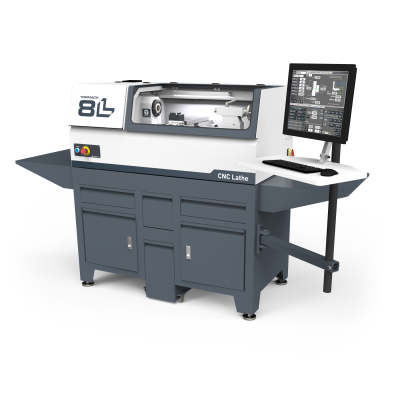
Tormach Inc., the industry’s leading supplier of affordable and compact CNC machines, has announced its newest machine, the 8L Lathe.
This new 8L Lathe is a small machine with big capabilities, and has the ability to fill turning needs in a variety of spaces. Rigid enough to cut anything, whether it’s plastic, stainless steel even titanium, this machine can handle it, and at an approachable price point. Starting at $6,595 for the basic machine with tailstock and fully-assembled enclosure, an 8L Lathe Deluxe Package with numerous features including a robust machine stand with integral coolant tank, separate chip drawer for easy removal, storage drawers and optional side shelving, as well as PathPilot controller, tool holder/tool kit, monitor, keyboard, mouse, and more is available for only $8,875. And the fully-loaded 8L build comes in under $10K.
“We are excited to introduce this new lathe to the market,” said Cory Bailey, Tormach’s Product Engineer. “Tormach was founded on the idea of bringing cost-effective and capable CNC equipment to market and this one provides users with everything needed to face, turn, bore, groove and thread. We know of no other machine that offers such advanced software and capabilities at such an affordable price.”
The 8L lathe features a 5C spindle that accommodates parts up to 1” diameter, which meets the needs of most lathe users. For larger pieces up to 8” in diameter, users can simply add a 3- or 4-jaw chuck to cut the stock.
Like all Tormach CNC machines, the 8L lathe will be controlled by the PathPilot software system. That means users can use intuitive conversational lathe programming, do rigid tapping, and leverage built-in Dropbox™ support for transferring programs. PathPilot and PathPilot HUB has been known to be incredibly powerful for both beginner CNCers, as well as veteran machinists and educators.
Specifications
The new 8L is unique, not just among other Tormach machines, but also in the general machine tool market, because it offers a 1.5 HP (1.11 kW) spindle that runs at 180-5000 RPM. It already comes with the machine in a fully assembled enclosure as part of the base model, but the footprint remains small (26in. x 50 in.), and the lathe itself is attached to a hand-scraped 140-pound cast base. Like all Tormach machine tools, the 8L runs on standard single-phase household power (115 Vac, 50/60 Hz, and a 15 A breaker).
With a 5C spindle, the 8L can accommodate parts up to 1 in. or use a 3- or 4-jaw chuck, providing a swing of up to 8”. And, the stepper motors on the X and Z axes provide a feed rate of 150 IPM (3.8 m/min).
Travels on the 8L are impressive for its compact size. The maximum workpiece length is 10” with the tailstock. The X-axis travel is 4.5”, so users can accommodate a part that fully utilizes the 8” swing.
It’s configured for Industry Standard OXA Quick Change Tool Post. Instead of the operator needing two wrenches that turn hardware in opposite directions, the machine itself can lock down the tool holder. By allowing ‘one hand tool changing’, this takes a typically inconvenient task and not only makes it easier, but also greatly reduces the time required to change the tooling.
Contact Details
Related Glossary Terms
- chuck
chuck
Workholding device that affixes to a mill, lathe or drill-press spindle. It holds a tool or workpiece by one end, allowing it to be rotated. May also be fitted to the machine table to hold a workpiece. Two or more adjustable jaws actually hold the tool or part. May be actuated manually, pneumatically, hydraulically or electrically. See collet.
- computer numerical control ( CNC)
computer numerical control ( CNC)
Microprocessor-based controller dedicated to a machine tool that permits the creation or modification of parts. Programmed numerical control activates the machine’s servos and spindle drives and controls the various machining operations. See DNC, direct numerical control; NC, numerical control.
- coolant
coolant
Fluid that reduces temperature buildup at the tool/workpiece interface during machining. Normally takes the form of a liquid such as soluble or chemical mixtures (semisynthetic, synthetic) but can be pressurized air or other gas. Because of water’s ability to absorb great quantities of heat, it is widely used as a coolant and vehicle for various cutting compounds, with the water-to-compound ratio varying with the machining task. See cutting fluid; semisynthetic cutting fluid; soluble-oil cutting fluid; synthetic cutting fluid.
- feed
feed
Rate of change of position of the tool as a whole, relative to the workpiece while cutting.
- inches per minute ( ipm)
inches per minute ( ipm)
Value that refers to how far the workpiece or cutter advances linearly in 1 minute, defined as: ipm = ipt 5 number of effective teeth 5 rpm. Also known as the table feed or machine feed.
- lathe
lathe
Turning machine capable of sawing, milling, grinding, gear-cutting, drilling, reaming, boring, threading, facing, chamfering, grooving, knurling, spinning, parting, necking, taper-cutting, and cam- and eccentric-cutting, as well as step- and straight-turning. Comes in a variety of forms, ranging from manual to semiautomatic to fully automatic, with major types being engine lathes, turning and contouring lathes, turret lathes and numerical-control lathes. The engine lathe consists of a headstock and spindle, tailstock, bed, carriage (complete with apron) and cross slides. Features include gear- (speed) and feed-selector levers, toolpost, compound rest, lead screw and reversing lead screw, threading dial and rapid-traverse lever. Special lathe types include through-the-spindle, camshaft and crankshaft, brake drum and rotor, spinning and gun-barrel machines. Toolroom and bench lathes are used for precision work; the former for tool-and-die work and similar tasks, the latter for small workpieces (instruments, watches), normally without a power feed. Models are typically designated according to their “swing,” or the largest-diameter workpiece that can be rotated; bed length, or the distance between centers; and horsepower generated. See turning machine.
- tapping
tapping
Machining operation in which a tap, with teeth on its periphery, cuts internal threads in a predrilled hole having a smaller diameter than the tap diameter. Threads are formed by a combined rotary and axial-relative motion between tap and workpiece. See tap.
- turning
turning
Workpiece is held in a chuck, mounted on a face plate or secured between centers and rotated while a cutting tool, normally a single-point tool, is fed into it along its periphery or across its end or face. Takes the form of straight turning (cutting along the periphery of the workpiece); taper turning (creating a taper); step turning (turning different-size diameters on the same work); chamfering (beveling an edge or shoulder); facing (cutting on an end); turning threads (usually external but can be internal); roughing (high-volume metal removal); and finishing (final light cuts). Performed on lathes, turning centers, chucking machines, automatic screw machines and similar machines.