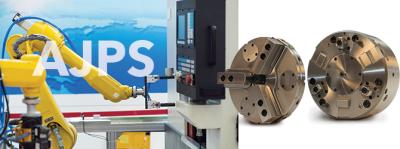
With Kitagawa/NorthTech Worlkholding's automated pallet jaw system, robotic automation is a viable solution for low- and moderate-volume parts production in a CNC lathe.
• Jaw Pallet replacing method allows you to change all 3 jaws at once by replacing entire Pallet
• Deliver your work-pieces and Jaw Pallets by Robot or Shuttle
• Flexible capabilities for automated robotic systems and continuous operations unattended
• Ideal for high mix, low volume production
• AJPS is engineered with Kitagawa quality and workmanship
• Precision high accuracy positioning and repeatability of pallet to chuck body
• Designed for protection from chips and contaminants
• Compact design uses less Z-axis space
How it works:
- The Promano Quick Change Capable Grippers on the Robots end of arm allows the Robot to change the rough part (loading) Grippers and finish part (un-loading) Grippers for as many different parts required to be machined.
- The Grippers also allow the Robot to change the Pallets (for the Workholding) for as many parts to be machined allowing total un-attended management of both part and Workholding handling.
- The Kitagawa Automated Jaw Pallet System Special Chuck and Cylinder can be installed on one or both Spindles allowing the Jaw Pallets for the rough and finish part geometries to be changed.
- The Robot loads the Pallet Gripper and inserts the Jaw Pallet into the chuck body where it is locked into place and ready for an internal or external gripping of the part.
- These Jaw Pallets are designed to maintain very close tolerance between changes allowing high accuracy and repeatability of both locating and gripping geometries.
- The Pallets are Equipped with Special Jaws and Dust covers designed to prevent any contaminants from intrusion and can be supplied with part specific engineered workholding solutions.
- The Robot then changes its Kitagawa Promano Gripper to the first part geometry to be loaded and machined.
- As the robot loads the first part to be machined the Kitagawa Automated Jaw Pallet grips it securely and accurately.
- As the machining process starts the Robot then proceeds to change the Kitagawa Promano Quick Change capable Gripper to the finish geometry.
- In this instance no change needed as both Gripers required for loading and un-loading the part or parts are on one end of Robot arm Bracket.
- As the Robot loads the next part to be machined it confirms the presence of the finished part and un-loads the finish part allowing the process to continue for any quantities needed.
- During the machining process the Robot continues with other tasks like inspection, part washing etcetera, both Machining and changing of the work handling happen internal of each other’s cycle time.
- When the desired number of parts needed to be machined is reached and the final part is un-loaded the Robot then changes its Promano Gripper to accommodate the Kitagawa Automated Jaw Pallets.
- The Robot then proceeds to equip the machine tool with the Workholding needed to machine the next group of completely different parts, in any quantity.
- The Robot then changes its Promano Gripper to the next completely different part geometry to be machined and the process is repeated all over again.
Contact Details
Related Glossary Terms
- chuck
chuck
Workholding device that affixes to a mill, lathe or drill-press spindle. It holds a tool or workpiece by one end, allowing it to be rotated. May also be fitted to the machine table to hold a workpiece. Two or more adjustable jaws actually hold the tool or part. May be actuated manually, pneumatically, hydraulically or electrically. See collet.
- computer numerical control ( CNC)
computer numerical control ( CNC)
Microprocessor-based controller dedicated to a machine tool that permits the creation or modification of parts. Programmed numerical control activates the machine’s servos and spindle drives and controls the various machining operations. See DNC, direct numerical control; NC, numerical control.
- lathe
lathe
Turning machine capable of sawing, milling, grinding, gear-cutting, drilling, reaming, boring, threading, facing, chamfering, grooving, knurling, spinning, parting, necking, taper-cutting, and cam- and eccentric-cutting, as well as step- and straight-turning. Comes in a variety of forms, ranging from manual to semiautomatic to fully automatic, with major types being engine lathes, turning and contouring lathes, turret lathes and numerical-control lathes. The engine lathe consists of a headstock and spindle, tailstock, bed, carriage (complete with apron) and cross slides. Features include gear- (speed) and feed-selector levers, toolpost, compound rest, lead screw and reversing lead screw, threading dial and rapid-traverse lever. Special lathe types include through-the-spindle, camshaft and crankshaft, brake drum and rotor, spinning and gun-barrel machines. Toolroom and bench lathes are used for precision work; the former for tool-and-die work and similar tasks, the latter for small workpieces (instruments, watches), normally without a power feed. Models are typically designated according to their “swing,” or the largest-diameter workpiece that can be rotated; bed length, or the distance between centers; and horsepower generated. See turning machine.
- tolerance
tolerance
Minimum and maximum amount a workpiece dimension is allowed to vary from a set standard and still be acceptable.