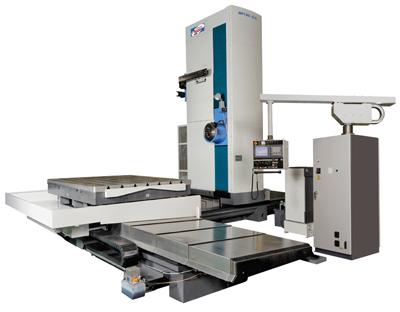
SNK America Inc. says the BP130-3.5 gives you everything you'd expect in a world-class Japanese built boring mill--superb design, robust construction and premium-grade components—but at a cost comparable to our competitor's 3.0 models.
The generous work envelope and straightforward design provide for efficient work throughput. It features heavy-duty, high quality cast iron construction throughout. Extra-wide solid boxways easily support large workpieces. Oversize ballscrews on all linear axes are precision ground and finished to deliver consistent, precise positioning even under the most demanding machining conditions.
The BP130-3.5 features a full rotary table size of 62.99 inches x 86.6 inches with a maximum workpiece load of 22,000 lbs.
X and Y axes travels are 137.80 inches x 98.43 inches respectively. The 5.1 inches boring spindle travels within the 8 inches milling spindle to provide a full 27.5 inches stroke for maximum machining flexibility. W-axis thermal growth compensation provides optimum accuracy. The X-axis table is of a single piece casting utilizing the accuracy and stability of a fully supported cast iron base. The B-axis is fully supported by a worm and wheel construction with scale feedback. The large work table has 7 T- slots to simply work fixturing.
Other features include an ATC with standard capacity of 60 tools (90, 120 optional), standard 35HP spindle motor and micro-filtration and chip conveyor system with skimmer & chip conveyor and more.
Optional features available on the BP130-3.5 include right angle head, angular attachment, facing head, U-axis CNC-controlled and pallet changer options.
The BP Series of planer type boring mills is available in four models including the BP130-3.0 with X and Y-axis travel of 118.11 inches and 78.74 inches respectively up to the largest model, the BP130-5.0 with X and Y-axis travel of 196.48 inches and 98.43 inches.
Contact Details
Related Glossary Terms
- boring
boring
Enlarging a hole that already has been drilled or cored. Generally, it is an operation of truing the previously drilled hole with a single-point, lathe-type tool. Boring is essentially internal turning, in that usually a single-point cutting tool forms the internal shape. Some tools are available with two cutting edges to balance cutting forces.
- gang cutting ( milling)
gang cutting ( milling)
Machining with several cutters mounted on a single arbor, generally for simultaneous cutting.
- milling
milling
Machining operation in which metal or other material is removed by applying power to a rotating cutter. In vertical milling, the cutting tool is mounted vertically on the spindle. In horizontal milling, the cutting tool is mounted horizontally, either directly on the spindle or on an arbor. Horizontal milling is further broken down into conventional milling, where the cutter rotates opposite the direction of feed, or “up” into the workpiece; and climb milling, where the cutter rotates in the direction of feed, or “down” into the workpiece. Milling operations include plane or surface milling, endmilling, facemilling, angle milling, form milling and profiling.
- planing machine ( planer)
planing machine ( planer)
Machines flat surfaces. Planers take a variety of forms: double-housing, open-side, convertible and adjustable open-side, double-cut and milling. Large multihead (milling, boring, drilling, etc.) planers and planer-type milling machines handle most planing work.
- work envelope
work envelope
Cube, sphere, cylinder or other physical space within which the cutting tool is capable of reaching.