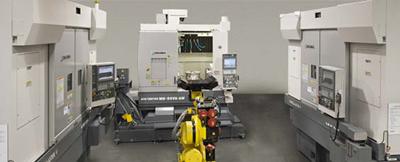
Okuma America Corp. announced the launch of the new All-Okuma wheel cell. The new wheel cell includes the new MB-56VA-AW aluminum wheel drilling machine, designed to deliver the reliability of Okuma lathes in a dedicated machining center/drill. Also included are two Okuma CNC lathes in a choice of sizes, a FANUC robot, and a variety of conveyance options, allowing for a customized cell configuration. All three Okuma machines feature the THINC-OSP open architecture CNC control for easy integration, enhanced functionality and accessibility to third-party applications. The new wheel cell is specifically designed to enable wheel manufacturers to increase productivity and efficiency while minimizing downtime.
Highlights of the New All-Okuma Wheel Cell:
MB-56VA-AW Aluminum Wheel Drilling Machine: The reliability of Okuma lathes is now available in this machining center/drill. Built based on Okuma's premier vertical machining center, it employs the latest technology and tailors the specs around the high-speed requirements of aluminum wheel drilling and milling. The integrated high-speed trunnion table provides full 4-axis machining capabilities.
Okuma CNC Lathes: With 5 wheel lathes to choose from, the Okuma machines allow for customizable cell configurations — sizes ranging from 16" to 24", featuring quick-changeover workholding providing flexible top tooling for the chuck, reducing the need for changeovers between setups.
THINC-OSP Open Architecture CNC: Because all three machines are now Okumas, all three feature the THINC-OSP control which allows fuller integration with the latest engineering simulation tools and throughout operations. Real-time monitoring and alarm notifications can now be enabled. Cell monitoring and performance reporting functions are more robust. Addition of third-party applications is now possible with this open architecture CNC control.
FANUC Robot: Proven gripper design and vision technology allows fixtureless locating and orientation, eliminating manned verification and offset probing.
Gosiger Automation, a member of Partners in THINC, expertly handles installation and service for the All-Okuma wheel cell. With a team of 50 deeply qualified experts they utilize advanced engineering and simulation tools, Controllogix and Wheel Process Monitoring to ensure end-to-end wheel cell performance.
Contact Details
Related Glossary Terms
- chuck
chuck
Workholding device that affixes to a mill, lathe or drill-press spindle. It holds a tool or workpiece by one end, allowing it to be rotated. May also be fitted to the machine table to hold a workpiece. Two or more adjustable jaws actually hold the tool or part. May be actuated manually, pneumatically, hydraulically or electrically. See collet.
- computer numerical control ( CNC)
computer numerical control ( CNC)
Microprocessor-based controller dedicated to a machine tool that permits the creation or modification of parts. Programmed numerical control activates the machine’s servos and spindle drives and controls the various machining operations. See DNC, direct numerical control; NC, numerical control.
- drilling machine ( drill press)
drilling machine ( drill press)
Machine designed to rotate end-cutting tools. Can also be used for reaming, tapping, countersinking, counterboring, spotfacing and boring.
- gang cutting ( milling)
gang cutting ( milling)
Machining with several cutters mounted on a single arbor, generally for simultaneous cutting.
- machining center
machining center
CNC machine tool capable of drilling, reaming, tapping, milling and boring. Normally comes with an automatic toolchanger. See automatic toolchanger.
- milling
milling
Machining operation in which metal or other material is removed by applying power to a rotating cutter. In vertical milling, the cutting tool is mounted vertically on the spindle. In horizontal milling, the cutting tool is mounted horizontally, either directly on the spindle or on an arbor. Horizontal milling is further broken down into conventional milling, where the cutter rotates opposite the direction of feed, or “up” into the workpiece; and climb milling, where the cutter rotates in the direction of feed, or “down” into the workpiece. Milling operations include plane or surface milling, endmilling, facemilling, angle milling, form milling and profiling.