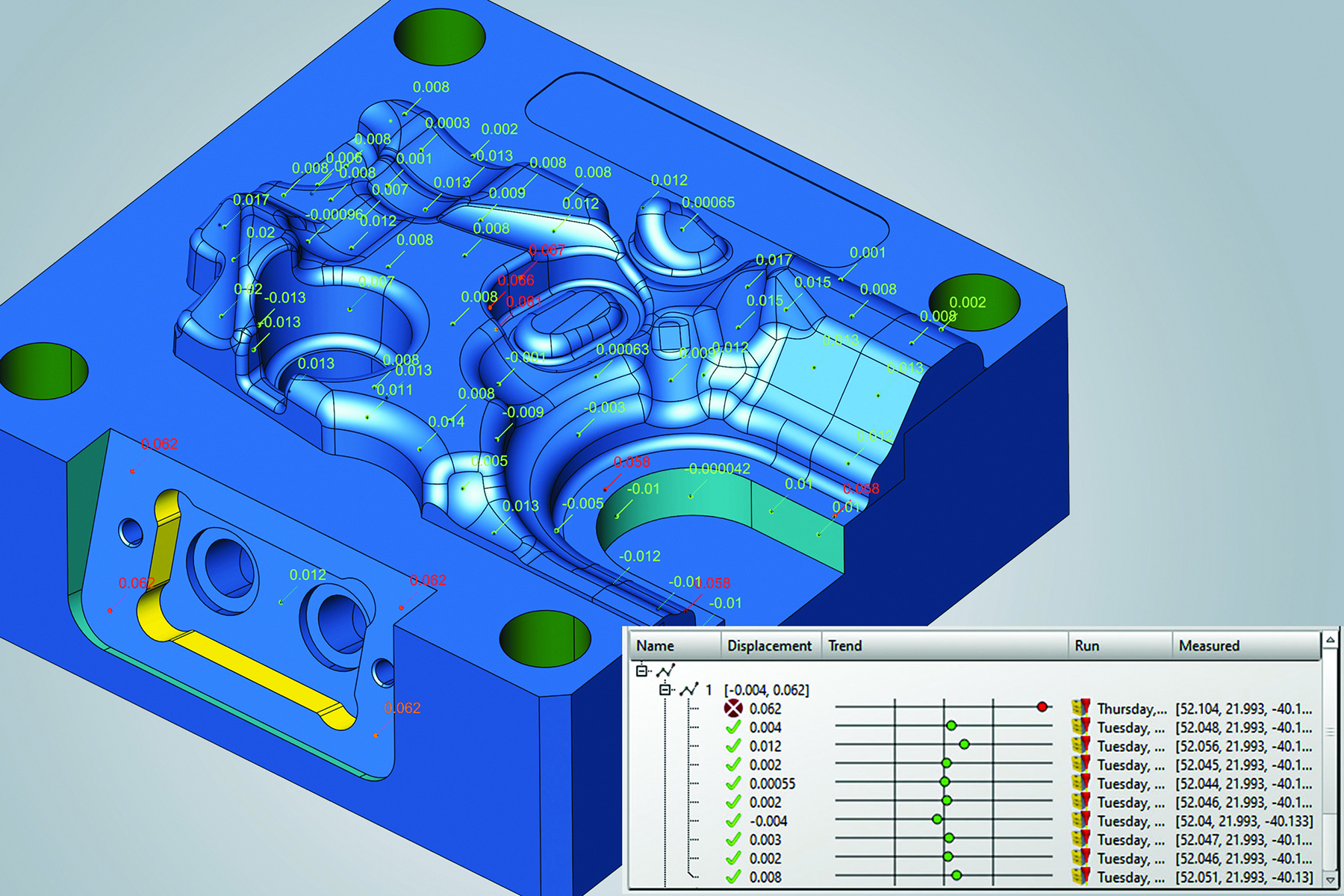
Another virtual machining features is reading back of measuring points that allows graphical representation of measured points on the part model, rather than comparing a list of measurement results.
The company says that users can quickly identify measuring points that are out of tolerance on a 3D part model and compare trends over sequential measurements. As a result, it is much easier to analyze and compensate for inaccuracies and tool wear after milling.
Contact Details
Related Glossary Terms
- computer-aided manufacturing ( CAM)
computer-aided manufacturing ( CAM)
Use of computers to control machining and manufacturing processes.
- coolant
coolant
Fluid that reduces temperature buildup at the tool/workpiece interface during machining. Normally takes the form of a liquid such as soluble or chemical mixtures (semisynthetic, synthetic) but can be pressurized air or other gas. Because of water’s ability to absorb great quantities of heat, it is widely used as a coolant and vehicle for various cutting compounds, with the water-to-compound ratio varying with the machining task. See cutting fluid; semisynthetic cutting fluid; soluble-oil cutting fluid; synthetic cutting fluid.
- gang cutting ( milling)
gang cutting ( milling)
Machining with several cutters mounted on a single arbor, generally for simultaneous cutting.
- milling
milling
Machining operation in which metal or other material is removed by applying power to a rotating cutter. In vertical milling, the cutting tool is mounted vertically on the spindle. In horizontal milling, the cutting tool is mounted horizontally, either directly on the spindle or on an arbor. Horizontal milling is further broken down into conventional milling, where the cutter rotates opposite the direction of feed, or “up” into the workpiece; and climb milling, where the cutter rotates in the direction of feed, or “down” into the workpiece. Milling operations include plane or surface milling, endmilling, facemilling, angle milling, form milling and profiling.
- numerical control ( NC)
numerical control ( NC)
Any controlled equipment that allows an operator to program its movement by entering a series of coded numbers and symbols. See CNC, computer numerical control; DNC, direct numerical control.
- tolerance
tolerance
Minimum and maximum amount a workpiece dimension is allowed to vary from a set standard and still be acceptable.
- toolpath( cutter path)
toolpath( cutter path)
2-D or 3-D path generated by program code or a CAM system and followed by tool when machining a part.