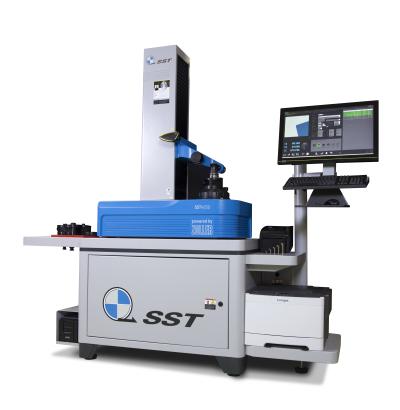
SST introduces the SST 4200 tool presetter for boosting efficiency and profitability in high-precision part manufacturing. Built and designed to exacting specifications, the SST 4200 equips shops with improved precision through tool measurement accuracy of ±0.003mm (0.00012 inches), and user-friendly features that help eliminate human error.
“Working with Zoller, we’ve engineered and specified a tool presetter that gives precision part manufacturers a significant competitive edge,” said Darrell Johnson, product manager of milling consumables at SST. “The SST 4200 provides ideal accuracy and reliability for uninterrupted production within high-precision markets, such as aerospace, precision production machining and mold-shop environments. By streamlining shop-floor efficiency and eliminating human error, the device helps minimize machine downtime and increase process stability for lower costs, shorter delivery times and improved quality.”
Constructed from heavy-duty aircraft aluminum, the SST 4200 reduces errors caused by thermal expansion. Its spindle features actuated clamping of tool holders, similar to that of a machine tool, providing optimal measurement accuracy with spindle concentricity of 0.002mm (0.000079").
Designed with superior image processing and dynamic cross-hair technologies, the SST 4200 captures and measures critical features of the tool cutting edge in the micron range. Its fully automatic X, Z and C axes and an auto-focusing camera enable fast measurement, setting and testing that help eliminate human error. Additionally, an intuitive touch-screen CNC boasts several user-friendly features that require minimal training and provide easy access to tool data, photographs, drawings and 3D images via a scalable tool management system.
To facilitate tool traceability within shop environments, the SST 4200 has a standard thermo-label printer and can be equipped with an optional RFID system. The device is capable of interfacing with other tool data management systems to track tooling across systems and processes, allowing robots, machines and other equipment to read and write stored data for more reliable, versatile and efficient unattended processing of high-precision components.
Contact Details
Related Glossary Terms
- computer numerical control ( CNC)
computer numerical control ( CNC)
Microprocessor-based controller dedicated to a machine tool that permits the creation or modification of parts. Programmed numerical control activates the machine’s servos and spindle drives and controls the various machining operations. See DNC, direct numerical control; NC, numerical control.
- gang cutting ( milling)
gang cutting ( milling)
Machining with several cutters mounted on a single arbor, generally for simultaneous cutting.
- micron
micron
Measure of length that is equal to one-millionth of a meter.
- milling
milling
Machining operation in which metal or other material is removed by applying power to a rotating cutter. In vertical milling, the cutting tool is mounted vertically on the spindle. In horizontal milling, the cutting tool is mounted horizontally, either directly on the spindle or on an arbor. Horizontal milling is further broken down into conventional milling, where the cutter rotates opposite the direction of feed, or “up” into the workpiece; and climb milling, where the cutter rotates in the direction of feed, or “down” into the workpiece. Milling operations include plane or surface milling, endmilling, facemilling, angle milling, form milling and profiling.