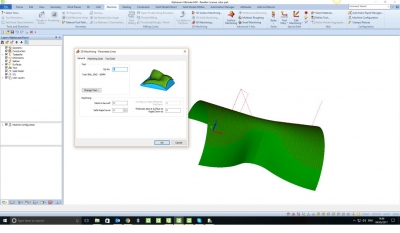
The latest release of Alphacam, from Vero Software, continues to intuitively automate key CAD/CAM operations, improving manufacturing productivity and efficiency. The Automation Manager includes enhancements to simplify workflow, including Multi-drill control, new Styles functionality, and further support for additional CAD file formats.
The introduction of Automation Manager Plus across all levels of Alphacam allows advanced automation to support the processing of Constrained Drawings and Parametric Sketches, and Part Grain Direction through sheet Grain Direction and Alignment Vector options. It also includes the Cabinet Door Manufacture (CDM) module.
Alphacam 2017 R2 also sees the first release of its integration with robot simulation software, meaning that output toolpaths generated within Alphacam can be passed directly to RoboDK’s Offline Programming (OLP) to simulate robot kinematics, along with a range of applications and activities such as robot milling. RoboDK then outputs the OLP to the robot controller.
As part of the Vero Customer Experience Improvement Program, Alphacam integrates Microsoft Analytics to gather software usage statistics.
A new Reverse Cut Direction option has been added to Rough/Finish and Stone Cut Shape, creating toolpaths in the opposite direction to the tool direction on the geometry. Alphacam Brand Manager Simon Mathias says this is particularly useful when creating multiple passes around a shape which need to go in alternate directions, such as polishing and sanding profiled edges.
For Stone, Mathias says cutting surfaces and solids with a disk has been made easier, as the user no longer has to create the work plane before starting. “The work plane can be created dynamically with on-screen feedback. Tabbed style dialogs have been introduced, and all strategies have Extents visualization of the area to be cut with dynamic cut directions and start positions.”
The Stone module now includes support for automatic detection of unsawn areas of the selected parts, and the option to add a Water Jet Cut Path operation, with two new tabs added to the sawing Dialog for the Water Jet Cut Parameters and its Lead In/Out settings.
“This is an essential addition to support the many combination Saw and Jet machines in the market,” says Mathias.
Sawing has been enhanced by controlling how the foul avoidance is applied. It can be applied to None or All of the selected machining geometries. Alternatively, a separate selection can be made for the avoidance geometries. Foul avoidance geometries appear in a new branch of the Operation tree, where geometries can be added or removed, and the selection remade.
In Alphacam’s powerful nesting function, offcuts generated from nested sheets are now written to the new Sheet Database. Sheets may have been created from the database or just-as-drawn in the active drawing. The offcut will be created under the correct sheet, matching the material and thickness, which can be viewed as Attributes on the sheet.
The new release also continues Alphacam’s theme of improving user experience by updating many Dialog boxes, including Profiling, 3D Machining, Lathe Turning Cycles and Stone, providing a more intuitive and consistent approach across the modules, to include new Images, Tooltips and Help Links.
Lathe Turning Cycles benefit from these new style dialogs for Facing, Diameter Roughing, Face Roughing, Contour Roughing and Twin Turret Balance Roughing – again, to include new Images, Tooltips and Help Links.
Support for 4K monitors has been improved with the addition of Scaling Options, to make the icons larger for higher 4K dpi settings – accessed from the Appearance section in the Ribbon Bar Configuration.
The Input CAD Extensions add-in now supports all imported file types. “And the dialog will only be displayed if the CAD file imported something that can be processed, for example, at least one instance of geometry, text or spline. Otherwise the dialog won’t be shown,” Mathias says.
There is also a new tool, which he says is useful for tidying up imported geometry from CAD formats such as DXF and DWG, where the designer may have created several overlaying entities which are used in design, but are not required for manufacturing via CNC. “This is the Common Line Removal option which has been added to the dialog, enabling it to run automatically on CAD import. It will be particularly valuable when batch processing CAD data through Automation Manager.”
In conclusion Mathias says, “The automation enhancements in Alphacam 2017 R2 assist manufacturers to improve productivity and profitability by speeding up their manufacturing processes.”
