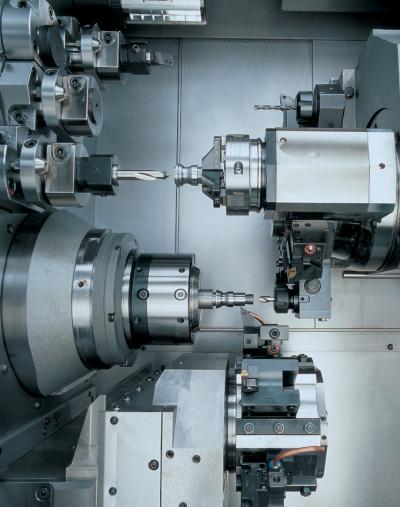
The dynamic new generation of the ABC machine from INDEX is ideal for turning out simple to moderately complex parts in cycle times up to 15% faster than the previous generation with rapid spindle acceleration (8 g), shorter spindle ramp-up times, higher rapid traverse rates, and quick chip to chip times, according to the company. Ideal for runs from 5,000 to 50,000 parts in the 42 to 60 mm range, the machine’s combination of features supports a low production cost per piece, even for complex parts. Up to 19 tools are available for highly flexible machining with live tools for both turrets.
Extremely short cycle times are achievable due to simultaneous machining with up to three tools. The ABC is equipped with up to five driven back-working tools and offers driven tools in all turret positions. The machine is available in 2-, 3- or 4-axis versions. The motorized 27-kW, 6000-rpm spindle, can generate up to 95Nm of torque.
Within the easy-access work area, mounted above the main spindle, is the upper turret used mainly for ID work. The lower turret is typically for OD work. A synchronized spindle operates in the upper turret. Both turrets feature a rapid traverse of 36 m/min.
The ABC can handle heavy-duty polygon turning and thread milling with a counterspindle or drive attachment. The ABC can also be supplied with a quiet-running Index bar loader which can save 4 to 30 seconds per cycle, and automatic part unloader automation.
Siemens S840D sl control offers economic and productive solutions. The operating system with the INDEXC200-4D CNC is equipped with the INDEX Xpanel i4.0 and 18.5” touch screen.
Xpanel creates the conditions for the use of INDUSTRY 4.0: the INDEX operating system focuses on the optimal control of the machine for the effective machining of workpieces with maximum productivity. It provides a direct connection between the machine control and the operations department within the user company. The operator receives exactly the information that best supports him in his current work.
Xpanel offers extensive user assistance through complete integration into existing network structures. Drawings, setup sheets, user manuals, circuit and hydraulic diagrams, and more are available directly on the machine without additional hardware.
Contact Details
Related Glossary Terms
- computer numerical control ( CNC)
computer numerical control ( CNC)
Microprocessor-based controller dedicated to a machine tool that permits the creation or modification of parts. Programmed numerical control activates the machine’s servos and spindle drives and controls the various machining operations. See DNC, direct numerical control; NC, numerical control.
- gang cutting ( milling)
gang cutting ( milling)
Machining with several cutters mounted on a single arbor, generally for simultaneous cutting.
- inner diameter ( ID)
inner diameter ( ID)
Dimension that defines the inside diameter of a cavity or hole. See OD, outer diameter.
- milling
milling
Machining operation in which metal or other material is removed by applying power to a rotating cutter. In vertical milling, the cutting tool is mounted vertically on the spindle. In horizontal milling, the cutting tool is mounted horizontally, either directly on the spindle or on an arbor. Horizontal milling is further broken down into conventional milling, where the cutter rotates opposite the direction of feed, or “up” into the workpiece; and climb milling, where the cutter rotates in the direction of feed, or “down” into the workpiece. Milling operations include plane or surface milling, endmilling, facemilling, angle milling, form milling and profiling.
- outer diameter ( OD)
outer diameter ( OD)
Dimension that defines the exterior diameter of a cylindrical or round part. See ID, inner diameter.
- rapid traverse
rapid traverse
Movement on a CNC mill or lathe that is from point to point at full speed but, usually, without linear interpolation.
- turning
turning
Workpiece is held in a chuck, mounted on a face plate or secured between centers and rotated while a cutting tool, normally a single-point tool, is fed into it along its periphery or across its end or face. Takes the form of straight turning (cutting along the periphery of the workpiece); taper turning (creating a taper); step turning (turning different-size diameters on the same work); chamfering (beveling an edge or shoulder); facing (cutting on an end); turning threads (usually external but can be internal); roughing (high-volume metal removal); and finishing (final light cuts). Performed on lathes, turning centers, chucking machines, automatic screw machines and similar machines.