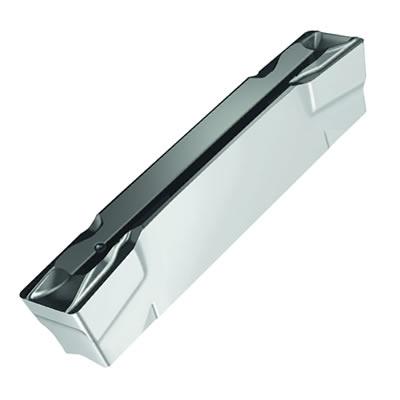
Walter has introduced three new Walter Cut GX Tiger·tec Silver CVD grooving and parting grades—the WKP13S, WKP23S and WKP33S—for use on steel and cast-iron applications. These have been introduced in combination with Walter's geometries UD4, UA4, UF4, RD4 along with plunge grooving and parting geometries GD3 and CE4. This advanced grade and geometry combination is enhanced by the latest developments in a wear-resistant cutting material that boosts cutting parameters while maintaining or improving tool life.
The new, thicker Tiger·tec Silver CVD coating used with the WKP grades features aluminum oxide with optimized microstructure for maximum crater wear resistance and enhanced cutting speed due, in part, to reduced friction. A new silver flank face permits easy wear detection and full cutting-edge usage. In addition, a second-generation mechanical post-treatment creates compressive stresses that enhance toughness, reducing the chance of chipping on the cutting edge thereby boosting load capability and metal-removal rates.
The WKP13S is for use under good machining conditions, primarily on steels such as high alloy, bearing and carbon steels as well as gray cast irons, ductile irons and compacted graphite cast irons. This grade delivers excellent wear resistance and cutting speed, especially in continuous cuts. WKP23S is a universal grade for a variety of applications, from continuous cutting on bar stock to machining interrupted cuts. It delivers superior wear resistance and cutting speed. WKP33S provides maximum toughness during unfavorable machining conditions.
Contact Details
Related Glossary Terms
- aluminum oxide
aluminum oxide
Aluminum oxide, also known as corundum, is used in grinding wheels. The chemical formula is Al2O3. Aluminum oxide is the base for ceramics, which are used in cutting tools for high-speed machining with light chip removal. Aluminum oxide is widely used as coating material applied to carbide substrates by chemical vapor deposition. Coated carbide inserts with Al2O3 layers withstand high cutting speeds, as well as abrasive and crater wear.
- carbon steels
carbon steels
Known as unalloyed steels and plain carbon steels. Contains, in addition to iron and carbon, manganese, phosphorus and sulfur. Characterized as low carbon, medium carbon, high carbon and free machining.
- cast irons
cast irons
Cast ferrous alloys containing carbon in excess of solubility in austenite that exists in the alloy at the eutectic temperature. Cast irons include gray cast iron, white cast iron, malleable cast iron and ductile, or nodular, cast iron. The word “cast” is often left out.
- chemical vapor deposition ( CVD)
chemical vapor deposition ( CVD)
High-temperature (1,000° C or higher), atmosphere-controlled process in which a chemical reaction is induced for the purpose of depositing a coating 2µm to 12µm thick on a tool’s surface. See coated tools; PVD, physical vapor deposition.
- cutting speed
cutting speed
Tangential velocity on the surface of the tool or workpiece at the cutting interface. The formula for cutting speed (sfm) is tool diameter 5 0.26 5 spindle speed (rpm). The formula for feed per tooth (fpt) is table feed (ipm)/number of flutes/spindle speed (rpm). The formula for spindle speed (rpm) is cutting speed (sfm) 5 3.82/tool diameter. The formula for table feed (ipm) is feed per tooth (ftp) 5 number of tool flutes 5 spindle speed (rpm).
- gray cast irons
gray cast irons
Alloys of iron, carbon and silicon in which more carbon is present than can be retained in austenite. The carbon in excess of austenite solubility in iron precipitates as graphite flakes. Approximate composition of gray irons is: 2.5 to 4.0 percent carbon, 0.5 to 1.0 percent manganese, 1.0 to 3.0 percent silicon, 0.05 to 0.15 percent sulfur and 0.05 to 0.8 percent phosphorus. Some Society of Automotive Engineer grades are G-1800, G-2500, G-3000, G-3500 and G-4000.
- grooving
grooving
Machining grooves and shallow channels. Example: grooving ball-bearing raceways. Typically performed by tools that are capable of light cuts at high feed rates. Imparts high-quality finish.
- microstructure
microstructure
Structure of a metal as revealed by microscopic examination of the etched surface of a polished specimen.
- parting
parting
When used in lathe or screw-machine operations, this process separates a completed part from chuck-held or collet-fed stock by means of a very narrow, flat-end cutting, or parting, tool.
- wear resistance
wear resistance
Ability of the tool to withstand stresses that cause it to wear during cutting; an attribute linked to alloy composition, base material, thermal conditions, type of tooling and operation and other variables.