Contact Details
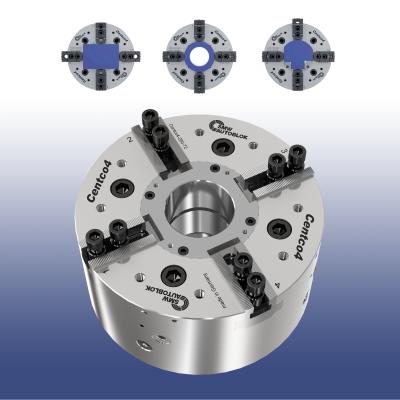
SMW Autoblok introduces the versatile four-in-one Centco4 2+2 self-centering and compensating chuck. The Centco4’s engineering and flexibility enables it to securely and efficiently clamp virtually any type or shape of geometric part including round, cubic, angular and irregular.
The Centco4 is available in both power and manual models and is suitable for deformation-sensitive workpieces. The four-jaw Centco4 provides four times less deformation as compared with three-jaw clamping and can be used on all industry-specific machine tools. The ability to handle virtually any part shape means fewer chuck changeouts and vastly reduced downtime. Diverse manual and hydraulic applications include turning, milling, inspection and finishing operations.
“Some of the many Centco4 benefits are that it features two independent self-centering and compensating jaws and single wedge actuation that eliminates the need for a dual-piston cylinder,” said Larry Robbins, president of SMW Autoblok’s Commercial division. “The precision product delivers unlimited flexibility and is perfect for aerospace and automotive companies who are looking for one standard chuck that can clamp any part geometry.”
The drive of the Centco4 moves toward or apart on two parallel axes and needs only one standard stroke single piston cylinder for actuation. This allows for independent, self-centering clamping via both axes. Centrifugal force compensation allows for maximum rotational speeds with up to 210 kn of gripping force with optimized lubrication system that saves both time and money in repairs and maintenance. Three sizes are available in the power version including: 210-52, 260-72, 315-92 and 400-112. A variety of synchron precision jaws are offered with a 1/16th x 90° interface.
Related Glossary Terms
- chuck
chuck
Workholding device that affixes to a mill, lathe or drill-press spindle. It holds a tool or workpiece by one end, allowing it to be rotated. May also be fitted to the machine table to hold a workpiece. Two or more adjustable jaws actually hold the tool or part. May be actuated manually, pneumatically, hydraulically or electrically. See collet.
- gang cutting ( milling)
gang cutting ( milling)
Machining with several cutters mounted on a single arbor, generally for simultaneous cutting.
- milling
milling
Machining operation in which metal or other material is removed by applying power to a rotating cutter. In vertical milling, the cutting tool is mounted vertically on the spindle. In horizontal milling, the cutting tool is mounted horizontally, either directly on the spindle or on an arbor. Horizontal milling is further broken down into conventional milling, where the cutter rotates opposite the direction of feed, or “up” into the workpiece; and climb milling, where the cutter rotates in the direction of feed, or “down” into the workpiece. Milling operations include plane or surface milling, endmilling, facemilling, angle milling, form milling and profiling.
- parallel
parallel
Strip or block of precision-ground stock used to elevate a workpiece, while keeping it parallel to the worktable, to prevent cutter/table contact.
- turning
turning
Workpiece is held in a chuck, mounted on a face plate or secured between centers and rotated while a cutting tool, normally a single-point tool, is fed into it along its periphery or across its end or face. Takes the form of straight turning (cutting along the periphery of the workpiece); taper turning (creating a taper); step turning (turning different-size diameters on the same work); chamfering (beveling an edge or shoulder); facing (cutting on an end); turning threads (usually external but can be internal); roughing (high-volume metal removal); and finishing (final light cuts). Performed on lathes, turning centers, chucking machines, automatic screw machines and similar machines.