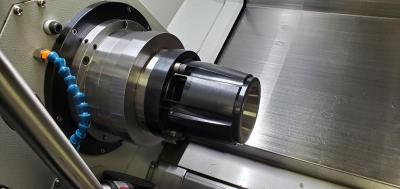
Zagar Inc. increases design and engineering services for customers otherwise seeking custom workholding for lathe operations. Zagar 22c CNC collet chucks are offered along with standard collets that are modified to mate exactly with unique die cast part configurations. These parts can be held securely on either ID or OD surfaces, providing increased machining access.
One CNC collet chuck holds each modified collet. Working together with a draw-bar spindle and coupling with the back of the collet chuck, the clamp mechanism is actuated inside to securely locate and hold the part in a single step. The setup helps to ensure machining performance while providing very low runout as well as quick changeover to keep machine uptime high.
CNC collet chucks and collets are an alternative to pneumatic or hydraulic workholding devices and are well-suited for high production runs. Standard shapes such as round, square and hexes can be held accurately and quickly compared to a three or four jaw chuck.
“Through design and engineering, we can help customers with virtually any special need”, says Brian Zagar, vice president of sales for Zagar Inc. “And often times the solution is simpler than you’d expect, with measurable reduction in man hours and increases in machine utilization”, Zagar continued.
Contact Details
Related Glossary Terms
- chuck
chuck
Workholding device that affixes to a mill, lathe or drill-press spindle. It holds a tool or workpiece by one end, allowing it to be rotated. May also be fitted to the machine table to hold a workpiece. Two or more adjustable jaws actually hold the tool or part. May be actuated manually, pneumatically, hydraulically or electrically. See collet.
- collet
collet
Flexible-sided device that secures a tool or workpiece. Similar in function to a chuck, but can accommodate only a narrow size range. Typically provides greater gripping force and precision than a chuck. See chuck.
- computer numerical control ( CNC)
computer numerical control ( CNC)
Microprocessor-based controller dedicated to a machine tool that permits the creation or modification of parts. Programmed numerical control activates the machine’s servos and spindle drives and controls the various machining operations. See DNC, direct numerical control; NC, numerical control.
- inner diameter ( ID)
inner diameter ( ID)
Dimension that defines the inside diameter of a cavity or hole. See OD, outer diameter.
- lathe
lathe
Turning machine capable of sawing, milling, grinding, gear-cutting, drilling, reaming, boring, threading, facing, chamfering, grooving, knurling, spinning, parting, necking, taper-cutting, and cam- and eccentric-cutting, as well as step- and straight-turning. Comes in a variety of forms, ranging from manual to semiautomatic to fully automatic, with major types being engine lathes, turning and contouring lathes, turret lathes and numerical-control lathes. The engine lathe consists of a headstock and spindle, tailstock, bed, carriage (complete with apron) and cross slides. Features include gear- (speed) and feed-selector levers, toolpost, compound rest, lead screw and reversing lead screw, threading dial and rapid-traverse lever. Special lathe types include through-the-spindle, camshaft and crankshaft, brake drum and rotor, spinning and gun-barrel machines. Toolroom and bench lathes are used for precision work; the former for tool-and-die work and similar tasks, the latter for small workpieces (instruments, watches), normally without a power feed. Models are typically designated according to their “swing,” or the largest-diameter workpiece that can be rotated; bed length, or the distance between centers; and horsepower generated. See turning machine.
- outer diameter ( OD)
outer diameter ( OD)
Dimension that defines the exterior diameter of a cylindrical or round part. See ID, inner diameter.