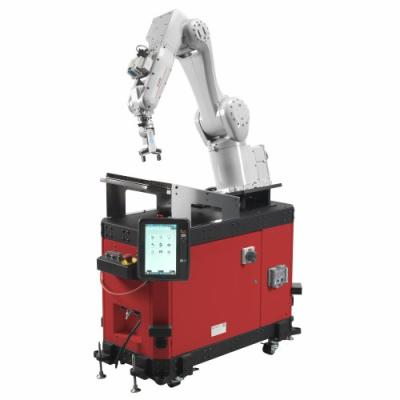
Mitsubishi Electric Automation, Inc. Launches Pre- Engineered Robot Work Cell as a Compact, Cost-Effective, and Intuitive Solution to Productivity Challenges
ARIA (Automated Robotic Industrial Assistant) has a small footprint, is fully configurable, and offers a broad array of options and preprogrammed software packages that enable the unit to be tailored to the application.
Mitsubishi Electric Automation, Inc. is proud to announce its newest pre- engineered work cell product to its existing lineup with LoadMate Plus. ARIA (Automated Robotic Industrial Assistant) is an ideal and cost-ef- fective solution to address labor shortages and productivity challenges across a multitude of industries. ARIA has a payload capacity of up to 13 kg (28.6 lbs.) and reach capabilities of 1503 mm (59.173"). It is suit- able for use as a stand-alone cell, or it can be implemented into a larger solution and offers two different base options: standard and machine tool bases.
ARIA’s Standard Base option is designed for various industry applications where flexibility and mobility are a must. The Machine Tool Base is designed for tending CNC Mill, Lathe, and Swiss applications. Both bases are suitable for Mitsubishi Electric collaborative, vertical/articulated, and SCARA robots. Included in the ARIA package is an FX5 PLC, an external 120V outlet, casters with jackscrews, a network switch with an external EtherNet port, an Operator station w/button pan- el, floor mounting brackets, and much more. Accessory add-on features include preprogrammed software packages, RT ToolBox3 software, MELFA Works for robot simulation, MELFA Safe Plus, Force Sensor, R86TB high-performance teach pendant, and two HMI options.
“ARIA fulfills an immediate need for flexible and cost-effective automation that addresses common industry problems such as labor shortages, productivity challenges, and the need to maintain quality standards. ARIA is fully configurable and mobile, making it an ideal solution to tackle multiple applications within a given facility,” said David Simak, product manager (service) at Mitsubishi Electric Automation, Inc.
Contact Details
Related Glossary Terms
- computer numerical control ( CNC)
computer numerical control ( CNC)
Microprocessor-based controller dedicated to a machine tool that permits the creation or modification of parts. Programmed numerical control activates the machine’s servos and spindle drives and controls the various machining operations. See DNC, direct numerical control; NC, numerical control.
- lathe
lathe
Turning machine capable of sawing, milling, grinding, gear-cutting, drilling, reaming, boring, threading, facing, chamfering, grooving, knurling, spinning, parting, necking, taper-cutting, and cam- and eccentric-cutting, as well as step- and straight-turning. Comes in a variety of forms, ranging from manual to semiautomatic to fully automatic, with major types being engine lathes, turning and contouring lathes, turret lathes and numerical-control lathes. The engine lathe consists of a headstock and spindle, tailstock, bed, carriage (complete with apron) and cross slides. Features include gear- (speed) and feed-selector levers, toolpost, compound rest, lead screw and reversing lead screw, threading dial and rapid-traverse lever. Special lathe types include through-the-spindle, camshaft and crankshaft, brake drum and rotor, spinning and gun-barrel machines. Toolroom and bench lathes are used for precision work; the former for tool-and-die work and similar tasks, the latter for small workpieces (instruments, watches), normally without a power feed. Models are typically designated according to their “swing,” or the largest-diameter workpiece that can be rotated; bed length, or the distance between centers; and horsepower generated. See turning machine.
- milling machine ( mill)
milling machine ( mill)
Runs endmills and arbor-mounted milling cutters. Features include a head with a spindle that drives the cutters; a column, knee and table that provide motion in the three Cartesian axes; and a base that supports the components and houses the cutting-fluid pump and reservoir. The work is mounted on the table and fed into the rotating cutter or endmill to accomplish the milling steps; vertical milling machines also feed endmills into the work by means of a spindle-mounted quill. Models range from small manual machines to big bed-type and duplex mills. All take one of three basic forms: vertical, horizontal or convertible horizontal/vertical. Vertical machines may be knee-type (the table is mounted on a knee that can be elevated) or bed-type (the table is securely supported and only moves horizontally). In general, horizontal machines are bigger and more powerful, while vertical machines are lighter but more versatile and easier to set up and operate.
- payload ( workload)
payload ( workload)
Maximum load that the robot can handle safely.