Contact Details
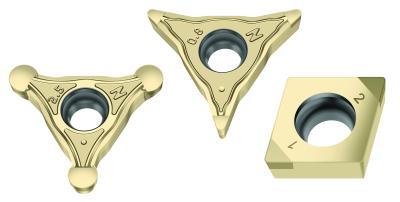
Walter has introduced the CBN grade WBH20C indexable inserts for hard machining with a high level of wear resistance. This capability is possible due to a combination of ultrapure CBN and a new patent pending TiAlN (titanium aluminum nitride) PVD HiPIMS (high-power impulse magnetron sputtering) coating with a ZrN (zirconium nitride) top layer.
The application range for the CBN-tipped inserts includes hard steels (ISO H) up to 65 HRC.
Excellent layer bonding and long tool life is possible due to the patent pending method for pretreating the indexable insert. Exceptional wear detection is provided by the light-colored top coating.
The ISO indexable inserts are available with or without the MW wiper geometry. They are available in the basic shapes of CCGW2…, CCGW3…, CNGA4…, DCGW3…, DNGA4…, TCGW2…, VCGW2… and VBGW3….
In addition, the WBH20C WL25 indexable inserts are full-radius copy turning inserts with Walter Lock positive engagement. The WL positive engagement provides maximum stability and precision for reliable machining of contours. With pocket support right under the cutting edge, and exceptional ability to prevent vibrations; the WL positive engagement is substantially better than the conventional V-shaped or even full radius grooving inserts.
The WBH20C grade features a 65 percent CBN content, a ceramic binder and bimodal grain size with a diameter of less than 39 millionths/159 millionths of an inch (1.0 µm/4.0 µm). Maximum purity of the CBN substrate is used.
Typically, hard turning is highly recommended to be a dry application, however, if the machining process constraints mandate the coolant to be “ON,” then the WBH20C is a very effective grade for wet-turning applications The CBN indexable inserts are suitable and recommended for use with coolant. Examples of workpiece material recommendations include bearing steel, such as AISI 52100 (100Cr6), and heat treatable steels, such as AISI 1045 and AISI 4140. The use of CBN grade WBH20C indexable inserts replaces grinding in many application areas, such as when turning gears.
Related Glossary Terms
- coolant
coolant
Fluid that reduces temperature buildup at the tool/workpiece interface during machining. Normally takes the form of a liquid such as soluble or chemical mixtures (semisynthetic, synthetic) but can be pressurized air or other gas. Because of water’s ability to absorb great quantities of heat, it is widely used as a coolant and vehicle for various cutting compounds, with the water-to-compound ratio varying with the machining task. See cutting fluid; semisynthetic cutting fluid; soluble-oil cutting fluid; synthetic cutting fluid.
- cubic boron nitride ( CBN)
cubic boron nitride ( CBN)
Crystal manufactured from boron nitride under high pressure and temperature. Used to cut hard-to-machine ferrous and nickel-base materials up to 70 HRC. Second hardest material after diamond. See superabrasive tools.
- grinding
grinding
Machining operation in which material is removed from the workpiece by a powered abrasive wheel, stone, belt, paste, sheet, compound, slurry, etc. Takes various forms: surface grinding (creates flat and/or squared surfaces); cylindrical grinding (for external cylindrical and tapered shapes, fillets, undercuts, etc.); centerless grinding; chamfering; thread and form grinding; tool and cutter grinding; offhand grinding; lapping and polishing (grinding with extremely fine grits to create ultrasmooth surfaces); honing; and disc grinding.
- grooving
grooving
Machining grooves and shallow channels. Example: grooving ball-bearing raceways. Typically performed by tools that are capable of light cuts at high feed rates. Imparts high-quality finish.
- hard turning
hard turning
Single-point cutting of a workpiece that has a hardness value higher than 45 HRC.
- indexable insert
indexable insert
Replaceable tool that clamps into a tool body, drill, mill or other cutter body designed to accommodate inserts. Most inserts are made of cemented carbide. Often they are coated with a hard material. Other insert materials are ceramic, cermet, polycrystalline cubic boron nitride and polycrystalline diamond. The insert is used until dull, then indexed, or turned, to expose a fresh cutting edge. When the entire insert is dull, it is usually discarded. Some inserts can be resharpened.
- physical vapor deposition ( PVD)
physical vapor deposition ( PVD)
Tool-coating process performed at low temperature (500° C), compared to chemical vapor deposition (1,000° C). Employs electric field to generate necessary heat for depositing coating on a tool’s surface. See CVD, chemical vapor deposition.
- titanium aluminum nitride ( TiAlN)
titanium aluminum nitride ( TiAlN)
Often used as a tool coating. AlTiN indicates the aluminum content is greater than the titanium. See coated tools.
- turning
turning
Workpiece is held in a chuck, mounted on a face plate or secured between centers and rotated while a cutting tool, normally a single-point tool, is fed into it along its periphery or across its end or face. Takes the form of straight turning (cutting along the periphery of the workpiece); taper turning (creating a taper); step turning (turning different-size diameters on the same work); chamfering (beveling an edge or shoulder); facing (cutting on an end); turning threads (usually external but can be internal); roughing (high-volume metal removal); and finishing (final light cuts). Performed on lathes, turning centers, chucking machines, automatic screw machines and similar machines.
- wear resistance
wear resistance
Ability of the tool to withstand stresses that cause it to wear during cutting; an attribute linked to alloy composition, base material, thermal conditions, type of tooling and operation and other variables.
- wiper
wiper
Metal-removing edge on the face of a cutter that travels in a plane perpendicular to the axis. It is the edge that sweeps the machined surface. The flat should be as wide as the feed per revolution of the cutter. This allows any given insert to wipe the entire workpiece surface and impart a fine surface finish at a high feed rate.