Contact Details
Related Glossary Terms
- computer numerical control ( CNC)
computer numerical control ( CNC)
Microprocessor-based controller dedicated to a machine tool that permits the creation or modification of parts. Programmed numerical control activates the machine’s servos and spindle drives and controls the various machining operations. See DNC, direct numerical control; NC, numerical control.
- computer-aided design ( CAD)
computer-aided design ( CAD)
Product-design functions performed with the help of computers and special software.
- gang cutting ( milling)
gang cutting ( milling)
Machining with several cutters mounted on a single arbor, generally for simultaneous cutting.
- lathe
lathe
Turning machine capable of sawing, milling, grinding, gear-cutting, drilling, reaming, boring, threading, facing, chamfering, grooving, knurling, spinning, parting, necking, taper-cutting, and cam- and eccentric-cutting, as well as step- and straight-turning. Comes in a variety of forms, ranging from manual to semiautomatic to fully automatic, with major types being engine lathes, turning and contouring lathes, turret lathes and numerical-control lathes. The engine lathe consists of a headstock and spindle, tailstock, bed, carriage (complete with apron) and cross slides. Features include gear- (speed) and feed-selector levers, toolpost, compound rest, lead screw and reversing lead screw, threading dial and rapid-traverse lever. Special lathe types include through-the-spindle, camshaft and crankshaft, brake drum and rotor, spinning and gun-barrel machines. Toolroom and bench lathes are used for precision work; the former for tool-and-die work and similar tasks, the latter for small workpieces (instruments, watches), normally without a power feed. Models are typically designated according to their “swing,” or the largest-diameter workpiece that can be rotated; bed length, or the distance between centers; and horsepower generated. See turning machine.
- lathe turning
lathe turning
Machining operation in which a workpiece is rotated, while a cutting tool removes material, either externally or internally.
- milling
milling
Machining operation in which metal or other material is removed by applying power to a rotating cutter. In vertical milling, the cutting tool is mounted vertically on the spindle. In horizontal milling, the cutting tool is mounted horizontally, either directly on the spindle or on an arbor. Horizontal milling is further broken down into conventional milling, where the cutter rotates opposite the direction of feed, or “up” into the workpiece; and climb milling, where the cutter rotates in the direction of feed, or “down” into the workpiece. Milling operations include plane or surface milling, endmilling, facemilling, angle milling, form milling and profiling.
- polishing
polishing
Abrasive process that improves surface finish and blends contours. Abrasive particles attached to a flexible backing abrade the workpiece.
- profiling
profiling
Machining vertical edges of workpieces having irregular contours; normally performed with an endmill in a vertical spindle on a milling machine or with a profiler, following a pattern. See mill, milling machine.
- sawing
sawing
Machining operation in which a powered machine, usually equipped with a blade having milled or ground teeth, is used to part material (cutoff) or give it a new shape (contour bandsawing, band machining). Four basic types of sawing operations are: hacksawing (power or manual operation in which the blade moves back and forth through the work, cutting on one of the strokes); cold or circular sawing (a rotating, circular, toothed blade parts the material much as a workshop table saw or radial-arm saw cuts wood); bandsawing (a flexible, toothed blade rides on wheels under tension and is guided through the work); and abrasive sawing (abrasive points attached to a fiber or metal backing part stock, could be considered a grinding operation).
- sawing machine ( saw)
sawing machine ( saw)
Machine designed to use a serrated-tooth blade to cut metal or other material. Comes in a wide variety of styles but takes one of four basic forms: hacksaw (a simple, rugged machine that uses a reciprocating motion to part metal or other material); cold or circular saw (powers a circular blade that cuts structural materials); bandsaw (runs an endless band; the two basic types are cutoff and contour band machines, which cut intricate contours and shapes); and abrasive cutoff saw (similar in appearance to the cold saw, but uses an abrasive disc that rotates at high speeds rather than a blade with serrated teeth).
- turning
turning
Workpiece is held in a chuck, mounted on a face plate or secured between centers and rotated while a cutting tool, normally a single-point tool, is fed into it along its periphery or across its end or face. Takes the form of straight turning (cutting along the periphery of the workpiece); taper turning (creating a taper); step turning (turning different-size diameters on the same work); chamfering (beveling an edge or shoulder); facing (cutting on an end); turning threads (usually external but can be internal); roughing (high-volume metal removal); and finishing (final light cuts). Performed on lathes, turning centers, chucking machines, automatic screw machines and similar machines.