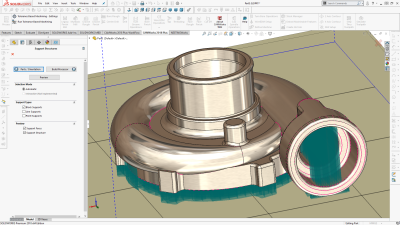
HCL Technologies announced the release of CAMWorks Version 2019, which includes Additive Manufacturing, Tolerance-Based Machining (TBM) for turn and mill/turn parts, and improvements to Technology Database (TechDB).
CAMWorks Additive Manufacturing, powered by Materialise technology, introduces the first additive-subtractive solution available for SOLIDWORKS to allow users to prepare models for their 3D metal printers inside SOLIDWORKS. The 3D printer model is then used as stock, and CAMWorks will generate the CNC subtractive machining operations and toolpaths needed to remove the build supports and machine other user-defined areas of the part, all inside of SOLIDWORKS. The design, additive and subtractive information are all stored within a single file, making it fully associative with the SOLIDWORKS model. Design changes made will subsequently be updated in the additive and subtractive programming.
CAMWorks 2019 also expands Tolerance-Based Machining (TBM) to turn and mill/turn parts, now with full integration inside CAMWorks. Tolerance-Based Machining provides technology to help users move their programming to Industry 4.0 procedures by recognizing and using Product and Manufacturing Information (PMI) – such as GD&T dimensions, notes and callouts – as well as Model Based Definition (MBD) information in the 3D model. With this information in the 3D model, users can eliminate the cost and manual tasks involved when using 2D drawings, and dramatically reduce the time needed to generate CNC programs for parts with close tolerances and surface finish requirements. CAMWorks TBM automatically selects the correct machining strategies to meet the tolerance requirements, and because it is fully associative with SOLIDWORKS, any tolerance changes made to the model will automatically be updated in the CNC programming.
CAMWorks 2019 also provides several improvements to TechDB – the CAMWorks Technology Database that captures programmers’ best practices and allows them to save and reuse the information that defines how they prefer to machine parts. With TechDB, users can define their preferred tools, speeds and feeds, machining strategies and associative parameters for the CNC machines on their shop floor. In addition, the TechDB can be shared with other programmers and designers working together, saving programming time and standardizing output quality.
Among the additional enhancements released in CAMWorks 2019 are significant improvements to 5-axis swarf milling, multiple-turret synchronization, production multiple-turret turning, toolpath editing, collision checking, multiple-axis chamfer milling and additional feature recognition functionality.
Contact Details
Related Glossary Terms
- computer numerical control ( CNC)
computer numerical control ( CNC)
Microprocessor-based controller dedicated to a machine tool that permits the creation or modification of parts. Programmed numerical control activates the machine’s servos and spindle drives and controls the various machining operations. See DNC, direct numerical control; NC, numerical control.
- gang cutting ( milling)
gang cutting ( milling)
Machining with several cutters mounted on a single arbor, generally for simultaneous cutting.
- milling
milling
Machining operation in which metal or other material is removed by applying power to a rotating cutter. In vertical milling, the cutting tool is mounted vertically on the spindle. In horizontal milling, the cutting tool is mounted horizontally, either directly on the spindle or on an arbor. Horizontal milling is further broken down into conventional milling, where the cutter rotates opposite the direction of feed, or “up” into the workpiece; and climb milling, where the cutter rotates in the direction of feed, or “down” into the workpiece. Milling operations include plane or surface milling, endmilling, facemilling, angle milling, form milling and profiling.
- swarf
swarf
Metal fines and grinding wheel particles generated during grinding.
- tolerance
tolerance
Minimum and maximum amount a workpiece dimension is allowed to vary from a set standard and still be acceptable.
- toolpath( cutter path)
toolpath( cutter path)
2-D or 3-D path generated by program code or a CAM system and followed by tool when machining a part.
- turning
turning
Workpiece is held in a chuck, mounted on a face plate or secured between centers and rotated while a cutting tool, normally a single-point tool, is fed into it along its periphery or across its end or face. Takes the form of straight turning (cutting along the periphery of the workpiece); taper turning (creating a taper); step turning (turning different-size diameters on the same work); chamfering (beveling an edge or shoulder); facing (cutting on an end); turning threads (usually external but can be internal); roughing (high-volume metal removal); and finishing (final light cuts). Performed on lathes, turning centers, chucking machines, automatic screw machines and similar machines.