Contact Details
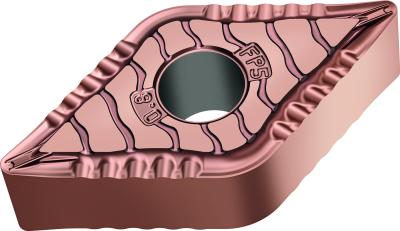
Walter has introduced a new cermet turning insert that deliver superior surface finish with reduced vibration. The new PVD coated cermet grade WEP10C, along with low cutting pressure from its negative clearance FP5 geometry and cutting-edge preparation, can boost productivity and dimensional stability in mass production. Primary application is steel (ISO P) with secondary application in stainless steel (ISO M) and cast iron (ISO K).
Also, the new FP5 geometry allows inserts well suited for finishing with continuous and slightly interrupted cuts, and unparalleled wear resistance.
These indexable turning inserts are designed for applications where a soft cut and high precision is required. Long tool life is achieved through the WEP10C coated cermet grade with multilayer PVD TiCN TiAlN coating and extra fine cermet substrate grain. Walter's combination of edge preparation and grade also ensures dimensional stability. Primary applications include energy, automotive, and general metalworking.
In addition to the negative clearance geometry FP5, the WEP10C grade cermet inserts are also available in positive clearance FP2 and FP4 geometries, The FP4 geometry is ideal for finishing operations with visibly shiny surface finish, while the FP2 geometry is ideal for small diameters, fine boring and in general any application that requires a sharper cutting edge. The grade WEP10C is offered in most common ISO shaped inserts including C, D, S, T, V, and W.
Related Glossary Terms
- boring
boring
Enlarging a hole that already has been drilled or cored. Generally, it is an operation of truing the previously drilled hole with a single-point, lathe-type tool. Boring is essentially internal turning, in that usually a single-point cutting tool forms the internal shape. Some tools are available with two cutting edges to balance cutting forces.
- clearance
clearance
Space provided behind a tool’s land or relief to prevent rubbing and subsequent premature deterioration of the tool. See land; relief.
- edge preparation
edge preparation
Conditioning of the cutting edge, such as a honing or chamfering, to make it stronger and less susceptible to chipping. A chamfer is a bevel on the tool’s cutting edge; the angle is measured from the cutting face downward and generally varies from 25° to 45°. Honing is the process of rounding or blunting the cutting edge with abrasives, either manually or mechanically.
- metalworking
metalworking
Any manufacturing process in which metal is processed or machined such that the workpiece is given a new shape. Broadly defined, the term includes processes such as design and layout, heat-treating, material handling and inspection.
- physical vapor deposition ( PVD)
physical vapor deposition ( PVD)
Tool-coating process performed at low temperature (500° C), compared to chemical vapor deposition (1,000° C). Employs electric field to generate necessary heat for depositing coating on a tool’s surface. See CVD, chemical vapor deposition.
- titanium aluminum nitride ( TiAlN)
titanium aluminum nitride ( TiAlN)
Often used as a tool coating. AlTiN indicates the aluminum content is greater than the titanium. See coated tools.
- titanium carbonitride ( TiCN)
titanium carbonitride ( TiCN)
Often used as a tool coating. See coated tools.
- turning
turning
Workpiece is held in a chuck, mounted on a face plate or secured between centers and rotated while a cutting tool, normally a single-point tool, is fed into it along its periphery or across its end or face. Takes the form of straight turning (cutting along the periphery of the workpiece); taper turning (creating a taper); step turning (turning different-size diameters on the same work); chamfering (beveling an edge or shoulder); facing (cutting on an end); turning threads (usually external but can be internal); roughing (high-volume metal removal); and finishing (final light cuts). Performed on lathes, turning centers, chucking machines, automatic screw machines and similar machines.
- wear resistance
wear resistance
Ability of the tool to withstand stresses that cause it to wear during cutting; an attribute linked to alloy composition, base material, thermal conditions, type of tooling and operation and other variables.