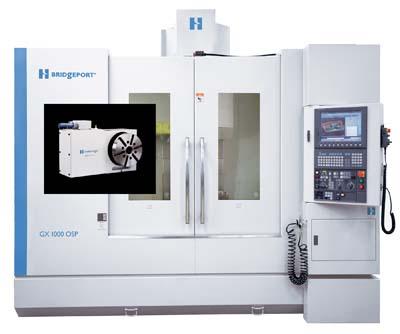
Hardinge and Bridgeport make it easy to select and connect a rotary device to the vertical machining center for precision fourth-axis parts positioning. Hardinge fourth-axis rotary tables will increase the machine capability with rapid positioning speeds and fast job changeover. The rigid design characteristics of the machine and the quick-change spindle nose design of the rotary device offer a rugged and flexible fourth-axis machining option.
The Bridgeport GX 1000 OSP high-performance machining center is unique to the Bridgeport family of mills as it incorporates the Okuma OSP P200 CNC control, encoders, motors, and drives. The GX 1000's popularity has risen over the years as a true workhorse in the industry, and with the addition of the OSP P200 control, this machine offers even more performance capabilities. The advanced architecture of the OSP-P200 NC control enables access to almost any application and peripheral, including factory management systems, and will interface with bar coders, feeders, robots, probes and tool setters to help streamline production.
The stiff and thermally stable spindle, rigid C-frame fixed column design, and fixed pretensioned double nut ball screws on all axes of the machining center, provide superior rigidity, accuracy and repeatability. Hardinge provides a smooth integration of their precision rotary tables into the GX 1000 OSP, to operate in a fully interpolated fashion with the other axes of the machine. Hardinge rotary packages include the Okuma motor and cables to connect via fourth-axis to the new, pre-wired Bridgeport GX 1000 vertical machining center with an OSP control. The new Bridgeport VMC must be prewired to accept the rotary package. Rotary systems can also be operated using just the Hardinge servo control if true fourth-axis is not required. Hardinge has a large selection of rotary products that are compatible with the Bridgeport GX 1000 OSP machining center including single and multi-spindle units.
Hardinge rotary products incorporate an A2-4, A2-5 or 5C threaded-nose collet-ready spindle that will accept collets, expanding collets, step chucks and chucks (as well as the traditional faceplate) to expand part gripping capabilities and improve part accuracies. The generous 44.09" x 21.25" machine table provides plenty of room for a rotary table and a vise to allow maximum job flexibility.
Contact Details
Related Glossary Terms
- computer numerical control ( CNC)
computer numerical control ( CNC)
Microprocessor-based controller dedicated to a machine tool that permits the creation or modification of parts. Programmed numerical control activates the machine’s servos and spindle drives and controls the various machining operations. See DNC, direct numerical control; NC, numerical control.
- machining center
machining center
CNC machine tool capable of drilling, reaming, tapping, milling and boring. Normally comes with an automatic toolchanger. See automatic toolchanger.
- numerical control ( NC)
numerical control ( NC)
Any controlled equipment that allows an operator to program its movement by entering a series of coded numbers and symbols. See CNC, computer numerical control; DNC, direct numerical control.